An aircraft pushback tractor (also known by towing tractor, tug, tug master, airport tractor and many other names) is a powerful vehicle used for towing an aircraft on ground. It is easily identifiable due to its low-profile design and large wheels size. It is used for maneuvering an aircraft between different locations on an airport.
In this post, we will explain what is an aircraft pushback tractor? We will answer why is it called a tractor? Why does an aircraft need a specially built vehicle to move it around? What are its different types? and also look at some recent innovations in pushback tractor technology.
Aircraft Pushback Tractor Purpose
The most common operation for which a pushback tractor is used is an aircraft pushback operation. After an aircraft lands on the runway, it finally reaches an aircraft stand (also called an aircraft bay or airport gate) where it finally stops. This is where the passengers deplane the aircraft.
Airline crew and ground handling agencies perform different servicing tasks on the aircraft at the bay to make it ready for the next operation. We have made a dedicated post to explain the different types of ground handling and support activities that take place at an aircraft stand.
After all servicing activities are finished, aircraft needs to get back on the runway to take off, however, it first needs to reverse itself from the aircraft stand. This is where the pushback tractor comes in.
A towing hook attaches its one end to the aircraft and the other end to the pushback tractor. The driver receives a go ahead signal from Pilot and begins the pushback operation.
It pushes the aircraft back and also steers it so that the aircraft ends up in correct position on the taxiway (a connecting pathway between aircraft stand and runway).
Pilot then gives an okay to disengage signal to the pushback tractor driver at which he unhooks the towing bar and steers the pushback tractor away from the aircraft.
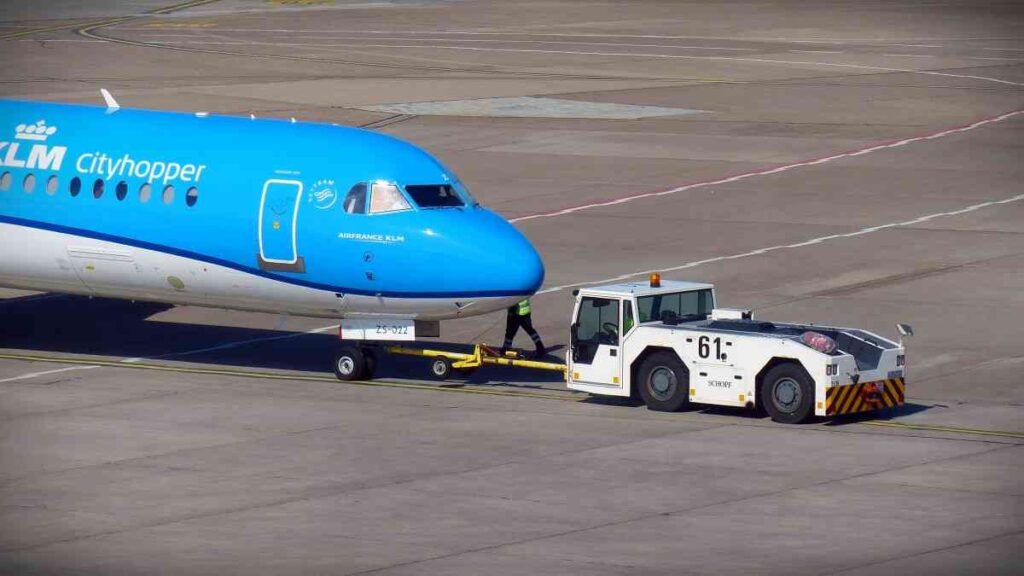
Other Uses of Aircraft Pushback Tractor
Although, pushback from the bay is the most common use of aircraft pushback tractors, it is not the only use. They used for movement of aircrafts in other scenarios as well. Let us discuss these scenarios one by one.
Maintenance Hangar Movement
A maintenance hangar is a large facility where different maintenance activities are performed on an aircraft. These hangars are located on airports and maintained by airline and ground handling staff.
Aircrafts don’t enter and leave the maintenance hangar with their engines on. It is because hangar is an enclosed space and it is not safe for aircrafts to enter and leave this space with jet engines on.
In fact, jet engines are not turned on inside maintenance hangars as an standard operating procedure as there is also a great risk of FOD (foreign object debris) such as a tool getting ingested into the engine.
In view of above, pushback tractor is used to bring an aircraft inside the hangar from anywhere on the airport as well as tow the aircraft outside the hangar after all maintenance work is finished.
And if you haven’t guessed by now, yes, a pushback tractor can also tow or pull an aircraft and not just push it back as the name suggests.
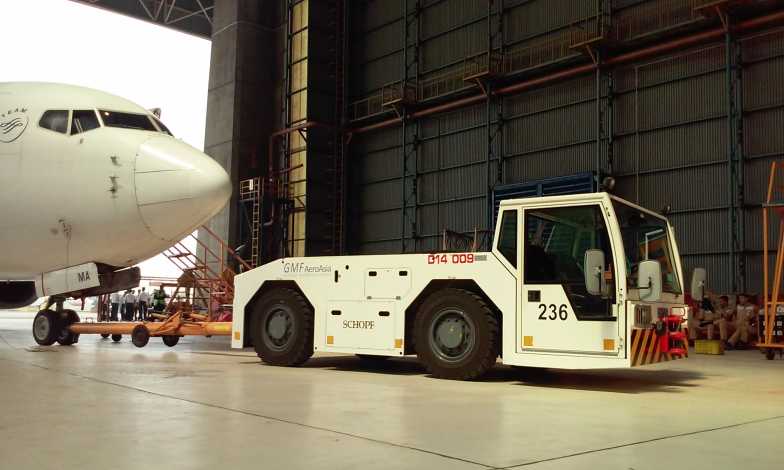
Aircraft Movements Between Parking Bays
Pushback tractor is also used for repositioning the aircraft from one aircraft stand to another at an airport. Such a requirement arises when let’s say an aircraft brings international passengers to an airport gate, however, its departure flight is with domestic passengers.
