Aircraft pushback is the last ground handling operation on the ramp after which the ramp is vacated. However, safety in aircraft pushback and towing operations holds critical importance in ramp safety.
On 13th January, 2008 at San Francisco International Airport in the United States, a Boeing 757 of United Airlines was being pushed back from the ramp when its tail collided with the tail of a Bombardier CL-600 that was also recently pushed back from an adjacent aircraft stand. Both aircraft sustained significant damages due to the incident.
The above incident highlights the importance of safety in aircraft pushback operation. This is what today’s article is all about. This article will explain the ramp safety aspects associated with aircraft pushback operation.
Aircraft Pushback Procedure
We have a dedicated article on introducing the aircraft pushback tractor – the equipment used in pushback operation. The humans involved in the pushback operation include:
- Pilots
- Pushback tractor driver
- Headset man
- Two wing walkers, one on each side of the aircraft,
- One tail walker
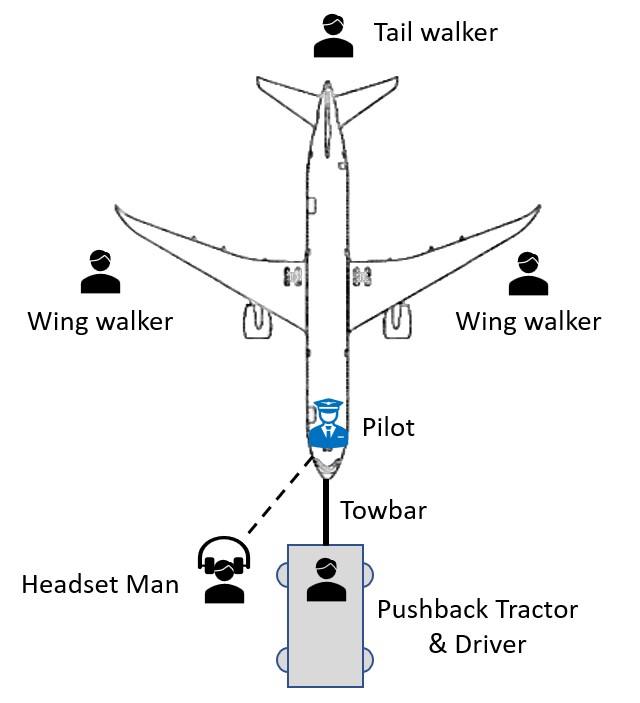
Pilot is the overall in-charge of the operation, however, pilot does not have a clear visual and orientation during pushback operation of how the aircraft will be reversed from the aircraft stand. Moreover, the movement of the aircraft in a pushback operation is not under direct control of the pilot himself.
The speed of the pushback, the angle of the turn and everything related to the pushback movement is under the control of the pushback tractor driver. However, the pushback tractor driver sits inside the pushback tractor and remains occupied with controlling the vehicle and the movement taking place.
In view of above, pilot’s point of communication and the overall in-charge for everything happening on ground is the headset man who remains in constant communication with the pilot through a headset device connected with the cockpit with the help of a cable plugged into a port present in the nose landing gear.
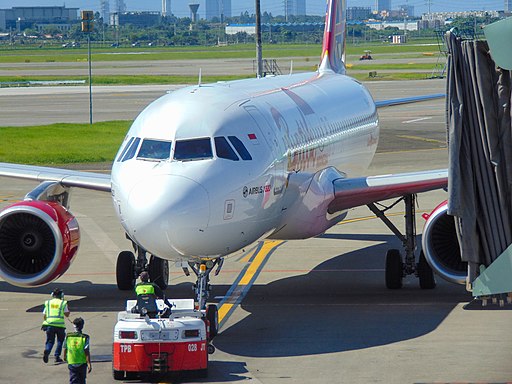
Control tower gives clearance for commencement of the aircraft pushback after which the pilot and the headset man communicate with each other to finalize when to start the pushback. Once the pilot and everyone on the ground are ready, headset man gives go ahead to the pushback tractor driver and the pushback operation begins.
