REDA stands for Ramp Error Decision Aid. It is a process or methodology developed by Boeing, the famous aircraft manufacturer, for investigating accidents and incidents that take place on the ramp that are caused by worker performance.
The purpose of REDA is to identify the root cause of error that resulted in the accident or incident, that REDA calls as Event, and allow the organization that is using the REDA investigation process to improve itself such that similar accidents and incidents don’t repeat.
The Ramp Error Decision Aid (REDA) tool is a structured process used to investigate events caused by worker performance
– REDA User Guide by Boeing
Today’s article is dedicated to explaining this methodology.
Changing REDA’s Perspective
Boeing has changed the way it refers to REDA from calling it an error investigation process to calling it an event investigation process because error always points at some mistake on the worker’s end while there can be another possibility that is not covered under error.
It is what REDA refers to as violation of a procedure or policy. Violation is different from error because violation carries an element of knowledge and intention i.e., someone did not follow the applicable procedure despite having knowledge that the procedure existed.
Although on the face of it, it appears as if REDA is a tool for apportioning blame to ramp workers for the unwanted events caused by their error or their violation, REDA must not be taken as a tool for blaming people for accidents.
In fact, Boeing itself states in its REDA user guide that an estimated 80-90% of the contributing factors to errors and violations are under the control of the management while only 10-20% are under the control of ramp worker.
The above factor is important to remember to set the perspective right before we begin studying how REDA works. REDA is not a process aimed for apportioning blame.
Ramp Error Decision Aid (REDA) is an investigative process designed to identify genuine shortcomings in policies and procedures that, once improved, reduce chances of similar accident again.
We estimate that 80%-90% of the contributing factors to errors/violations are under management control, while the remaining 10%–20% are under the control of the ramp worker.
– REDA User Guide by Boeing
Execution of REDA – The REDA Results Form
To make it simple, REDA investigation process is guided by a 6-page form known as REDA Results Form. This form is what serves as a guiding roadmap for investigators of an organization to conduct the REDA investigation process.
In simplest terms, the investigator has to:
- analyze the event;
- interview the ramp workers involved in an accident; and
- use the REDA results form as a guide to structure the interview and record information.
Ultimately, the information referred above is used for determining the root cause of the problem and fix it by revising a procedure, policy or any other action needed.
In this article, we will explain the REDA investigation process by using REDA results form as our guide and look at how different sections of the REDA results form allow you to undertake a coherent and effective investigation to identify all the causes and all the contributing factors behind an unwanted event.
Basic Terminologies in REDA
Before discussing the REDA process, we are going to look at some basic terminologies used in REDA process.
Ramp System
We have explained in other articles on our website about the different ground handling operations that take place on the ramp including specialized Ground Support Equipment (GSE). From aircraft marshalling to aircraft pushback, there are several operations performed on the aircraft. The Ramp System is simply a term used for entailing the activities, equipment, people and processes related to the ramp.
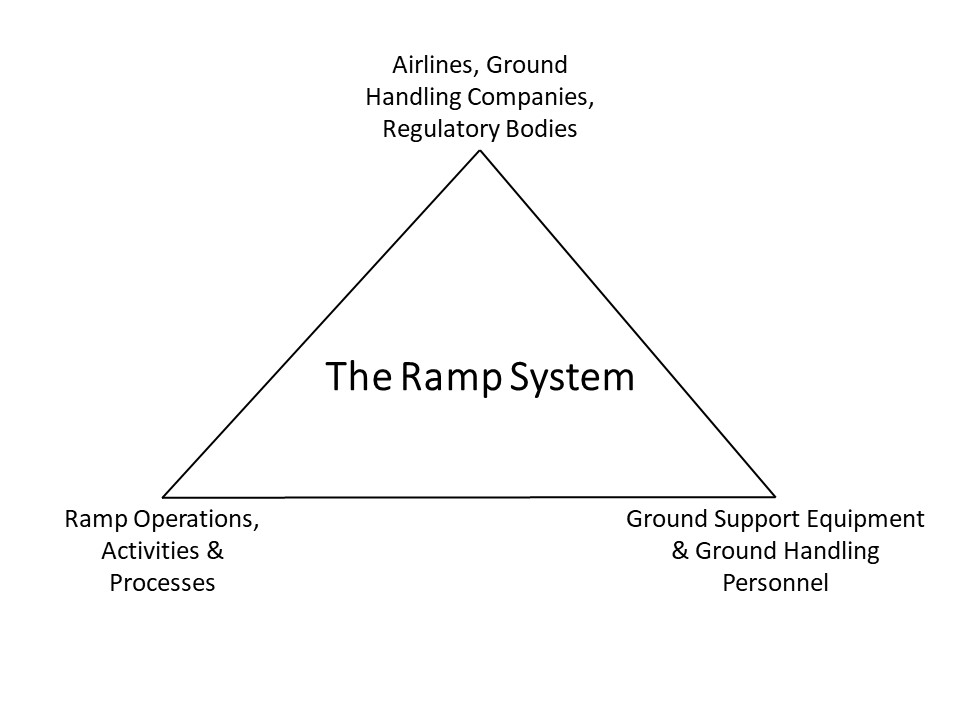
Ramp System Failure
Ramp system failure is said to have taken place when any ramp worker does either of the following three things:
- Makes an error
- Makes a violation
- Is unable to complete task in required time.
REDA has defined each of the above three points.
REDA defines error as under:
An error is a human action (or human behavior) that unintentionally deviates from the expected action (or behavior).
– REDA User’s Guide
For example, baggage loaders were loading baggage and just didn’t notice that a zip of a bag or a small wheel broke and fell on apron to become an FOD. This dropping off and leaving un-noticed an FOD is a ramp system failure caused by human error.
On the other hand, REDA defines violation as under:
A violation is a human action (or human behavior) that intentionally deviates from the expected action (or behavior).
– REDA User’s Guide
Violation differs from error only with intention. For example, an air start unit (ASU) operator was supposed to check that no Foreign Object Debris (FOD) is in front of the engine before starting it but he did not conduct any FOD inspection and started the jet engine without it.
