Air cargo handling on the ramp is a ground handling operation involving a lot of hustle on the ramp. It involves significantly greater movement of men, machines and material than other ramp operations. Therefore, air cargo handling is an operation that calls for dedicated safety precautions.
On 6th January 2018, at Jomo Kenyatta International Airport in Kenya, Etihad Airways aircraft Airbus A320-200 was parked at the aircraft stand getting ready for departure to Abu Dhabi airport. During baggage loading on the ramp, the belt loader underwent uncontrolled motion and collided with the aircraft’s starboard side engine. Both belt loader and the aircraft sustained damages.
While we’ll discuss the reason of above ramp accident shortly in this article, the accident expresses the importance of observing safety precautions while cargo handling and baggage handling on the ramp.
We have a dedicated article on explaining the basic procedure of aircraft cargo loading and unloading with focus on the equipment used in the process. Therefore, we will not repeat that in this article. This article focuses on discussing the safety aspects of air cargo handling operation on the ramp.
Safety Precautions in Handling Cargo Dollies
In air cargo loading, handling staff (also known as air cargo handlers) has to bring the filled-up Unit Load Devices (ULDs) or packed cargo pallets on the ramp by making a train of ULDs over cargo dollies hooked to each other behind a towing tractor. Safety precautions begin the moment this train of ULDs is set in motion.
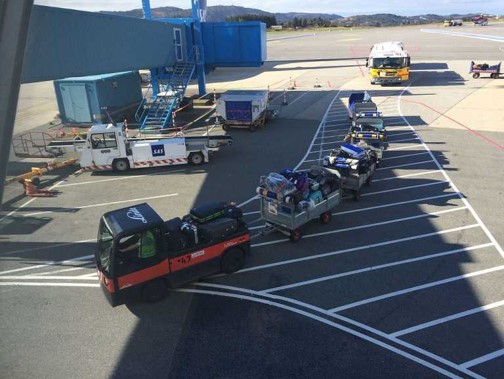
Cargo and baggage loading is a task bearing a lot of time pressure on ramp staff because any delay in these activities directly results in flight delay. Therefore, there is a tendency in handling staff of neglecting safety measures while handling cargo and baggage.
One of the temptations for air cargo handlers is to make a long train of cargo dollies so that their trips between the ramp and baggage carousel area are minimized. However, a longer than normal train would be:
- harder to control and steer;
- have a much greater turning radius; and
- the driver wouldn’t be able to really notice if something falls off on a far behind cargo dolly.
For the above reasons, ramp supervisor must be strict not to allow a train of cargo dollies bearing greater number of units than allowable as per airline, ground handling company or airport policy. Generally, any train greater than 5 or 6 cargo dollies is too long from a safety perspective.
Cargo dollies are designed for transporting ULDs and cargo pallets. They have special locks to hold the ULD or cargo pallet in place and prevent it from sliding off and falling on the road during movement and turns of the train. Staff must not forget to properly secure the ULDs and cargo pallets on the cargo dollies with the help of these locks before beginning the towing action.
All too often, the staff hurries and does not properly secure the load over cargo dolly. Consequently, the ULD falls off the cargo dolly while the towing tractor takes a turn. This falling-off of the load from the cargo dolly during a turn is especially dangerous during airport peak traffic hours when there is a lot of movement on airside.
The ULD that falls off the dolly can collide with another vehicle driving close by. In case of cargo pallets, the net must properly wrap the load so that during motion, nothing falls off the pallet.
Another important safety aspect is not to leave the cargo dollies without checking that their brake locks are in place. That is so because on many occasions, a train of cargo dollies may be left without a towing tractor. When that happens, the cargo dollies need to have fully functional braking locks to prevent their movement under wind or any other external force.
An unrestrained train of cargo dollies is dangerous for nearby equipment because it can move unchecked and collide with any object.