The Aircraft Walkaround Check Before Pushback
Safety in aircraft pushback operation starts from before the operation actually begins. It starts with a walkaround visual check of the aircraft by pushback crew. Its importance starts from ramp safety but extends to flight safety. It is important to conduct a visual inspection of the aircraft by walking around it to make sure that nothing looks abnormal.
For example, cargo doors of the aircraft may not be properly closed or one chock from rear landing gear wheels may not have been removed. It is small details like these that matter a lot in ramp safety and a simple walkaround of a trained person with an eye for detail goes a long way in preventing aircraft pushback accidents.
Once the walkaround check is complete, pushback equipment is setup and pushback crew gets ready for the operation.
Importance of Correct Towbar Engagement in Aircraft Pushback Safety
The towbar is seemingly a simple piece of equipment without any moving part such as a motor or engine, technically called a non-motorized piece of equipment, however, it carries a lot of important points with respect to safe engagement with the aircraft.
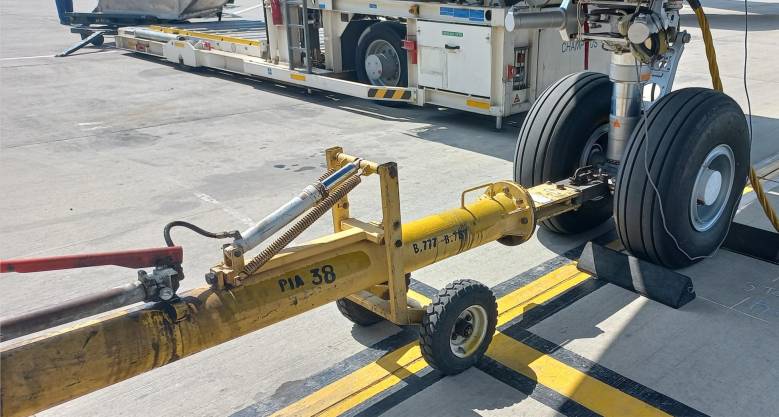
The sequence of steps in setting up pushback tractor and towbar involves an important safety consideration. The towbar is always engaged first with the aircraft. After towbar engagement, pushback tractor is hooked with the towbar.
This sequence is important because to whichever side the towbar is engaged first, the other side will have to be adjusted accordingly. If the towbar is engaged first with the pushback tractor, you cannot move the aircraft to align it with the towbar and make a correct engagement.
Therefore, once the towbar is engaged with the aircraft, it is properly aligned with the line of symmetry of the aircraft. After that, the pushback tractor is brought in and adjusted to make the connection. In this way, the aircraft and the towbar serve as a reference for the pushback tractor to correctly positioning itself instead of the other way around.
Furthermore, the angle of engagement of towbar is also important. There are two main angles to consider:
- The angle that towbar makes with the aircraft’s line of symmetry
- The angle towbar makes with the ground
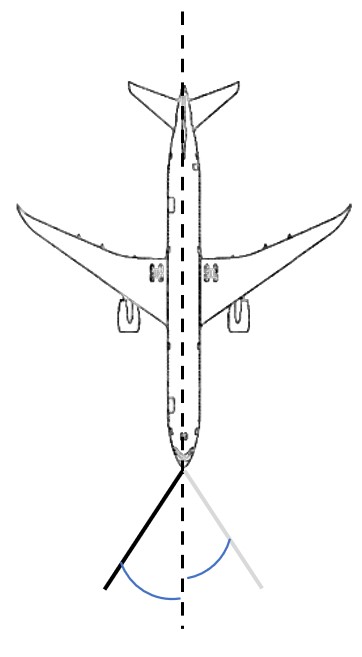
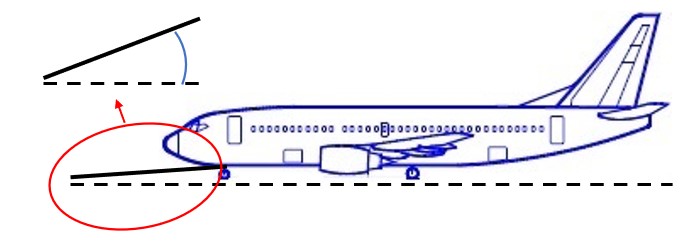
The first angle is what controls the steering of the aircraft during pushback. However, this angle is locked by the design of the aircraft’s towing fitting that does not allow the towbar to swing left or right with respect to the nose landing gear.