This starting of the jet engine without FOD inspection is a ramp system failure caused by violation. If he had conducted FOD inspection but couldn’t spot a FOD that was laying there than it would have been an error. However, since he didn’t perform FOD inspection prior to engine startup despite knowing the procedure, that is why it is a violation.
It is important to understand where is the Ramp System Failure in the given scenario?
Please note that it is not the case that after starting the jet engine, the FOD was ingested and that the ingestion is a ramp system failure. It is that starting the jet engine without proper FOD inspection was the ramp system failure irrespective of whether that failure resulted into an accident or not.
The above point is important to remember because the term failure seems as if incident has taken place. However, a ramp system failure can easily take place without resulting into an accident. When it results into an undesirable accident, it is called an Event which we will discuss shortly.
Finally, the inability to complete task in required time refers to a situation where neither the ramp worker has made any error nor any violation, but still his work isn’t finished in required time.
For this third condition to be called a ramp system failure, there must not be any error or violation involved, otherwise the time pressure would simply become a contributing factor to ramp system failure and not a system failure in itself.
A good example of this third factor is a catering truck arriving late from the flight kitchen. Now the catering crew would get their job done without any error or delay but still their task wouldn’t complete in required time.
However, this inability is not associated with any error or violation of procedure on part of the catering crew. It is just that the truck arrived late from flight kitchen because the meals weren’t ready in the kitchen on time. Now this is a factor falling outside of the ramp system.
Step 01: Ascertaining the REDA Event Category
Now as we discussed above, a ramp system failure may or may not result into an undesirable occurrence. When it does turn into a such an occurrence, an event is said to have taken place.
It is this event that REDA is designed to investigate. Event is any accident or incident or simply, an undesirable occurrence that is not supposed to take place on the ramp.
The REDA results form we referred earlier (that will serve as the guiding roadmap for understanding REDA) starts with the event at its first page. After filling out the generic information about the event, the very first thing it asks is what undesirable thing has happened on the ramp?
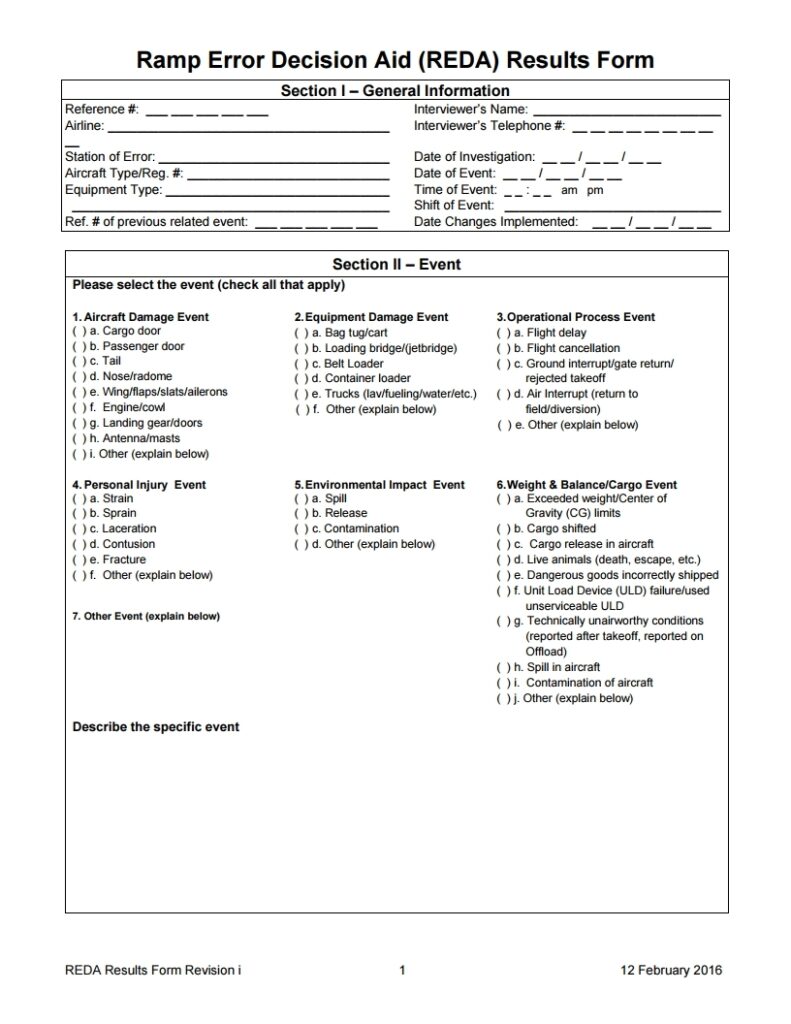
The first step in the REDA investigation process is to categorize the event being investigated. The REDA results form gives various options to choose from to help the investigator. These categories and options have been listed based on Boeing’s experience of the ramp accidents and incidents. You are most likely to find the accident you are investigating among these options.
For example, a jet bridge collided with the aircraft. This is an event because such collisions are not supposed to happen on the ramp. This event falls under both aircraft damage event as well as equipment damage event because both the aircraft and jet bridge would get damaged from such an event.