Since airports have different gates for domestic and international passengers, after passenger deplaning is complete on international gate, the aircraft needs to be pushed back from international gate and taken to a domestic gate. A pushback tractor is used for such a movement because it is not economical to turn on jet engines for such a short movement.
Another example of such movement is when an aircraft brings passengers but there is no departure flight scheduled for the aircraft immediately. Under such a case, such an aircraft is repositioning from the gate at which it first parked to a remote aircraft stand. It frees up the occupied gate for other flights.
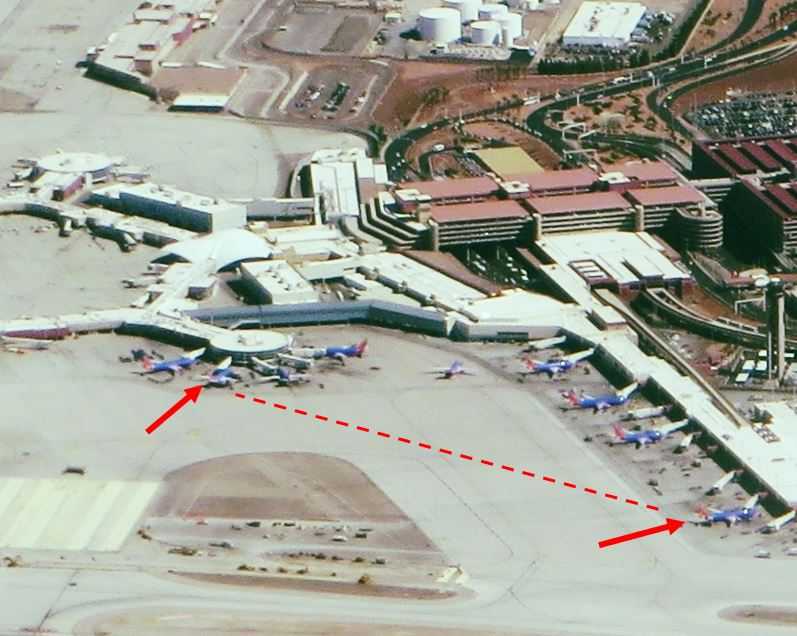
Repositioning on Aircraft Centerline
A pushback tractor is briefly required in instances when an aircraft parks incorrectly on an aircraft stand. Let us explain what incorrect parking means in this context.
Every aircraft stand has a center line with reflective paint that is used for guiding the aircraft on an aircraft stand. When aircraft approaches for parking, its nose wheel must be kept on the referred centerline so that it doesn’t end up parked too much on the left or on the right.
Since different aircrafts have different geometries, the aircraft centerline has stop positions, also known as stop bars, to indicate where nosewheel of each aircraft type must stop so that the aircraft neither parks too far behind nor too far ahead.
In this way, centerline and stop positions on an aircraft stand keep the aircraft horizontally and longitudinally centered.
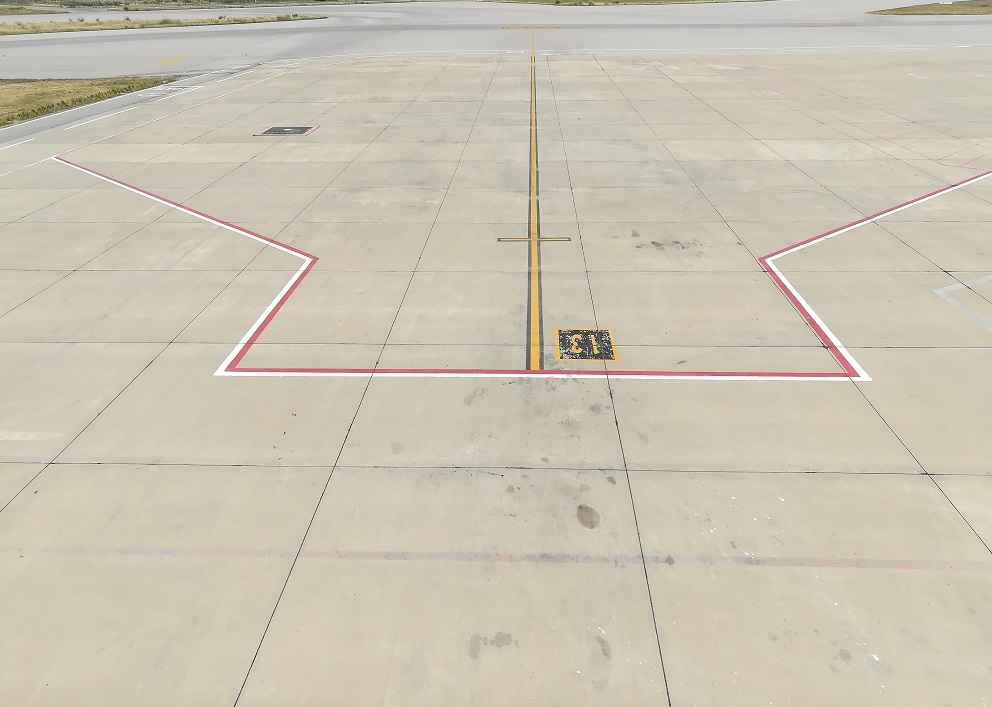
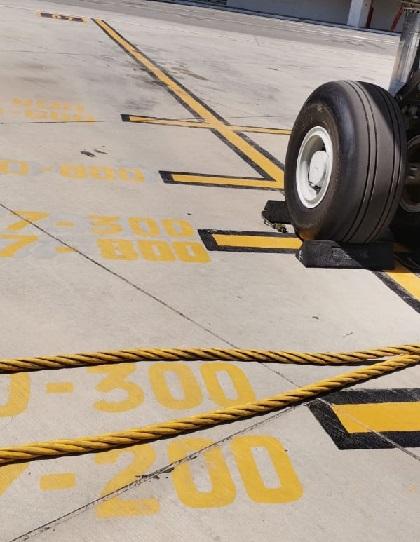
So, what is the role of pushback tractor in all this?