However, the second angle is to be taken care of and it must be as much close to zero as possible otherwise it poses risk of towbar snapping under a buckling force.
Timing of Removing Aircraft Wheel Chocks & Releasing Aircraft Brakes
Aircraft chocks must be removed only after towbar and pushback tractor have been successfully engaged with the aircraft and pushback tractor has driver inside of it. It is important because it is the chocks that prevent the aircraft from movement in case its brakes are released from the cockpit.
If the pushback tractor is not properly engaged with the aircraft and chocks are removed, aircraft brakes are the only thing stopping the aircraft from moving. If the pilot releases the brakes mistakenly, there is risk of aircraft rolling uncontrollably and hitting the tractor or running over someone’s foot.
Many accidents of aircrafts running over people are experienced around the world on yearly basis. Such accidents are a result of such co-incidences where chocks have been removed and pilots release aircraft brakes with nothing to prevent the aircraft from rolling forward or backward. Once the pushback tractor is properly setup and the driver is inside the tractor, pilots can release the aircraft parking brakes.
Aircraft has parking brakes in front and rear landing gears. These brakes play the same role as parking brake of your car. They prevent the aircraft from rolling forward or backward under a slope or any external force. Many airport aprons are designed with a slight slope towards a drainage line so that during rain, water does not remain stagnant on apron. The same slope may also allow the aircraft to roll on apron if chocks and parking brakes are not applied.
Before pushback tractor could start pushing, aircraft’s parking brakes must be released otherwise the aircraft pushback tractor will try to push an immovable object. It will cause the towbar and the nose landing gear to bear the tussle between the aircraft and pushback tractor. It will result in either the towbar getting snapped or the nose landing gear collapsing.
Therefore, it is extremely important for ramp safety that aircraft pushback crew and the pilot make sure that the aircraft parking brakes are released before the pushback tractor driver starts to push the aircraft. For this purpose, clarity in communication, especially phraseology, between pilot and pushback crew is of critical importance. Pushback crew and pilot must use very clear phrases to talk to each other about aircraft brakes.
For example, a general phrase from the pilot to the crew could be “Cleared for pushback”. There is lot of ambiguity in that phrase. Maybe the Pilot is just saying that Air Traffic Controller has given clearance for pushback while the pushback crew might mistake it for clearance to begin the pushback action by assuming that pilots has released the brakes.
Instead, it would be much better if the headset man says “Ready for pushback. Please release the parking brakes”. Pilot may reply “Parking brakes released” and the headset man would reply “Starting Pushback”. These phrases convey the status of parking brakes precisely.
Aircraft Pushback Headset Communication – Importance for Safety
The communication between the headset man and the pilot must never break. If there is any disconnection in this communication because of any technical (or any other) reason, the pushback operation is stopped immediately, and headset man continues the operation only after fixing the problem.
If the problem is unable to be fixed and the pushback operation has to be continued without the headset communication, headset man has to bring it into the notice of the pilot so that the pilot and the headset man establish a consensus that the remainder of the operation is to be performed without audible communication.
An additional safety measure incorporated by some airports is that if a pushback is being conducted without two-way headset communication, it also needs to be informed to the control tower so that the controller also knows about the situation and observe additional precaution (such as disallowing parallel pushback on an adjacent aircraft stand).
It is important because pilot must not remain under the impression that headset communication with the ground is up while it is actually down. Cockpit crew must know that now if any communication has to be made with ground crew, it has to be made through hand signals.
Under such a condition (when headset communication fails), only the headset man is authorized to communicate with the pilot through hand signals. Any other pushback crew is not allowed to communicate with the pilot because it creates ambiguity in pushback communication. If any other crew notices anything abnormal, they must convey it to the headset man and not the pilot.