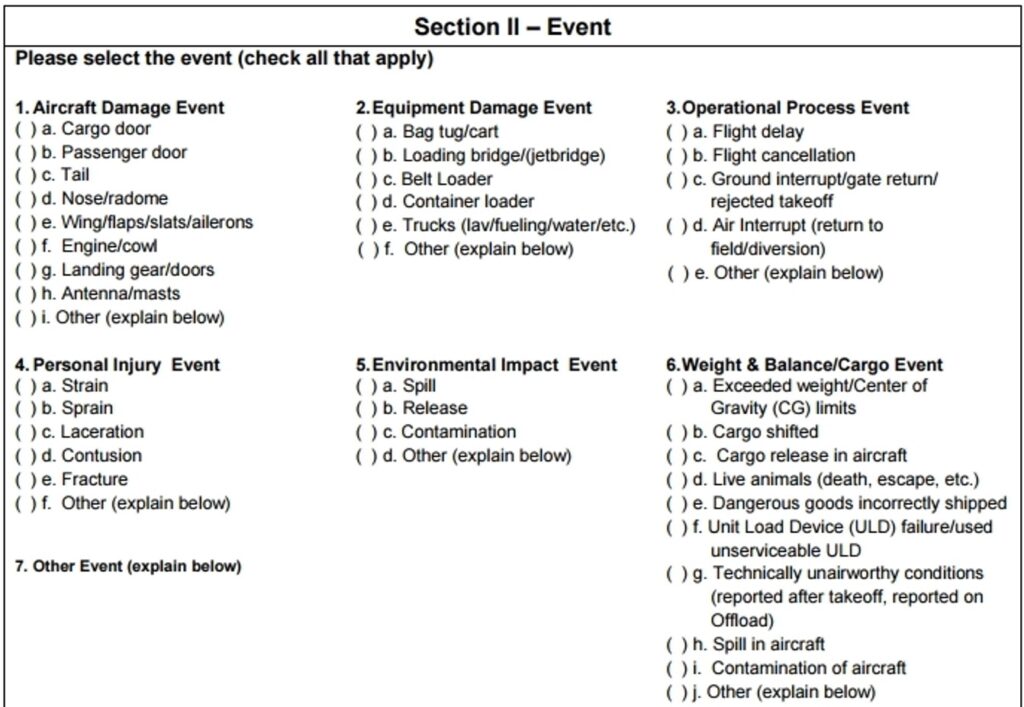
You can observe that a flight delay is also termed as an event (under operational process event category) and falls under REDA because flight delays are not supposed to happen on the ramp. They are undesirable ramp occurrences.
If let’s say a jet fuel spill has taken place, it is an environmental impact event, and if incorrect cargo loading has taken place, it has its own event category termed as Weight and Balance/Cargo Event.
Maybe a chemical consignment leaked during cargo loading and caused a spill inside cargo compartment. It falls under spill in aircraft under the same Weight and Balance/Cargo Event category.
Or maybe an exotic snake specie was being handled in cargo that escaped during loading and caused a lot of drama. It falls under live animals (death, escape etc.) under the same Weight and Balance/Cargo Event category.
If you do not find the event you are investigating, you can write it down yourself.
In the end, you have to record the description of event being investigated. For example, if a jet bridge collided with the aircraft, you would explain in detail the particulars of the event. Even a near miss of the jet bridge from any part of the aircraft is a REDA event.
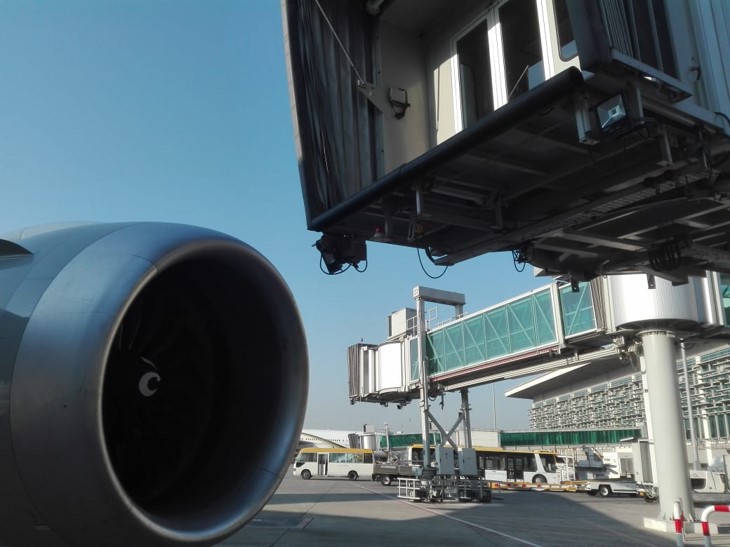
The Relationship Between Event & Ramp System Failure
The REDA philosophy relates the Event to Ramp System Failure. This relation can be of two types:
- Cause-in-fact Relationship: The event was caused because of the ramp system failure.
- Probabilistic Relationship: The ramp system failure did not cause the event directly but it increased the chances of the event.
For example, a potable water truck operator forgot to disconnect the hose from the aircraft’s potable water access panel and drove the truck that caused damage to the hose as well as aircraft’s access panel. This is a cause-in-fact relationship because whenever you would not disconnect the hose and drive the truck, abnormal forces will always cause some sort of damage.
However, take another example. A ramp worker was not wearing reflective vest at night and got hit by a belt loader because the belt loader driver was not able to see him under low light. Now this is not a cause-in-fact relationship because not wearing reflective vest doesn’t always result in some vehicle hitting you on the ramp.
However, reflective vest allows drivers to see if a person is in their way and not wearing reflective vest increases probability of the accident. Therefore, it is a probabilistic relationship between event and ramp system failure. In reality, most accidents take place due to the probabilistic relationships between events and ramp system failures.
Moreover, if it is a cause-in-fact relationship, there is going to be a single Ramp System Failure to cause the event. However, if it is a probabilistic relationship, there can be multiple Ramp System Failures where each failure increased the probability of event.
It is important to reconcile the types of ramp system failure with the relationships. Since a ramp system failure can be an error, a violation or inability to complete task in required time, therefore there are many different possibilities that can result into an unwanted event such as:
- An error that causes an event vs. that increases probability of an event.
- A violation that inevitably causes an unwanted event or just increases its probability.
These relationships are important for an investigator to understand because REDA is not just about filling a form. The spirit of REDA process is in understanding the ultimate true root cause of an undesired event.
If you as an investigator don’t differentiate between if Ramp System Failure had caused the unwanted event or had increased the probability of the event then you are likely to pin the blame on an incorrect reason.
Step 02: Ascertaining Ramp System Failure
The next section in the REDA Results Form is all about recording the Ramp System Failure.
Just like REDA events were categorized, REDA results form has categorized Ramp System Failures to make it easy for the investigators to already have a list of options to select from.