Sometimes, the aircraft nose wheel crosses its stop position on the centerline and moves too far ahead its designated parking position.
It happens if the marshaller (the official who guides the aircraft with hand signals) makes a mistake and delays the stop signal causing the nosewheel to move past the stop bar or if there is a shortcoming in Pilot’s judgment to apply brakes or comprehend marshaller signals.
Whatever the reason, the aircraft cannot reverse itself to get back on its designated stop position. A pushback tractor is used to push the aircraft nosewheel back to its stop position.
Such a scenario creates quite a hassle on the ramp because it costs airlines time and money. It takes at least 5 minutes to engage pushback tractor and push the aircraft back to its stop position.
Moreover, if the pushback tractor is not owned by the airline itself, services of a ground handling agency (GHA) have to be acquired. GHAs generally have fixed charges for usage of pushback tractor and they don’t offer a discount for 5 minutes usage.
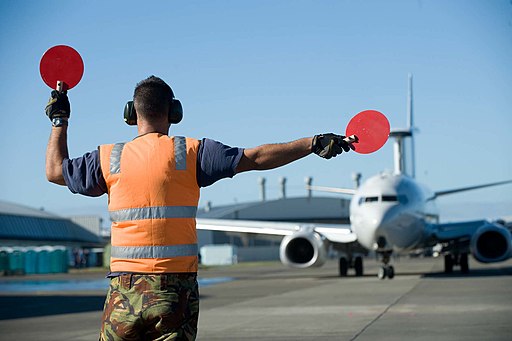
Why is it called a tractor?
The story goes back to early days of aviation when airplanes used to land on open fields instead of concrete runways we have today. After landing, the nearest tractor available on the field was hooked to the aircraft to move it around. Although, engineers later developed a specialized vehicle for this job, but the name stuck and is still used today.
Why can’t aircraft move by itself?
It is obvious that an aircraft has its own engines so why can’t aircraft reverse itself from the aircraft bay? Why can’t aircraft move from one point to another at an airport on its own? After all, no pushback tractor is needed to maneuver an aircraft from the runway to airport gate after its landing. All these questions are valid and require scientific answers.
Starting with the pushback operation, let’s discuss why can’t an aircraft reverse itself from the bay. Majority airliners do have a reverse thrust mechanism that can theoretically allow it to reverse from the bay. This reverse thrust mechanism is used by pilots to slow the aircraft down after it has landed.
The reason why reverse thrust cannot be used is that it reverses the direction of jet thrust that can prove itself to be very dangerous on the bay. An aircraft bay is designed in a way that airport building and facilities are located in front of the aircraft.
Aircraft engines produce thrust by expelling high temperature and high velocity air behind the aircraft (and thus force the aircraft to move forward by Newton’s law of action and reaction). Reverse thrust mechanism will reverse the thrust and direct it towards the airport building and facilities such as the Passenger Boarding Bridge (Jet Bridge).
Due to this reason, an aircraft cannot reverse itself and thus requires an aircraft pushback tractor to push it back from the bay.
It is clear why an aircraft cannot reverse itself from the bay, however, the question that why can’t aircraft move from one point to another on an airport still remains. The answer lies in economics of jet engines vs. pushback tractor for on-ground movement.
An aircraft jet engine is not designed for moving an aircraft on ground at 10-30 km/hr (typical taxiing speed). It is designed for moving an aircraft at 700 km/hr cruising speed. Its fuel efficiency does not follow a linear pattern where lowering the speed would lower the fuel consumption by the same factor. Jet engines are as much fuel inefficient at low speeds as they are fuel efficient at their optimal speeds.
On the other hand, an aircraft pushback tractor has a diesel engine, gearbox and chassis especially designed for high torque and low speed operation. Its fuel consumption is far lower than a jet engine in the speed range typical for ground handling.
Due to above reason, airlines and ground handling agencies use pushback tractors for on ground maneuvering of the aircraft.
How a Conventional Pushback Tractor Works?
Now that we have developed a basic understanding of the purpose of a pushback tractor and its different uses, let us discuss the design of a conventional pushback tractor and how it works from a technical point of view.
A conventional pushback tractor is a diesel engine powered vehicle with a chassis design that keeps its body very low to the ground. The reason for low profile is to avoid collision with aircraft nose and keep a low centre of gravity that helps with stability.
A pushback tractor pushes the aircraft back by hooking itself to the aircraft with its towing hook – a special hook located on the nose landing gear (commonly referred to as the NLG).
Pushback tractor chassis needs to be as low to the ground as possible to ensure that the line of action of force at the time of pushback operation remains as much straight as possible to avoid bending of the towing bar – we’ll discuss shortly what tow bar is.
If the line of action is not straight, pushback tractor will tend to bend the towing hook more than trying to push the aircraft.