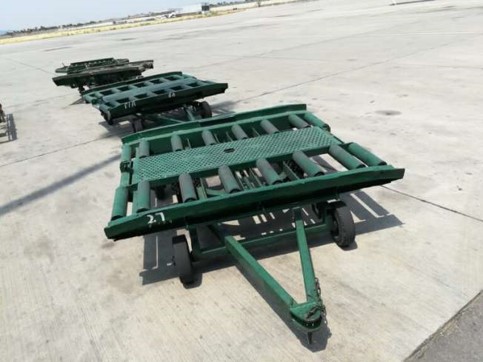
Safety Precautions in Operating Cargo Loaders
While a towing tractor brings the train of cargo dollies loaded with ULDs and cargo pallets to the aircraft stand, cargo Loader is driven to the ramp and aligned with the aircraft cargo door. There are certain safety precautions to be observed while driving the cargo loader.
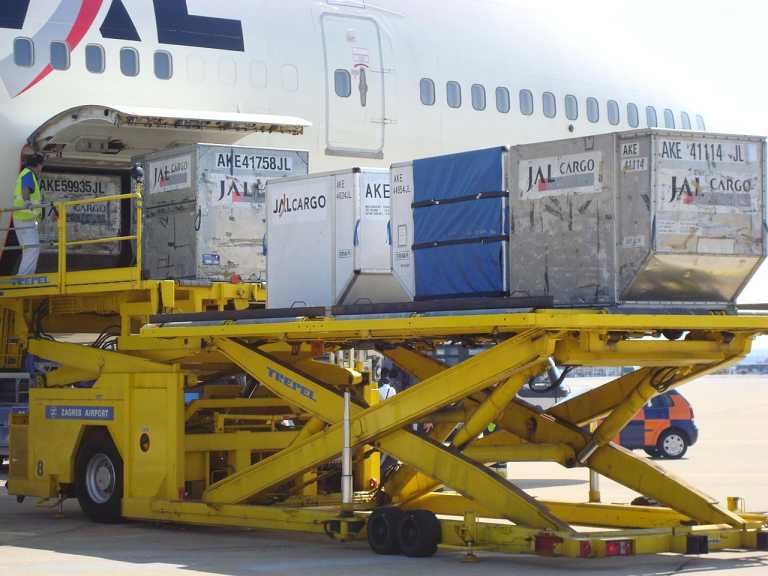
First, Cargo loaders must never be driven under the wing of the aircraft. They must be driven clear of the wings because their width and height both are a safety hazard with respect to collision with the aircraft.
Secondly, Cargo loader bridge bumper must not press hard against the aircraft body. It should have a gap of an inch or two from the aircraft body. Many modern cargo loaders come equipped with sensors that sense the contact between the bumper and aircraft body. These sensors cut off cargo loader movement when bumper touches the aircraft.
Similarly, Cargo loaders can also have radar based sensors that sense if the cargo loader is in close proximity of the aircraft. If it is, the cargo loader control system automatically slows the cargo loader down and restricts its high speed mode so that operator is bound to approach the aircraft with a very slow speed.
Correct alignment of cargo loader with the aircraft cargo compartment is also necessary for safety. For this purpose, cargo loader operator may also take assistance of another guide person standing on ground guiding him from a different angle. After correct alignment is ensured, cargo loader bridge is raised and brought in level with the aircraft cargo door.
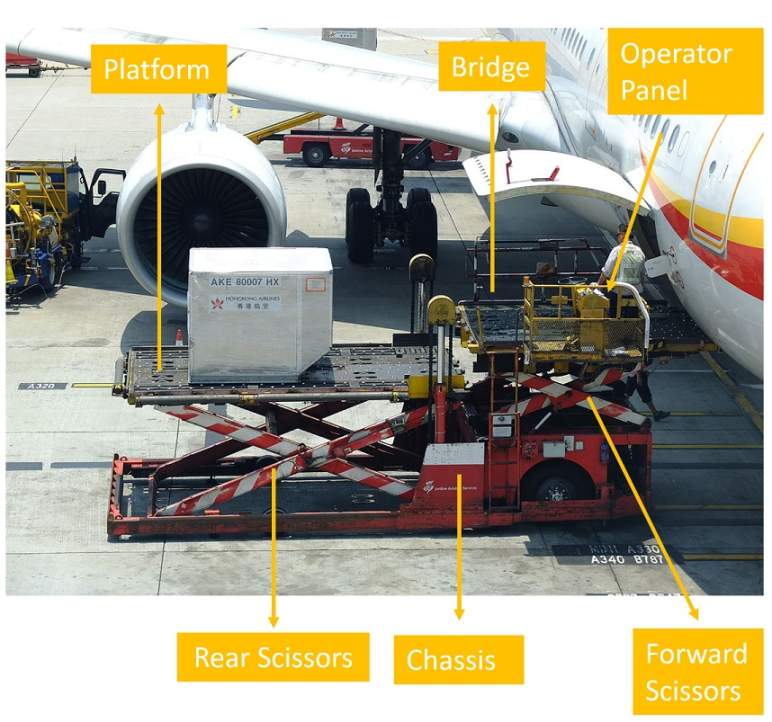
The first thing that must be done as soon as the bridge is levelled with the door is to extend the cargo loader bridge safety rails. This safety precaution is of paramount importance in air cargo handling on the ramp. While it is a general safety precaution to use a safety harness whenever working at heights, safety harness is not feasible in cargo loader because the operator has a lot of area to move on.