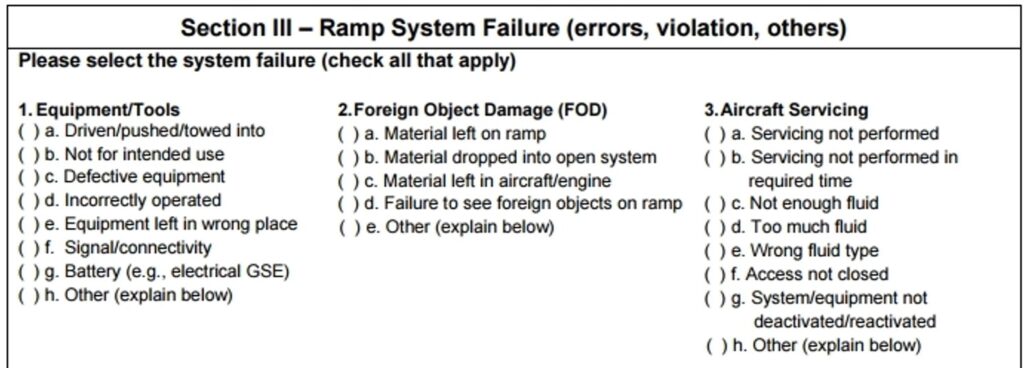
For example, the first category is ramp system failures related to equipment and tools used on the ramp. Here you can see that an equipment or tool may be driven into another equipment, or under worst case scenario, into the aircraft.
The second category is based on Foreign Object Debris (FOD). Maybe the ground crew did not perform FOD inspection on the ramp on arrival of the aircraft that led to the event of aircraft tire getting damaged.
The third category is about aircraft servicing. Maybe the cabin cleaning crew did not perform cabin cleaning altogether when the aircraft was parked on the ramp. Or maybe they came late and therefore cabin cleaning was not performed within turnround time of the flight that caused delay.
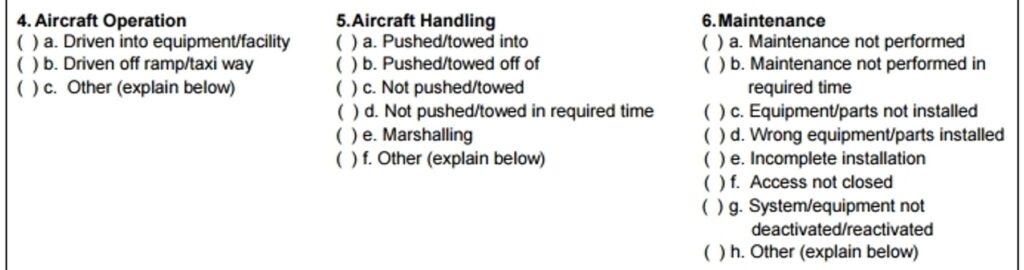
The fourth category is based on ramp system failures of aircraft operation itself. For example, the aircraft did not stop at its designated stop position and kept moving forward that resulted in collision of its wing with the jet bridge.
The fifth category is based on Aircraft Handling i.e., ramp system failures of guiding or moving the aircraft from an external source such as when the pushback tractor is pushing or towing the aircraft. Or when the marshaller is guiding the pilot to dock the aircraft.
The sixth category is based on Maintenance that would generally include such activities that are performed by the airline’s engineering team on the aircraft.
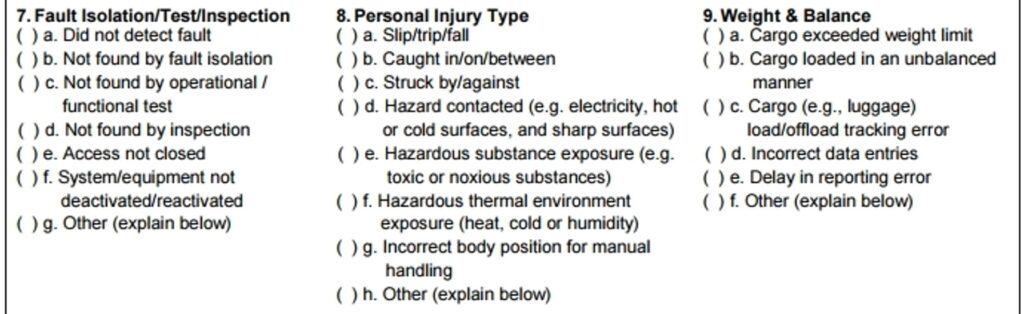
The seventh category is titled Fault Isolation, test or inspection that refers to technical inspections of the aircraft. For example, the walk around check of the aircraft failed to detect that the cargo compartment was not properly closed or that a piece of fabric was stuck in cargo compartment door.
The eighth category is based on personal injury that is relatively simple to understand and the last category is of aircraft weight and balance that primarily deals with the cargo loading crew. For example, maybe the crew miscalculated the total weight of cargo loaded in the aircraft.
The REDA investigator is most likely to find the ramp system failure in this form, however, if he doesn’t, he can write down his own.
It is important to mention here that there can be and would most likely be multiple ramp system failures linked to an event. In this multiple selection, the investigator must remain well oriented that he has to link the ramp system failures with the event.
For example, a belt loader collided with the aircraft engine cowl due to being incorrectly operated. Further, the investigative interview revealed that one of its safety systems was also unserviceable.
Therefore, when you are investigating an incident or occurrence, you are likely to make multiple selections and it is important to keep things linked on the form. More importantly, use the form as a tool for the mind to avoid making REDA a form filling process. It is the mind of the investigator that will find the root cause and not the REDA form.
It is also important that with every Ramp System Failure that you identify as an investigator, always ask yourself,
Is this Ramp System Failure an error?
Or is it a violation?
Or is it the inability of the ramp worker to complete work in required time?
Say for example you are investigating an accident in which an aircraft engine cowl collided with a cargo dolly when the aircraft was parking at the aircraft stand. When you checked the CCTV footage, you found that the cargo dolly was left at the wrong place by ramp workers who serviced the previous flight on the same stand.
Now you have to ask that why did they leave it in the wrong place? Is it an error? Maybe they left it there by mistake not knowing that cargo dollies have a dedicated space for standby.
Or is it a violation? Maybe the ramp worker knew the procedure that he has to remove the cargo dolly from the aircraft stand but he thought it is not a big deal and that the next flight will also need cargo dollies so what’s the harm in leaving it there. Now this is not an error but a violation.
The above facts will come to light only when you will interview the ramp worker not in an intimidating manner but in a warm and forthcoming manner.
Don’t give them the impression that you are trying to pin a fault on them and blame them as they already will have their guard up when they hear that you are an investigator.
The REDA Contributory Factors
At this stage, it is important to explain contributory factors in REDA because the next step in REDA investigation after ascertaining ramp system failure is to find contributory factors to the event.