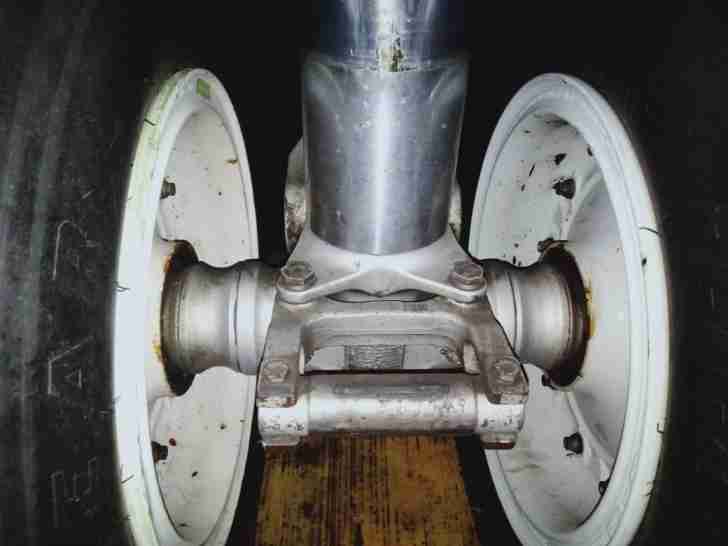
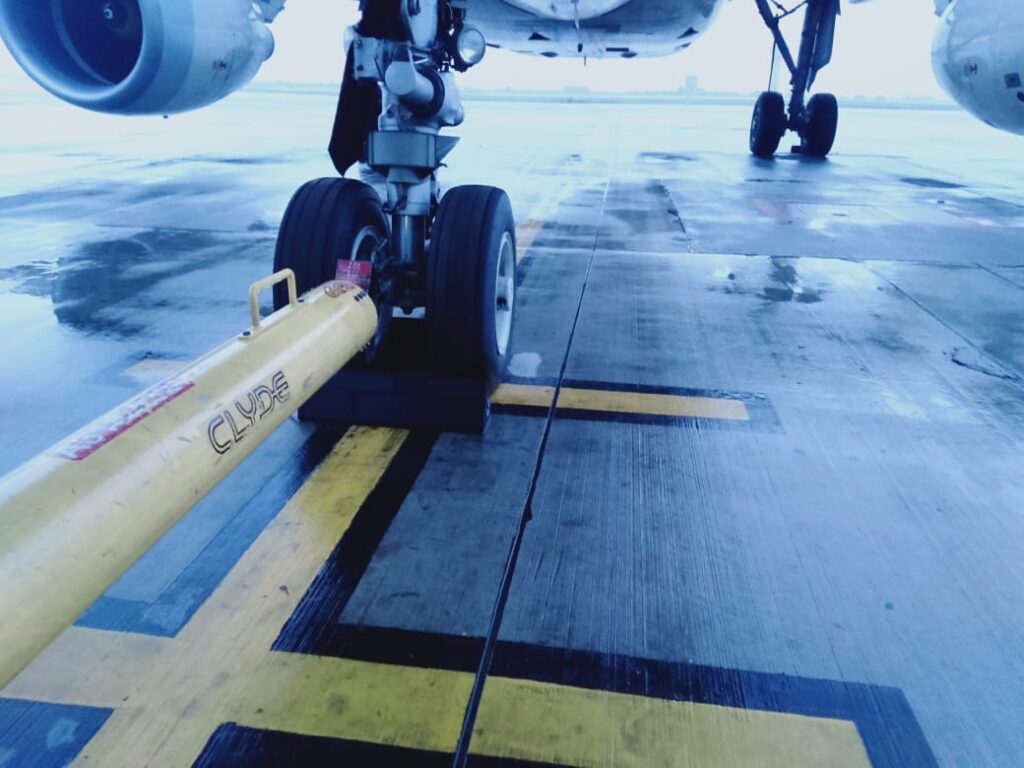
Pushback tractor is characterized by its large wheels to increase its tires contact patch and provide necessary traction during aircraft pushing/towing.
Just like a muscular person won’t push a heavy object with slippery feet, a powerful diesel engine won’t push the aircraft unless its tires provide good traction.
A conventional pushback tractor is built extremely heavy. For example, a pushback tractor compatible with wide body aircrafts can weigh upwards of 50 metric tonnes.
This weight is not necessarily of its own components but of extra ballast weight that is added in pushback tractor’s chassis to improve traction by increasing coefficient of friction and avoid wheel slippage during operation.
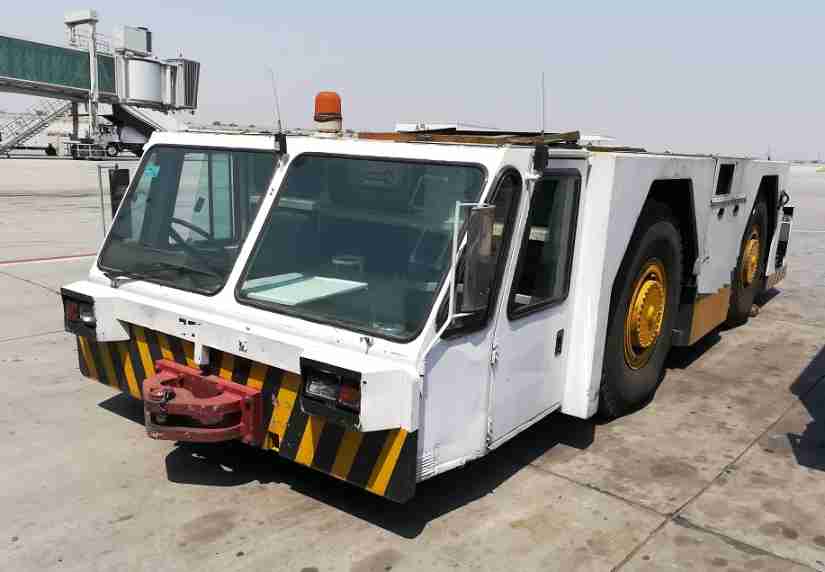
How Pushback Tractor Capacity is Worked Out?
Every manufacturer makes pushback tractors in different models, specifications and capacities. These differences arise out of the different aircraft types to be pushed as well as the airport conditions.
Different models and types of pushback tractors are based on four main factors,
- What is the maximum weight of aircraft it needs to push?
- What is the slope of apron surface?
- How many engines are running at idle at the time of pushback?