Aircraft Pushback Accident Case Study – Importance of Headset Communication
On 26th June 2007 at Birmingham Airport in England, a British Aerospace Jet was pushed back from the ramp. The headset was unserviceable therefore the pushback crew and the Pilots onboard were communicating with the help of hand signals.
Everything went normal in the pushback until the time when pushback tractor had to be disengaged. At this point, the pushback crew ran into a technical problem. For some reason, the towbar could not be disconnected. Meanwhile, another aircraft needed to pass through the same taxiway.
The pilot in command waited to see if pushback crew could solve the issue. However, the issue was unable to be resolved. Therefore, the pilot decided that the aircraft be towed back to the ramp from where it was pushed back to clear the taxiway it was blocking.
The first officer flashed the aircraft’s taxi lights and waved his hands from inside the cockpit to get the attention of the pushback crew to inform them about the new decision. Eventually, the pilot in command was able to make eye contact with the pushback crew.
Since headset communication was down, pilot relied on conveying the message through hand signals. However, there were no standard hand signals to say “take me back to the same ramp”. Nonetheless, the pilot pointed towards the aircraft waiting at the taxiway. After that he pointed at himself and finally pointed at the ramp from where they had been pushed back.
The pushback crew looked at the hand signals of the pilot and responded with pointing at the ramp. The captain gave them a thumbs up. Without any further due, the pushback crew reversed the pushback tractor to drive the aircraft back to the ramp being pointed at and the aircraft nose landing gear collapsed. It happened because the pilots had not released the aircraft parking brakes yet when the pushback crew commenced the aircraft towing.
The accident was investigated by Air Accidents Investigation Branch of United Kingdom. Investigators attributed the accident to the ambiguity in communication between the Pilot and pushback crew. In the absence of headset communication, the exchanged hand signals between the pilot and the pushback crew did not precisely convey whether or not aircraft parking brakes had been released which resulted in the accident.
Clarity in Communication of Aircraft Pushback Operation with Control Tower
Clarity in communication during aircraft pushback operation is not limited just to pilots and ground crew. It is also of significant importance for control tower.
From control tower’s end, it is recommended that any clearance issued by the controller must never be conditional. For example, air traffic controller should not say that you are cleared for pushback after pushback on the adjacent aircraft stand. This is a conditional clearance and leaves the decision on the pushback crew and pilot.
If such a conditional clearance is issued, pilots and pushback crews must communicate with the tower once again before the actual commencement of pushback operation.
Secondly, it is recommended that the pushback driver also listens to the control tower frequency. Radio sets are available in pushback tractors and pushback drivers should turn it to control tower frequency at the time of pushback operation.
The pushback tractor driver should listen to the instructions issued by control tower as well as responses of the pilot. If he thinks there is any confusion regarding any instruction being issued by the controller or that the controller and pilot are making any error, he should inform the headset man to convey his reservation to the pilot.
There is an important human factor involved here. Since air traffic controllers and pilots are generally of much higher rank than the pushback crew, there is an inherent reluctance in pushback crew to disagree with the pilot or air traffic controller. This reluctance and hesitation should be removed through training and grooming.
In pushback operation, pushback crew is in control of the aircraft and if they think there is any risk to safety, they should not proceed. Pushback crew should be encouraged to challenge the decision of control tower or pilot if they feel that something is being missed or that it is unsafe to proceed pushback under certain conditions.
Importance of Headset Man’s Positioning in Aircraft Pushback Safety
Once clearance is received from air traffic control tower and pushback operation starts, the headset man must never sit inside the pushback tractor during the pushback operation. It is necessary because of two important reasons.
Firstly, if the headset man sits in the vehicle, the pilot won’t be able to have a clear line of sight with him. Since during the pushback operation, headset man and all pushback crew move with the aircraft, headset man must always maintain line of sight with the pilot.