In the context of the REDA process, a contributing factor is any element that negatively effects the proper functioning of Ramp System and by way of that negative effect, contributes towards either causing a ramp system failure or an unwanted event, or increasing their chances of happening.
For example, jet engine startup procedure blew away a unit load device by jet blast. Now this blowing away of the Unit Load Device (ULD) by jet blast is an unwanted event and you are investigating it. You found that the ramp system failure was that the ULD was laying in the jet blast danger zone when the jet engine was started.
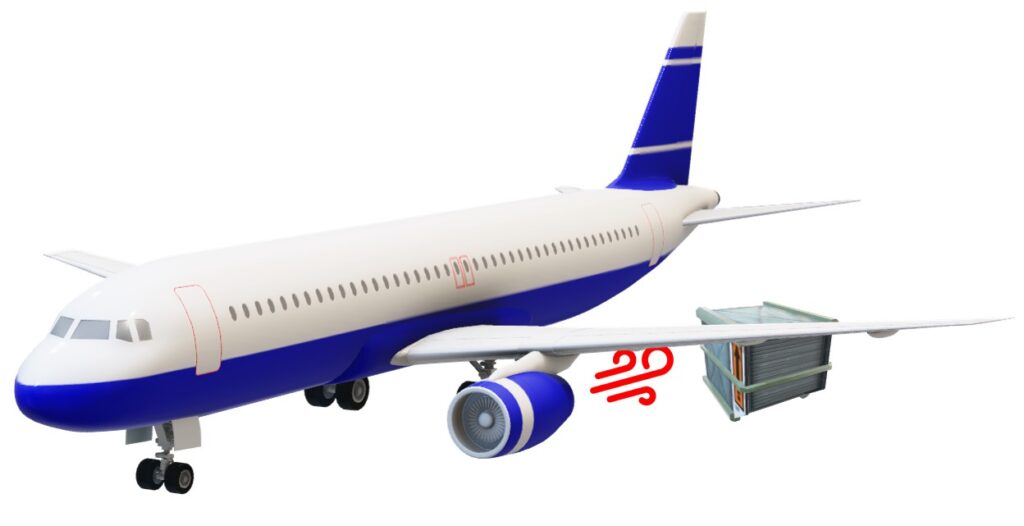
You further investigated whether the ramp system failure was an error or a violation. You found that ramp worker of the last flight did not remove the ULD from the jet blast danger zone because he forgot to do so. Contributing factors unveil themselves when you ask another WHY?
Why did he forget to remove the ULD? Because he was under time pressure to finish his work.
Why was he under time pressure? Because he was assigned an additional duty of helping with another ramp task.
Why was he assigned additional duty? Because on that day, one ramp worker in the team was absent and the ground crew was running the show with one man short.
Why was the show being run with one man short? What remedy has the company got for meeting unexpected absentees? You find that company has not hired leave reserves to meet with unexpected staff absentees because hiring additional manpower puts additional burden on company’s finances.
All of the above answers are a contributing factor to the event in which the final is on the level of management i.e., hiring additional manpower as leave reserve personnel. In this way, a contributing factor does not directly cause or becomes a source of an unwanted event but contributes towards its happening.
The REDA guide by Boeing itself says that the ramp worker involved in the accident is the best person to learn about contributing factors. He is the best person to tell you what improvements are needed to make sure such factors are eliminated or reduced to prevent future accidents.
However, it is the investigator’s skill to obtain that information from the ramp worker. REDA investigator needs to have a well developed interviewing skill in which you are able to communicate in a way as to assure the ramp worker that you are not trying to make a case against him.
You have got to communicate in a way as to express that you are making the ramp worker involved in the accident a part of continuous improvement process. You have to be cautious not to threaten him with your questions as he would already be on his guard trying to save himself from a blame.
The REDA Event Model & The REDA Philosophy
At this stage, it wouldn’t be hard to understand what is called the REDA Event Model. It simply explains this concept to the investigator that whenever an event takes place, it takes place in a probabilistic field. There are one or more ramp system failures behind the event, each having multiple contributing factors around it.
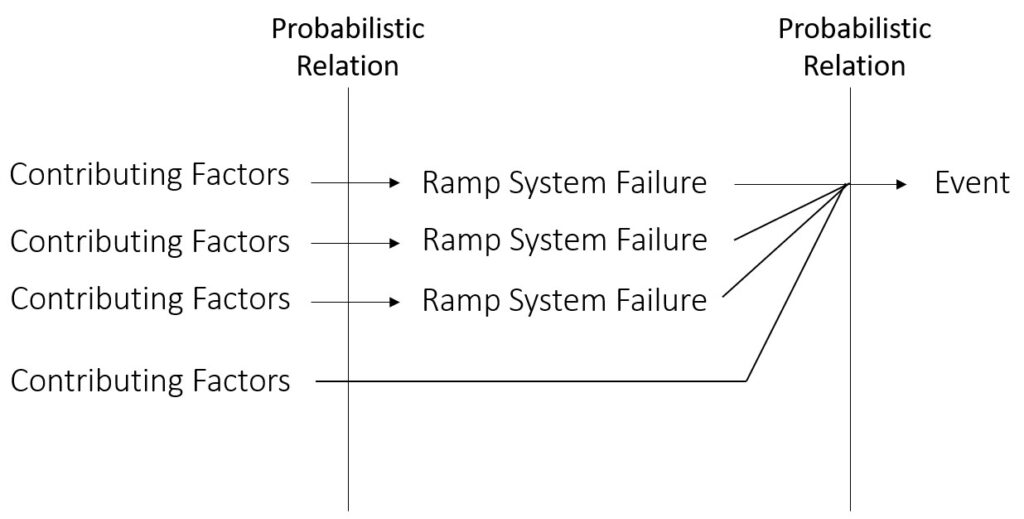
Some contributing factors can be directly contributing to increasing chances of an unwanted event itself instead of just a ramp system failure. What is important for an investigator to understand is the realm of possibilities that define the nature and philosophy of ramp accidents.
Understanding of REDA philosophy will allow an investigator to undertake the process of finding the truth in a complete and wholesome manner. REDA stands for Ramp Error Decision Aid and later Boeing changed its name to Ramp Event Decision Aid to remove the emphasis from error and put emphasis on event.