- What is the surface condition?
Let’s discuss the first factor first i.e. weight of aircraft.
Weight of an aircraft depends on its size as well as its loading condition. The parameter used in aviation to represent weight of an aircraft is Maximum Takeoff Weight (MTOW). It is the maximum weight of the aircraft at which the pilot is allowed to takeoff.
For example, the MTOW of Airbus A320, a narrow body airliner, is around 70 metric ton. Similarly, the MTOW of Airbus A350, a wide body airliner, is around 270 metric ton. The MTOW of the largest passenger aircraft, the Airbus A380, is over 500 metric ton. The larger the MTOW of an aircraft, the more powerful a pushback tractor needs to be.
The second factor is slope of surface on which the pushback operation is taking place. Ideally, surface of apron is perfectly flat, however, many airports can have a slight slope in their surface that makes pushback operation more difficult for the tractor.
The maximum slope generally considered in pushback operations for determining pushback tractor capacity is 2%.
After weight and slope comes the third factor i.e. number of running engines at the time of pushback.
Just before the pushback operation begins, Pilots turn on at least one of the aircraft’s jet engines at idle speed. Sometimes, both the engines are turned on to prepare for taxiing and takeoff.
Therefore, a pushback tractor not only has to fight the weight of the aircraft and surface slope but also the thrust produced by jet engines at idling speed.
Last but not the least, surface condition also affects pushback tractor power requirement. The surface condition here refers to snow or rainwater that may be present on apron surface at the time of pushback operation.
Water or snow makes the surface slippery thereby reducing traction of pushback tractor. In order to counter this, ballast weights have to be added to increase pushback tractor’s weight to compensate for this loss. When weight is increased, more power is required from the engine.
The surface condition factors are most prominent at airports like Chicago O’Hare International airport where subzero temperatures in extreme winter conditions affect nearly half of the flights operating at the airport.
Based on above factors, airlines and ground handling agencies procure and maintain multiple models of pushback tractors to serve different aircraft types in different conditions.
Aircraft manufacturers provide information about towing requirements in their manuals as well. These requirements are presented in a form of chart where the above four parameters are combined to figure out the capacity of pushback tractor.
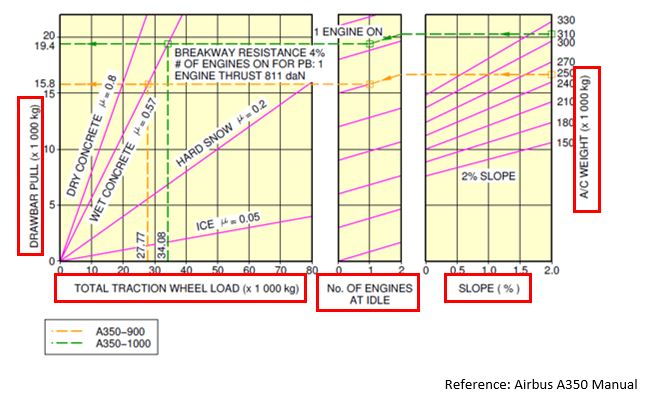
Main Specifications of Pushback Tractor
In view of the factors determining the requirement of pushback tractor capacity, the main specifications of a pushback tractor include,
- Drawbar Pull
- Weight of pushback tractor itself
- Maximum weight of the aircraft it can push.
The above specifications are not independent of each other. They are interconnected and we’ll explain how.
Drawbar pull is the amount of horizontal pulling force a pushback tractor can exert in kilo Newtons (kN). Greater the drawbar pull rating, more powerful is the tractor and greater the aircraft size it can work with. Drawbar pull is a function of the tractor’s diesel engine power and its chassis integrity.
Weight of the pushback tractor represents its power to hold its ground when the engine is doing its job. Quoting the same example, a powerful weightlifter wouldn’t be able to pull a heavy object with slippery feet.
Weight of the pushback tractor provide traction and prevents the engine’s power from going into waste by spinning tractor’s wheels at their own place.
Manufacturers specify the stock weight of the tractor as well as ‘ballasted weight’. Ballasted weight refers to adding additional weight in pushback tractor to improve its traction for more demanding pushback operations such as pushback during rain.
The above two factors combined determine the maximum weight of the aircraft that pushback tractor can work with. It also determines the aircraft families with which the pushback tractor is compatible.
For a more practical understanding, let us present example of different models of pushback tractors made by Trepel – a GSE brand,
Model | Max. Aircraft Weight (Metric Tonnes) | Drawbar Pull (kN) | Tractor Weight (Metric Tonnes) | Ballasted Weight (Metric Tonnes) | Supported Aircraft Family |
Challenger 150 | 160 | 101 | 9 | 15 | Airbus A320 & Boeing 737 Family |
Challenger 280 | 300 | 209 | 24 | 28 | Airbus A350 & Boeing 787 Family |
Challenger 430 | 380 | 304 | 27 | 43 | Boeing 777 Family |
Challenger 550 | 450 | 369 | 50 | 60 | Up to Boeing 747-800, the Jumbo Jet |
Challenger 700 | 600 | 498 | 40 | 70 | Up to Airbus A380, the largest passenger airliner in the world. |
Tow Bar
A conventional pushback tractor attaches itself to the aircraft’s nose landing gear through a simple piece of equipment called a tow bar.
It is a simple cylindrical steel bar with hooks at both ends. At one end, it engages with the aircraft towing hook on its nose landing gear. On the other end, it hooks up with the pushback tractor. Force applied by the pushback tractor is delivered to the aircraft nose landing gear through the tow bar.