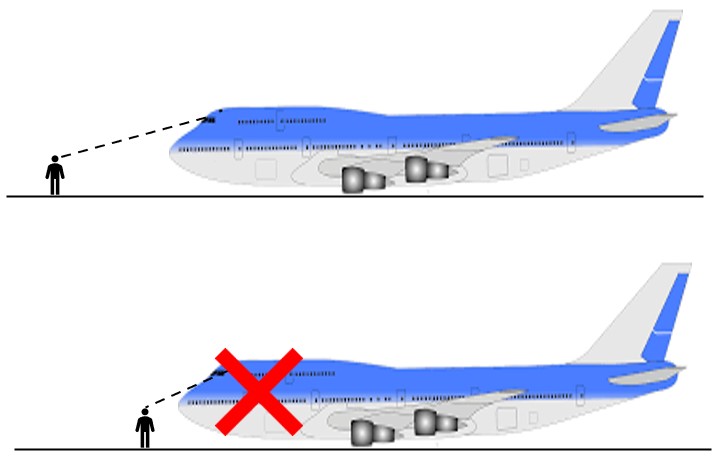
He must be walking at such a distance that he is in eye contact with the pilot. Pilot must not be needing to make any effort in finding where the headset man is. It is necessary to incorporate visual communication during pushback operation instead of only the audible headset communication.
Secondly, if the headset man sits inside the pushback tractor, his sense of orientation of the aircraft on the ramp and chemistry with the rest of the pushback crew including wing walkers and tail walker will be negatively affected.
The Role of Wing Walkers & Tail Walkers in Safety of Aircraft Pushback
The purpose of the wing walkers and tail walker is to keep a check that wings and the tail of the aircraft are clear of any obstacle and that the aircraft is moving without any risk of collision. Wing walkers and tail walker augment the sight of headset man and the pushback tractor driver because they don’t have a good perspective of position of the wing and tail.
The above mentioned perspective is especially important in pushback of wide body aircrafts like a Boeing 777 or Airbus A350 because the wider and longer the aircraft, the less accurate is the sense of distances and clearances perceived by the pushback tractor driver and the headset man. Wing walkers and tail walker communicate with the headset man with the help of hand signals or radio sets.
The accident mentioned at the start of this article (regarding aircraft tails collision during pushback operation at San Francisco Airport in United States) was investigated by National Transportation Safety Board of USA. It found non-usage of wing walkers and tail walker during aircraft pushback operation as contributory to the accident.
How Speed of Pushback is Important for Safety of Pushback Operation
Pushback operation must always be carried out at a slow pace, not more than the walking pace of an average person. The speed with which the headset man walks serves as a reference to the pushback tractor driver to control speed of the pushback operation.
There must not be an instant where the headset man is left behind because the tractor is being driven fast. Headset man walks like he normally does and pushback tractor has to be driven with the same pace. In this way, walking speed of the headset man regulates the speed of the whole operation.
Safety Precautions for Preventing Injury to Aircraft Pushback Crew
There are two important safety precautions to be taken during the pushback operation to prevent risk of injury to pushback crew.
First is that the headset man must walk with the tractor in line of sight of pilot and must not walk with the towbar. It is important because towbar is always under an enormous magnitude of compressive force. This compressive force has the tendency to fracture the towbar in case any defect has developed in its material.
If the towbar fails under a turn, it is likely to swing outwards and hit any person in the way. Therefore, the headset man or any other pushback crew must not walk alongside the towbar between the pushback tractor and aircraft.
Secondly, no person must step across the towbar after pushback has begun due to the obvious risk of stumbling. If the person stumbles or falls down, he can get severely injured from the pushback tractor or the aircraft wheel running over him.
Aircraft Engine Startup During Pushback
Pushback operation begins at the end of all ground handling operations on the ramp. Aircraft jet engines need to be started before the pushback is started; during the pushback operation or at the end of the pushback operation. The reason being when the pushback tractor has finished its job, aircraft becomes ready to move under the thrust produced by its own engines and taxi to the runway for takeoff.
If the engines are turned on after completing the pushback operation and disconnecting the towbar and pushback tractor, there is no risk. However, generally, at least one of the jet engines is started prior to pushback operation and the other jet engine is started during the pushback operation or at the end of it.