The REDA philosophy is based on the understanding that investigation of an unwanted event must not be for the purpose of just finding where the ramp worker made the error and then pinning the accident on the worker to close the investigation.
The whole point of making a REDA event model is to find the reasons behind the error or violation the ramp worker made to remove the spotlight from the worker and scrutinize the policies, procedures and processes in place. The REDA investigation process begins with the understanding that ramp worker did not want the accident to happen.
REDA maintains that it is the shortcomings in processes, policies and procedures that need to be identified and removed to prevent similar accidents from happening again.
Step 03: Ascertaining the Contributing Factors of the Event
After ascertaining the ramp system failure, the next step in the REDA investigation process is finding the factors contributory to the undesirable event.
Contributing factor checklist starts with one of the most important elements of ramp safety i.e., documentation.

While it is very important to realize that creating rules, policies and procedures is critical for ramp safety or any other operation, it is equally important that these rules policies and procedures don’t have shortcomings that make them ineffective and thus a contributing factor to undesirable events.
The rules, policies, procedures and forms must be understandable. Quite often, these documents are too complex for an average ramp worker to understand. Such difficult terminologies such as use of legal vocabulary must be avoided and documents must be made with this in mind that they have to make sense for a person who may not be highly qualified from an academic perspective.
Unavailability of such documents for ramp workers is another contributing factor. There may be a rule, but it is kept in the operations manager office. The duty shift in-charge of ramp worker’s teams and the control rooms of ramp staff is not given a copy so they may consult it whenever needed. It is another contributing factor towards accident.
Sometimes the documents are incorrect in the sense that they may not be guiding the worker correctly. For example, maintenance checklist may contain a check for correct functioning of a component that has been replaced with an upgraded version.
Too much information and conflicting information is also a problem. A Standard Operating Procedure (SOP) may be defining how to operate the a certain Ground Support Equipment (GSE) at more than one places, each time with a different angle and that can create confusion. These documents must be concise.
Many times, the information is insufficient. For example, the procedure for baggage handling on the ramp may be written too generic without explaining each part of the flow of work. It can become a contributing factor to an unwanted event because it gives way for confusion due to absence of information.
A critical factor for such documents is how long do they take to update?
If the process of approvals of a new form to be used in field is too complicated or that the reviewing process takes several months, it can be a contributing factor. For example, an airport has started using tow bar less tractors, however, safety precautions for them haven’t been updated in relevant procedure.
Or maybe when certain information was taken from manufacturer’s manuals to be incorporated into a procedure, some mistakes were made. Such a discrepancy can become a contributing factor to undesirable events.
Maybe worker had all the information, but he still undertook the task incorrectly You’ll have to interview the worker why he did it if this is the case. Maybe he thought it’s not a big deal. In that case, it is better to include some clarification inside the document to help workers realize its importance.
The procedure defined may be inefficient. For example, you have given ramp workers two forms to record cargo loading and both the forms have overlapping information. So, all the information that could have been recorded in one form is now divided in two forms and the worker may get too busy with paper work to focus on the cargo loading safety itself. It can be a contributing factor.
Last but not the least, Uncontrolled documents are also a contributing factor to unwanted events. By uncontrolled, it is meant that let’s say a procedural document was distributed in two control rooms but when its revision was issued, new copies were not replaced after retrieving old copies.
Control of documents is a mechanism in which a proper record of distribution and updating is kept so that any change in the document is communicated to all. Such a shortcoming can become a contributing factor because it may compromise transfer of some important safety precaution recently revised in a procedure while the ramp team keeps using the old procedure.
The second category of contributing factor has already been discussed in different perspectives before. It is related to equipment.
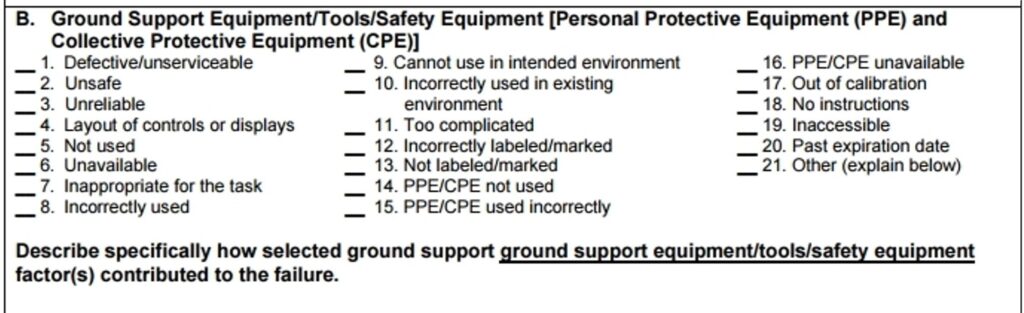
For example, the safety shoe sensor of catering truck wasn’t working properly that contributed to an unwanted event where aircraft door came into contact with the catering truck floor. Maybe the extendable railing of the cargo loader was missing that contributed to a person falling from height.
Maybe the controls of the new variant of jet bridge were quite different from the old one due to which the operator got confused and drove the bridge into the aircraft. Maybe the fuel gauge of the refuel equipment was not calibrated that resulted in over fueling and ultimately a fuel spill on the ramp.
The third category of contributory factors critically looks at the design of the aircraft to see if the design of the aircraft itself had some shortcomings that contributed towards an accident.
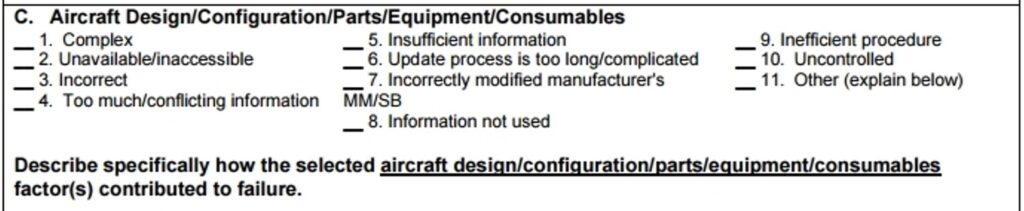
For example, maybe the airconditioning access panel had a faded out label on it that caused confusion for the ramp worker and contributed towards an accident. However, since majority of airlines use Boeing and Airbus aircrafts for commercial flights, it is generally rare that a fault with let’s say user friendliness is found to be a contributing factor as ramp workers are usually familiar with these aircrafts.