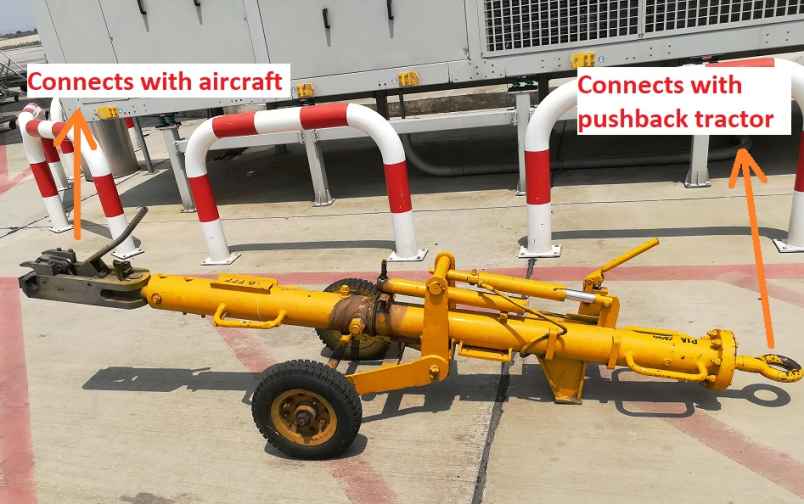
Different aircraft types have different designs of nose landing gear. Therefore, same tow bar cannot be used on all aircrafts. A tow bar can be used only on a family of aircrafts that have similar design of nose landing gear.
Any airline or ground handling agency that has a conventional pushback tractor will always maintain an inventory of towing bars to accommodate different aircraft types it operates.
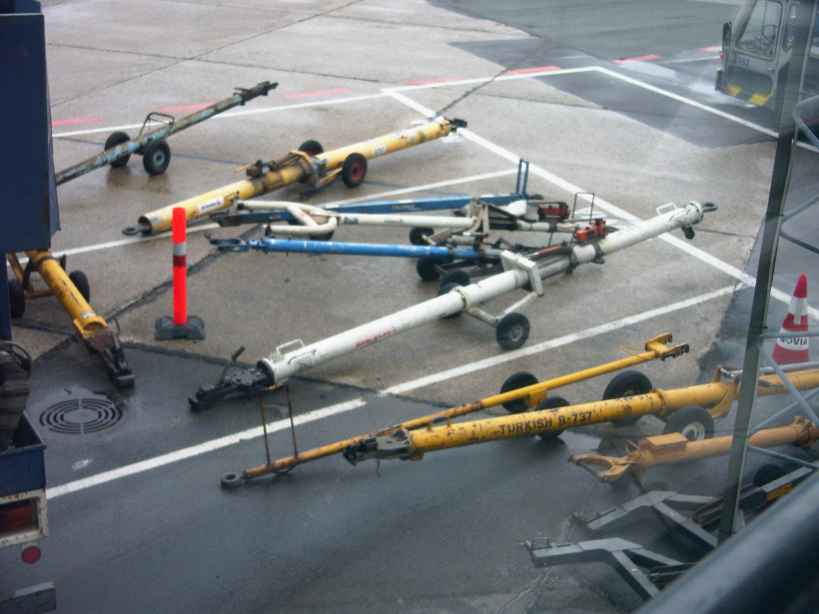
Since companies that manufacture the towbars are aware of these stresses that act on the towbar during pushback operation, they have come up with an ingenious way of integrating safety in the design of their towbar. It would be interesting to note that a small metal pin has the ability to save aircraft nose landing gear and pushback tractor from accidents. It is called a shear pin.
Shear pin has one purpose. If the forces acting on the towbar exceed a safe limit, the shear pin collapses and prevents those forces from getting transmitted to the aircraft nose landing gear. The design of shear pin and its functionality in the towbar is not difficult to understand.
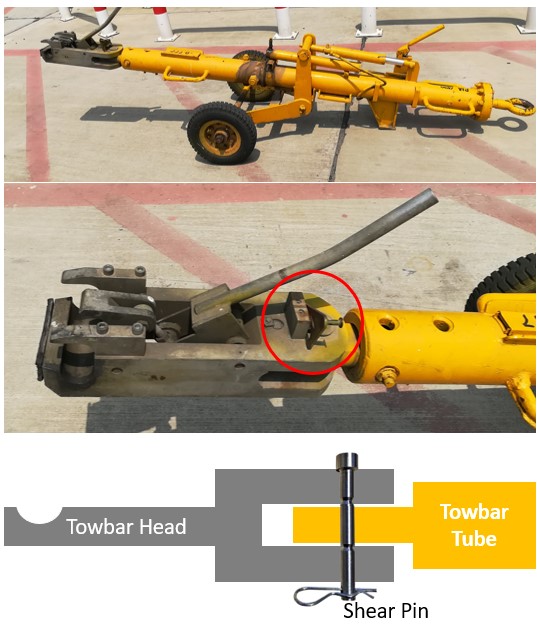
It is located in the towbar head that is attached to the aircraft nose landing gear. It keeps the towbar tube and towbar head aligned with each other as long as the forces acting on the towbar don’t become abnormal. When such forces become abnormal, the shear pin shears and the towbar head collapses. The resulting misalignment is immediately noticeable by the pushback crew so they may stop the procedure.
It is important that pushback crew keep a check on the failure of shear pin as apron is quite noisy and there are chances of the shear pin failure going unnoticed.
The Tow Bar Less (TBL) Pushback Tractor
One major innovation in the area of pushback tractor technology has been the development of a Tow Bar Less Pushback Tractor.
A Tow Bar Less (TBL) towing tractor or pushback tractor does not use a tow bar to attach itself with the aircraft. It has a hydraulic system that lifts the nose wheel assembly of the aircraft off the ground and supports it on its own chassis.
It then tows the aircraft from one point to another until it reaches its destination. There, it releases the aircraft nose wheel assembly and aircraft continues on its own.