This practice (of starting engine prior to pushback) prevents delays in engine startup as once the aircraft has been pushed on the taxiway by the pushback tractor, it becomes an obstruction blocking the taxiway. Therefore, the aircraft needs to get going as soon as possible after completion of pushback operation.
The ramp safety aspect in above case is that when aircraft jet engine is turned on, it produces thrust and tries to push the aircraft forward. When the pushback tractor is pushing an aircraft with its engine running, it is not just working against the weight of the aircraft but also against the thrust produced by the jet engine(s) at idle speed.
This fight between the pushback tractor and the aircraft jet engines puts additional pressure on the towbar, nose landing gear and all components involved. Therefore, every airline and airport has a set of rules for engine startup during pushback to prevent any incident due to engine startup at the wrong time. In case the pushback tractor is towing the aircraft, the engine thrust will work in the same direction of the tractor which has the risk of putting the tractor out of control of the driver.
The risk is aggravated if the pushback operation is being conducted under wet conditions i.e., if the apron is wet with rain or snow because it makes the surface slippery and reduces the traction and grip of pushback tractor on the ground. It increases chances of pushback tractor instability during movement.
Due to these reasons, engine startup before or during a pushback is a sensitive part of pushback operation that must be given due consideration in training of pushback crews and pushback tractor drivers.
Aircraft Pushback Accident Case Study – Engine Startup & Wet Conditions
Let us present the case study of an accident in aircraft pushback operation to highlight the importance of engine startup we explained above.
On 27th September 2017, an Airbus A320 was ready for departure from Dublin Airport in Ireland to Madrid Airport in Spain. The first part of the aircraft pushback operation from the ramp completed without any problem. Subsequently, pushback tractor had to tow the aircraft forward.
During forward towing of the aircraft, pilot requested for permission to start the starboard engine i.e., the engine on right side of pilot. The engine was turned on and the pushback crew towed the aircraft. During the movement, the aircraft nose began overtaking the pushback tractor. This is when things got out of control.
The headset man immediately requested the pilot to cut off the starboard engine because he was observing the starboard engine coming straight at the pushback tractor. The engine was cut off but the pushback tractor jack-knifed into the aircraft jet engine cowl. The blades were still rotating when the pushback tractor collided. Fortunately, nobody was injured in the accident but aircraft engine and pushback tractor sustained damages.
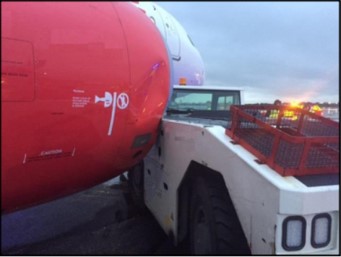
The accident was investigated by Air Accident Investigation Unit Ireland. Investigators found that the probable cause of the accident was shear pin failure that remained unnoticed. The shear pin of the towbar had failed when the aircraft was being towed forward. However, the failure remained unnoticed until the pushback tractor lost directional control of the aircraft which exhibited itself in the form of aircraft nose overtaking the pushback tractor.
The contributory factors to shear pin failure was the engine startup that put additional stress on the towbar. In fact, it was the ground handling company’s standard operating procedure not to turn on the engines during the pushback and towing operation.
Another contributory factor to the accident was wet apron due to rain that caused the pushback tractor to lose its grip and slip once the jet engine thrust applied its force.
The accident conveys a good understanding of the dynamics of the pushback operation and highlights how the engine thrust coupled with wet apron resulted in pushback tractor losing control. It also highlights the importance of good communication. Timely and clear communication made by headset man to cut off the engine saved life of pushback tractor driver.
Sequence in Safely Concluding the Aircraft Pushback
Just like the sequence of releasing parking brakes, removing chocks and connecting towbar and pushback tractor is important at the beginning of the aircraft pushback operation, sequence is equally important at the end.
At the end of the pushback operation, the aircraft parking brakes are applied before the pushback crew disconnects the pushback tractor. This sequence is important for safety because pilots start at least one of the main jet engines towards the end of the pushback operation.