The fourth category of contributing factors is important to understand. Job design is often a neglected part of ramp operations that becomes a contributing factor towards ramp safety.

For example, an air start unit operator has been operating air start unit since five years. That’s wrong. There isn’t much to air start unit operation to do it for five years. Ramp managers must rotate people to avoid monotony of work as it tires people out mentally and contributes towards an unwanted event.
On the other extreme, a job change without prior preparation and orientation can also become a contributing factor. For example, the same air start unit operator deputed for operation of preconditioned air unit without familiarization with its controls and operating procedures.
A physically demanding job has lots of chances to become a contributing factor to events. For example, the job of baggage loading where workers have to manually load the bags from the cart on to the belt. They may not notice that the conveyor belt has caught their shirt.
Preconditioned air (PCA) receptacle on some aircrafts is so low that it requires squatting and ducking into position to engage the PCA hose. Any person with some problem in his knees may injure himself while doing so.
In short, there can be many elements of the job or task in itself that may contribute to an unwanted event.
Next category of contributing factors is knowledge and skills. It is also a category that is a common contributing factor to accidents and incidents.

While everyone understands the importance of technical skills and task knowledge; what is important is to also understand the importance of overall process knowledge.
Ramp workers must be trained and oriented not on just their jobs but also how their job fits in between a sequence of many preceding and succeeding ramp operations and how his job is interlinked with others.
For example, catering crew must understand the importance of removing their truck before the air start procedure begins in the same way that the air start crew must know the criticality of catering truck that operates close to aircraft engine.
Individual factors also form a common source of contributing factors towards accident and incidents. Jet bridge operator may be feeling fatigued in his night shift and therefore wasn’t that alert contributing to accident involving collision between bridge and aircraft.
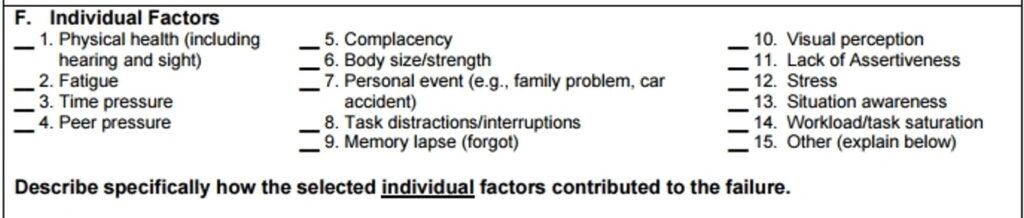
Lack of assertiveness is an important one. Often, a person knows that he is doing the right thing but just because someone else says NO with a lot of confidence, he stops. That becomes a contributing factor towards ramp accidents.
Catering truck marshaller may be telling the driver that truck is slightly off but the driver might say with confidence that “I’ve got it” when actually the situation is dangerous. At this stage, marshaller has to assert himself and intervene to prevent the accident. In this way, lack of assertiveness in a lot of operations becomes a contributing factor towards accidents.
Elements involving the environment, facilities or the ramp itself also become contributing factors to a lot of accidents. For example, rain can cause pushback tractor to loose traction and cause a pushback related incident. Strong winds may topple the catering truck.

Faded ground markings may also become a source of confusion for ramp workers. Lighting conditions at night may not be good enough to reveal that an access panel is not properly closed. In this way, many elements related to the environment of the ramp may contribute towards an incident.
Next category of contributing factors is extremely impactful and important. It is the organizational factors. Remember when we discussed how 80% of the factors are in the control of organization and management and not the ramp worker? This category is a reflection of that fact.
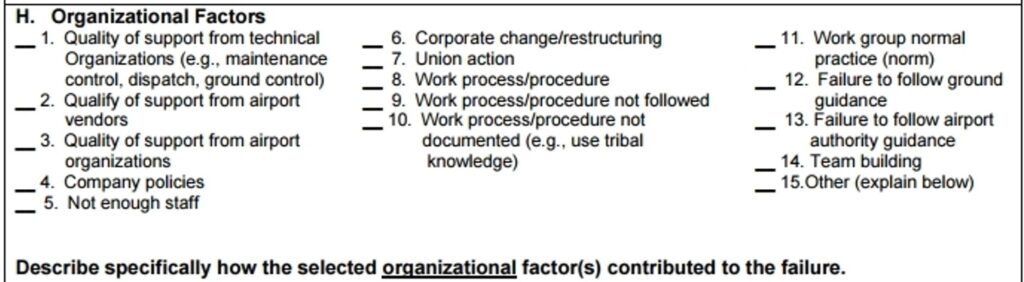
The level of integration and flow of information between different agencies involved directly or indirectly in ramp operation may be lacking. For example, unserviceable radio sets on ground support vehicles may not be rectified by the electronics department at the airport. It would in turn hinder the drivers from listening to tower frequency and may contribute to any accident.
Corporate change and restructuring of the organization may be producing a lot of confusion among workers that can contribute to any accident. Maybe the agency hasn’t developed a policy on when to use conventional pushback tractors and when to use towbarless tractors.
It is these things under management control that can become a contributing factor to many accidents.
Finally Leadership, Supervision and communication are the last two categories of contributing factors each of which is self explanatory in its importance.