Since an aircraft weight is distributed between its three landing gears (one at nose and two rear landing gears), pushback tractor supports a major share of the aircraft’s total weight on its own chassis. This weight fulfills the traction and friction requirements that were necessitating the use of ballasts on a conventional pushback tractor. Due to these reasons, tow bar less pushback tractors are lighter in weight.
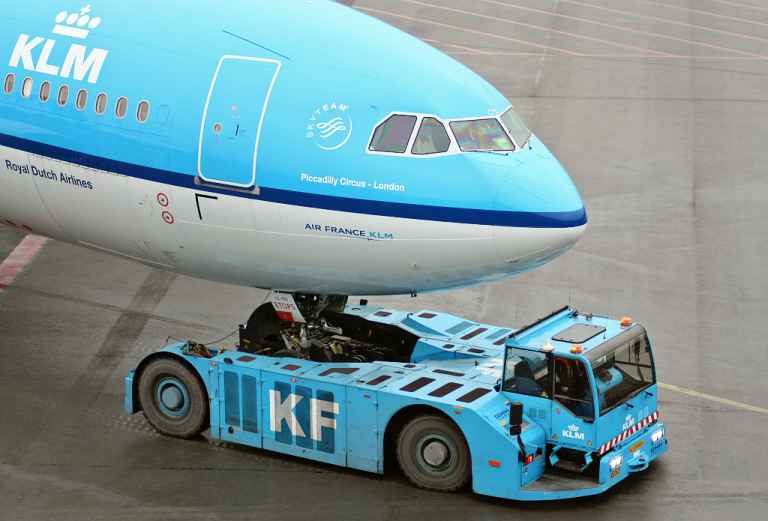
Main advantages of Tow Bar Less (TBL) Tractor
A TBL tractor has following main advantages over a conventional pushback tractor,
- A TBL tractor is lighter in weight than a conventional towing tractor due to which it is more fuel efficient. This is so because a conventional towing tractor’s engine has to carry 50 metric tonnes of weight even when it is not pushing or towing an aircraft, whereas a TBL towing tractor does not.
- Reduced weight of a TBL tractor also brings cost savings on maintenance as engine, gearbox, chassis and other components work under reduced load and wear and tear is less than in conventional tractors.
- With a TBL tractor, airlines and ground handling agency don’t need to maintain any inventory of tow bars because TBL tractors don’t engage with the towing hook of the aircraft. Although there are different variants of TBL tractors as well but they are generally based on their weight handling capacity. All things considered, any given TBL tractor will handle multiple aircraft types without the need of any tow bar.
Latest Advances in Pushback & Towing Technology
The technology of pushback and towing operations is continuously evolving with more and more innovations being introduced over time. In this regard, let us discuss some of the popular pushback and towing technologies,
Taxibot
Taxibot is a towing tractor developed by Israel Aerospace Industries is a Tow Bar Less tractor with an onboard computer system that receives instructions from pilot and has its own software program to allow aircraft on ground maneuvering under pilot’s control.
The main innovation is giving the control of taxiing to the pilot in a way that pilot feels the most comfortable with. Pushback is not controlled by pilot because pilot does not have a clear line of sight of what is behind the aircraft.
However, once the pushback operation has been completed, driver transfers the control over to the pilot. Pilot uses aircraft controls to maneuver the aircraft just as if the jet engines are on and pilot is taxing on its jet engines. Pilot controls the acceleration, steering and braking of the tractor from the cockpit.
TaxiBot is in routine operation in India since 2019 while being tested in Amsterdam in 2020. Corendon Airlines was the first airline to operate TaxiBot in India, after which KLM and Transavia tested TaxiBot.
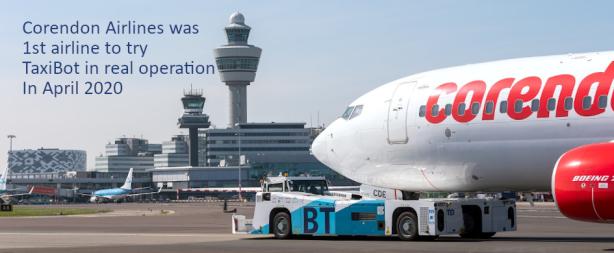
Mototok
Mototok is a remote controlled electric towing vehicle that works in the same way as a TBL towing tractor, however, it is remote controlled by a ground staff instead of being driven by a driver.
It has an extremely compact design, a full electric drive and rests the nosewheel on its chassis just like a TBL towing tractor. Once the nose landing gear (NLG) has been lifted, a ground staff steers the pushback operation as if a child is playing with a remote controlled toy car. It eliminates the need for rigorous training and driving license required in conventional tractors.
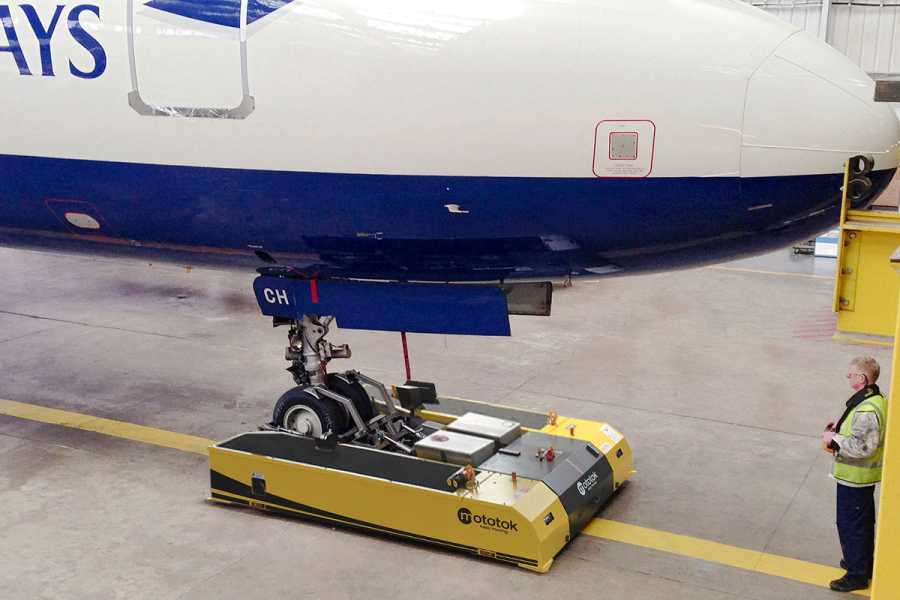
The primary advantage of Mototok tug is its simplicity of use. It provides a clear view of the aircraft and its surroundings from all angles to the ground staff who is controlling Mototok – a characteristic advantage as drivers in conventional tractors sit inside their cabins with a restricted view of surroundings and need a walk winger to guide the tractor driver about aircraft extremities during movement.