Under a constant thrust produced by the engine trying to move the aircraft forward, if parking brakes are not applied and towbar or pushback tractor is disengaged, the aircraft could instantly move forward (under the thrust produced by the engine) and cause an accident.
Criticality of The Bypass Pin in Safety of Aircraft Pushback Operation
The very last step in the aircraft pushback operation is extremely important. It is about the bypass pin.
The nose landing gear of the aircraft remains under the control of cockpit crew under normal conditions. However, at the start of aircraft pushback operation, a bypass pin is inserted by the pushback crew in the nose landing gear of the aircraft. The bypass pin disables the steering control of the nose landing gear from the cockpit and gives full steering control to the pushback crew.
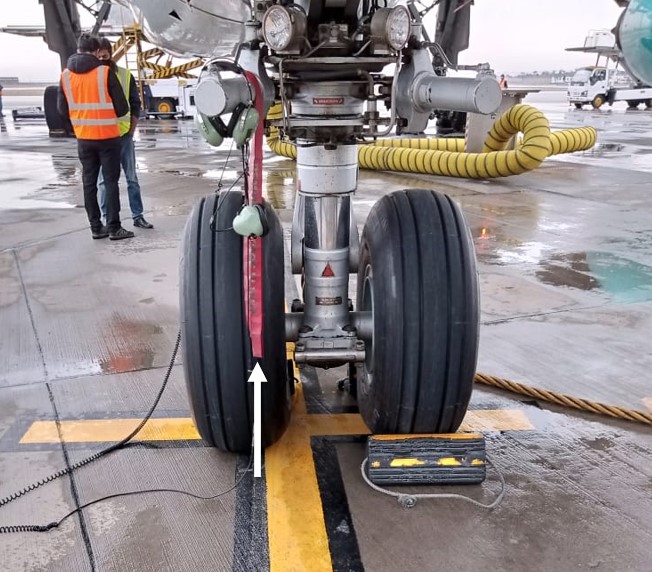
It is necessary to use the bypass pin because during the pushback operation, pushback tractor steers the aircraft during reverse movement through steering the nose landing gear. However, once pushback operation is completed, this steering control needs to be given back to the cockpit.
If the pushback crew forgets to remove the bypass pin, pilots will not be able to maneuver the aircraft on ground from the cockpit that could lead to accident.
A standard safety procedure to prevent such a human error is that after completing pushback operation, pushback crew has to disconnect all equipment, remove the bypass pin and stand a suitable distance away from the aircraft where the cockpit crew is able to see them.
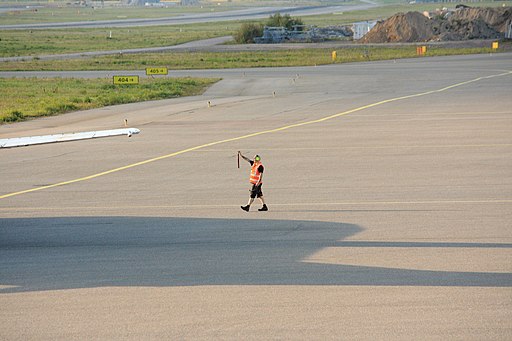
Cockpit crew visually checks that none of the pushback equipment is under their nose. Moreover, the pushback crew also raise their arm with the bypass pin in their hand waving at the pilot. It confirms the cockpit crew that bypass pin has been removed. Only after the cockpit crew has visually confirmed all of the above do they proceed with taxiing for departure.
In this way, the procedure of the pushback operation integrates human factors to enhance ramp safety.
So, this was all about ramp safety in aircraft pushback operation. If you liked this article, share it with at least one person of common interest. It allows our work to be of service.
If you are interested in obtaining a base level knowledge about ramp safety, check out this 7-hour video based course on Udemy that you can easily finish in a week (or binge watch in a day or two). It explains ramp safety in detail with interesting case studies of ramp accidents for in-depth understanding of the subject. It also explains ramp safety aspects associated with 13 main ground handling operations carried out on the ramp.