Secondly, the harness can get caught in the automated rolling mechanism of cargo loader and cause a serious injury. Apart from that, aprons can get dangerously windy. Therefore, the only safety on a cargo loader to prevent someone from falling-off a height are the safety rails.
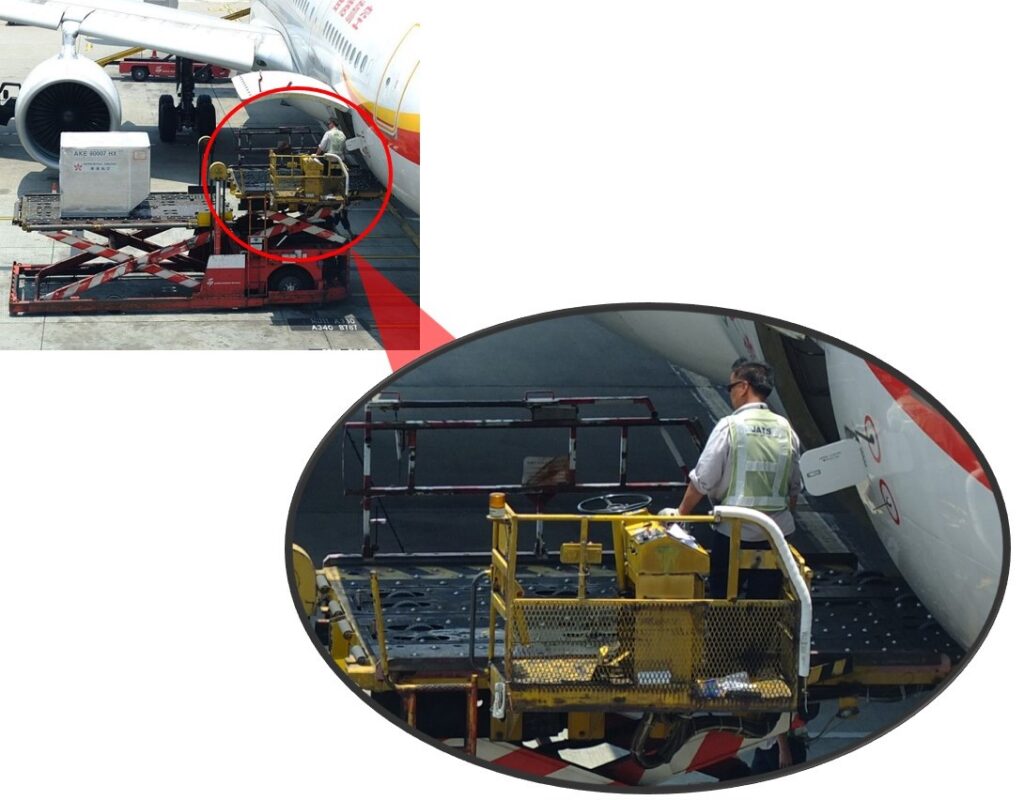
Once the cargo loader is all set up and ULDs or cargo pallets have reached the aircraft stand, the next step in cargo loading is labor intensive. Staff has to push the ULDs or cargo pallets over to the cargo loader platform. In order to make sure smooth sliding of the ULD, cargo dolly and height loader must be aligned properly as well as be on the same height level.