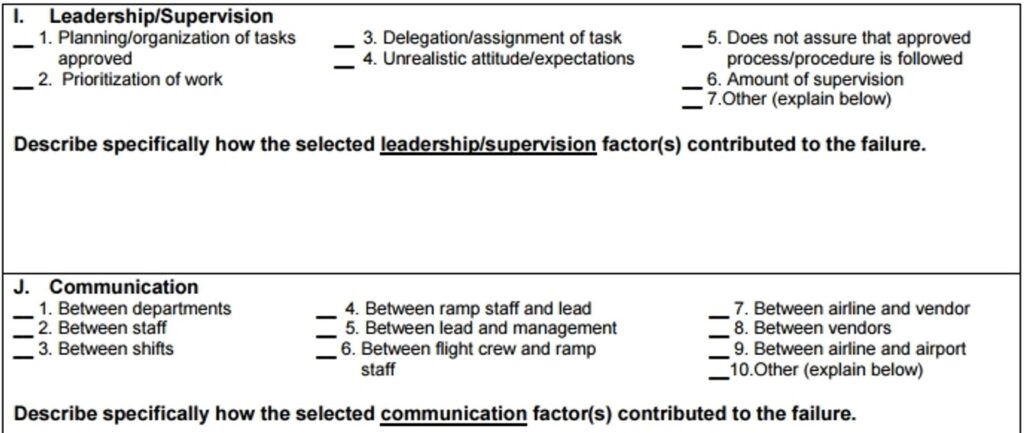
Step 04: Devising Failure Prevention Strategies
The last Section of REDA results form focuses on the existing procedures and policies to allow the investigator to work out failure prevention strategy. The focus here is on Prevention.
That is why it starts with the question that what current existing procedures, processes and/or policies in your organization are intended to prevent the accident but didn’t?
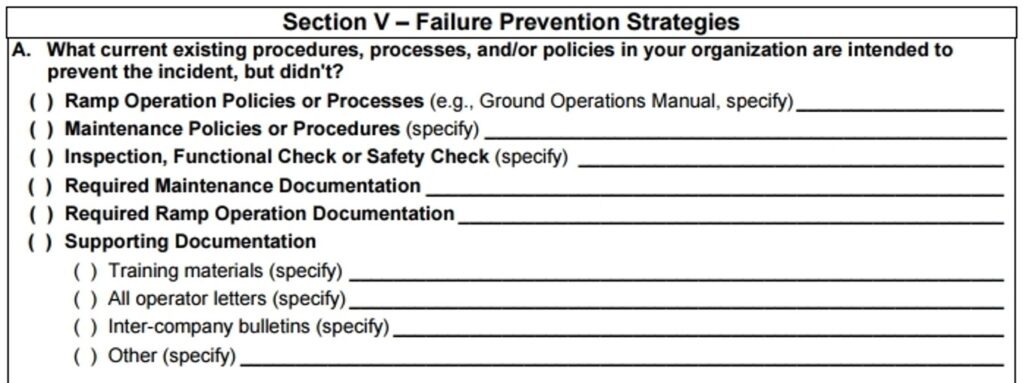
This question tries to find the shortcoming in the existing procedure or policies if they existed; or if absence of a documented procedure or policy is a contributor to an unwanted event, then that will also be revealed here.
In every organization, there is a complete hierarchy of documents in place to define policies and work procedures. The form itself lays it all out in front of the investigator. For example, if a passenger boarding bridge auto-leveler malfunctioned and aircraft door collided with the bridge floor, what does the Ground Operations Manual say about it?
Ground Operations Manual, simply referred to as GOM, is a hefty document of several hundred pages and every airline and ground handling company has its own GOM. It has dedicated chapters inside of it that discuss the procedures and safety precautions for different ground operation services. The investigator has to ask, what does the chapter of Passenger Boarding Bridge say about auto-leveling?
Does it say that the jet bridge operator must stay in the bridge after its engagement to verify normal functioning of the auto-leveling system? Does it say that jet bridge operator must remain in the vicinity of the bridge to intervene in case the auto-leveling system malfunctions?
In this way, the investigator will ascertain whether GOM has sufficient information or not about the issue. If it does not have sufficient information, then revision of GOM will be recommended as a failure prevention strategy.
If it is present in GOM, the REDA investigator may ask what is the policy in place for training the bridge operators? What is the training curriculum? How frequently is training imparted? And so the investigator will keep digging until a procedural or policy recommendation is revealed to prevent such a failure in future.
Now let’s assume that the accident happened not because of some operational and procedural lapse but because of some technical problem in the auto-leveler sensor. Now the relevant place to look would be the maintenance manuals and maintenance checklists.
When was maintenance last carried out on the jet bridge on which the accident happened?
What is the maintenance schedule?
Does maintenance checklist include checking the normal functioning of auto-leveling system?
If not, what is the policy in place for making improvements in maintenance checklists? Are they periodically revised by taking input from experience of maintenance engineers and technicians?
If there is none, then the investigator will recommend revision of maintenance checklist as a failure prevention strategy.
In this way, the investigator will probe into the problem further and further to find the areas of improvement in policies and procedures. He will not pin the accident on a maintenance technician whose signature is present on the last carried out maintenance checklist.
REDA goes as far as looing at the organizational culture. The investigator can ask if similar auto-leveling accident has taken place at some other airport where the same company serves and if the lessons learned have been shared with the help of Inter-Company Bulletins?
Now if you look at what we have just discussed, you can easily see the reflection of the REDA philosophy in this Section-5 of the REDA results form. REDA forces the investigator to look beyond the error made by a person and sheds light on things that are under the control of higher management i.e. policies and procedures.
The REDA spirit is to embed the lessons learned from an accident into policies and procedures so that similar accident is not repeated.
This same section of failure prevention strategies has a subsection for listing down all such recommendations upon which the management may then take action to prevent similar unwanted events from occurring again.
Step 05: Record Chronological Summary of Event
The last section in REDA results form simply records the chronological summary of the unwanted event. However, it is different from when the accident details were recorded in the beginning.
In the beginning, the accident was uninvestigated therefore the details were in the form of different pieces of story noted by the investigator.
However, this time, the summary is being recorded after investigation is complete. The purpose here is to write the story with the facts revealed in the investigation. The story at this stage will reveal how the accident happened as discovered by the REDA investigator.
In this section you record how sequence of events unfolded themselves to finally result in the REDA Event. This summary will record all of the ramp system failures and contributory factors along a timeline explaining the REDA Event in the form of an understandable story.
This summary marks the completion of the REDA investigation process.
If you liked this article, share it with at least one person of common interest. It allows our work to be of service to people who can benefit from it the most.
If you are interested in obtaining a base level knowledge about ramp safety, check out this 7-hour video based course on Udemy that you can easily finish in a week (or binge watch in a day or two). It explains ramp safety in detail with interesting case studies of ramp accidents for in-depth understanding of the subject. It also explains ramp safety aspects associated with 13 main ground handling operations carried out on the ramp.