Height level of the cargo dolly cannot be changed therefore levelling the height is dependent on the cargo loader operator. If the cargo loader platform is not levelled with the cargo dolly, the ULD or cargo pallet being pushed on the cargo loader platform could slide back and injure the loading staff. ULDs and cargo pallets are heavy and can easily weigh several hundred kilograms that can cause a serious injury.
After loading up ULDs on the cargo loader platform, the cargo loader operator raises the platform to bring it at the same level as the bridge. During the raising of the platform, staff on ground should keep a distance from the platform to keep themselves safe in case any load falls off.
The cargo loader operator uses the motorized rolling system of cargo loader platform and bridge to transfer the load into the aircraft and lowers the platform for loading of the next batch of ULDs or cargo pallets. During the loading, unloading and handling of cargo, none of the air cargo handlers should be wearing loose clothing.
The design of the cargo loader platform, cargo dolly and the dynamics of the air cargo loading procedure are such that loose clothing could get entangled in any wheel, roller or lock that could cause an injury.
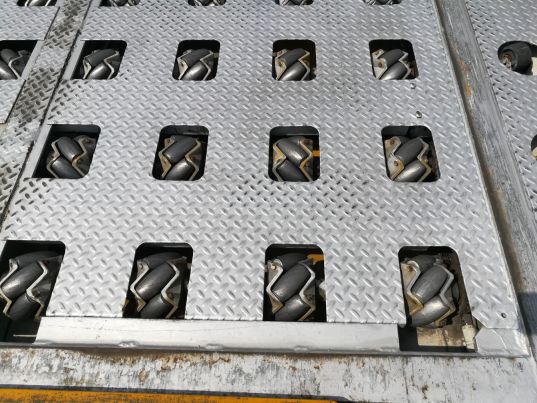
Safety Precautions in Baggage Loading on an Aircraft
Baggage loading refers to loading up the aircraft’s cargo compartment with bags, suitcases and other passenger luggage. Baggage loading is carried out by a specialized machine known as the Belt Loader or Conveyor Belt Loader.
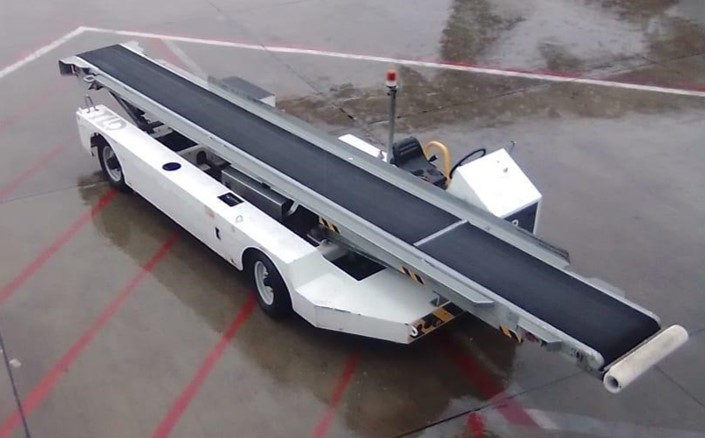
Just like cargo dollies bring the ULDs in cargo loading, baggage carts are used to stack up the passenger luggage in it from the airport’s baggage carousel. Subsequently, a towing tractor tows a train of baggage carts to the ramp where ramp staff manually unloads the bags and luggage pieces over to the conveyor while another person sitting inside the cargo compartment places them properly inside the compartment.
The first and foremost safety precaution in baggage handling is to load bags and not throw bags on the conveyor belt. Since the bags and luggage pieces are heavy and nature of job is laborious and mundane, baggage staff has the tendency to just get it over with and toss the luggage pieces over to the conveyor belt.
The above practice not only falls under mishandling of baggage but is dangerous from multiple aspects:
- The first is the risk of the luggage pieces being thrown falling and hitting something or someone.
- Second is the breaking off of the plastic parts, zips and other small components of trolley bags, suitcases and other luggage pieces that become Foreign Object Debris (FOD) on apron.
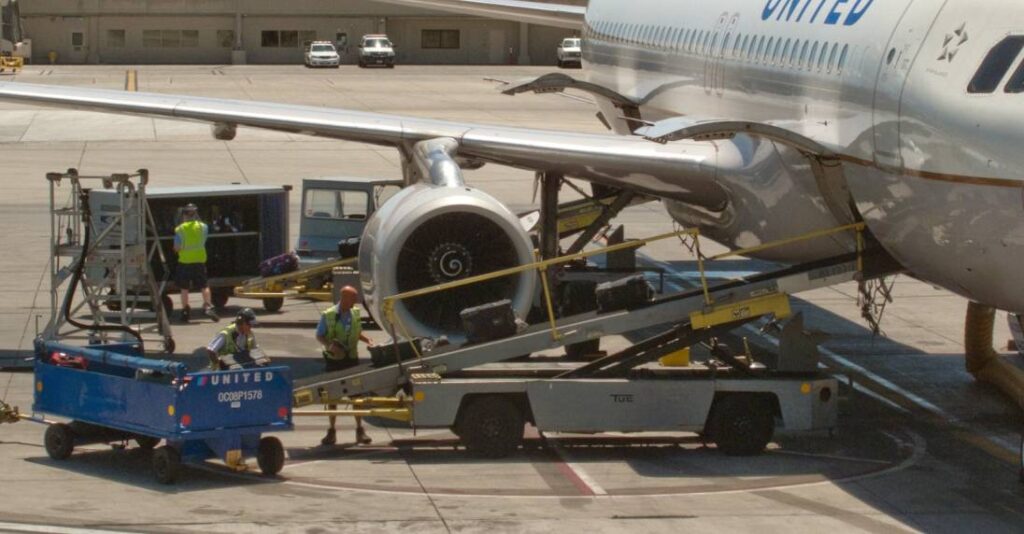
It is important to remember that FOD inspection is carried out prior to flight. Moreover, baggage loading takes place at the front and rear of the jet engine. It means that broken off pieces from luggage become FOD that is laying right in front or rear of the jet engine.
Since aircraft engine generally starts up before pushback, if FOD from baggage handling is laying around the engine, it can ingest it or jet blast it, both of which are a great safety hazard on the ramp.
That is the reason why baggage handling staff must always take care in handling the bags and luggage pieces so as not to create FOD on the ramp. Moreover, after completion of baggage loading or unloading, an FOD inspection of the ramp must be conducted, especially near the aircraft cargo compartments (where baggage loading takes place) to dispose any FOD that is produced during the loading process.
The safety precaution of not wearing loose clothing is of particular importance in baggage handling just like it is in cargo handling. For safety of personnel, baggage handling personnel must not wear loose clothing as a continuously rotating belt can catch it and cause injury.
Aircraft Baggage Loading Accident Case Study
On 6th January 2018, at Jomo Kenyatta International Airport in Kenya, Etihad Airways aircraft Airbus A320-200 was parked at the aircraft stand getting ready for departure to Abu Dhabi airport.
The Belt loader was engaged with the aircraft with its engine running when the baggage handling staff left it as the baggage loading was complete and just a few extra luggage pieces were awaited.
Suddenly, due to some unknown reason, the belt loader started moving and reversed from the aircraft upon which is hit a cargo dolly that changed its direction. The belt loader went straight for the starboard side jet engine of the aircraft and collided with it causing damage to engine cowling.
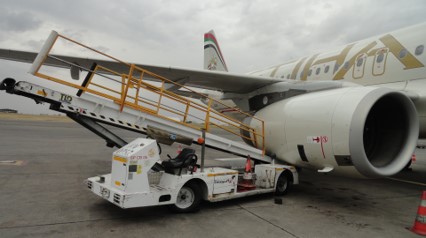
Since the conveyor belt of the belt loader is powered by its engine, the engine is kept on during operation. However, the loader must not be left unattended as it can result in an accident like discussed above. If there is no one to attend the machine, its engine must be turned off. The accident emphasizes the importance of not leaving equipment unattended on the ramp.
With this we conclude today’s post. If you liked this article, share it with at least one person of common interest. It allows our work to be of service to people who can benefit from it the most.
If you are interested in obtaining a base level knowledge about ramp safety, check out this 7-hour video based course on Udemy that you can easily finish in a week (or binge watch in a day or two). It explains ramp safety in detail with interesting case studies of ramp accidents for in-depth understanding of the subject. It also explains ramp safety aspects associated with 13 main ground handling operations carried out on the ramp.