With Mototok, the operator can walk left and right to get a visual of any point he wants without the need for any walk winger. It makes the overall operation of pushback and towing more simple, precise and controlled with reduced manpower requirement.
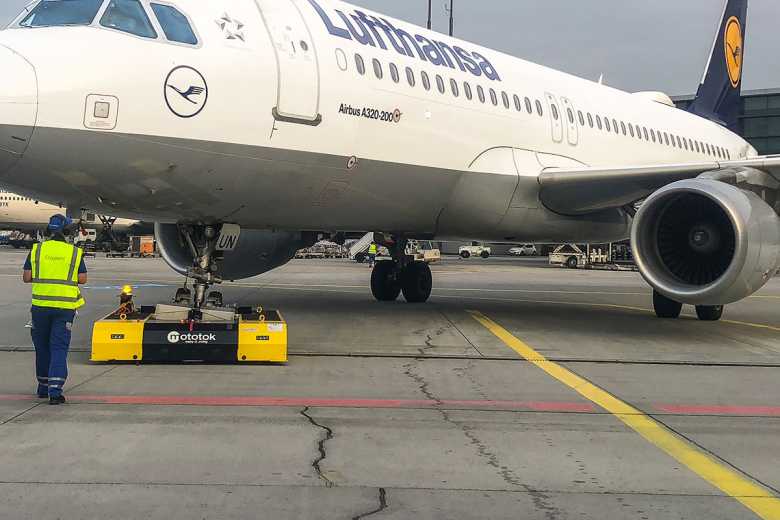
Another great advantage of Mototok tug is that its turning radius is virtually zero i.e. it can spin around the nose wheel axis of the aircraft. This feature allows for a far greater flexibility in maneuvering of the aircraft than conventional towing tractors.
Apart from above, conventional pushback tractors are very noisy piece of equipment. Since Mototok is a fully electric vehicle, it does not generate any noticeable noise – a desirable thing at the aircraft stand where there are already too many pieces of machinery generating lots of noise.
Mototok tugs are used not only at airport but inside hangars and even production facilities because these tugs can maneuver and park aircrafts more precisely than conventional tractors.
In hangars, they can be used for parking aircraft much closer to each other than possible with a conventional tractor allowing the hangar to contain more aircrafts than possible before. In production facilities, it can be used to maneuver the aircraft from one assembling station to another.
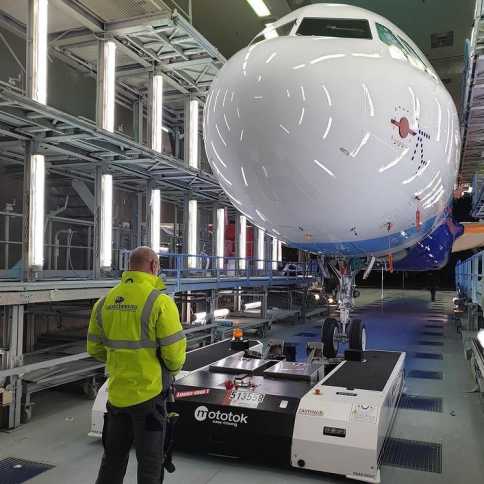
(Photo – Courtesy of Mototok)
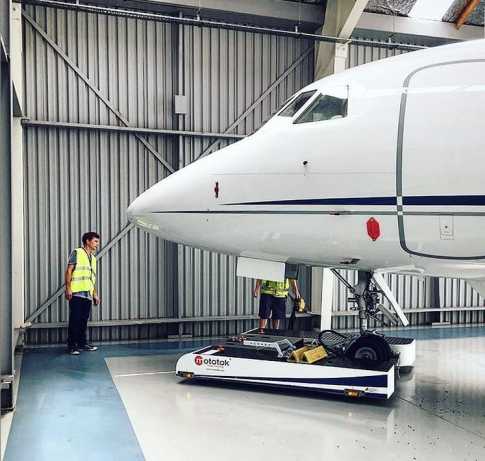
WheelTug
WheelTug is a technology under development by a company of the same name. It is not a towing tractor but the name of a concept where powerful electric motors are coupled with aircraft nose wheels that allow aircraft on-ground maneuvering without the need for turning on the main engines or calling a pushback tractor for assistance.
The chief advantage of WheelTug technology lies in eliminating external support required by the aircraft to move on ground in the form of pushback tractors. It makes the aircraft self-sufficient and gives control of ground movement from pushback tractor’s driver to the Pilot himself.
The electric motors coupled with the nose wheels of the aircraft are high torque low speed motors powered by aircraft’s own electrical system energized by the Auxiliary Power Unit (APU). The idea is that Pilots can maneuver their aircraft themselves whether it is movement between aircraft stands, into the hangar or on the taxiway.

With this we conclude our topic. If you liked our article, please do share it with likeminded people as it helps our efforts to reach people who can benefit from it.
If you are interested in obtaining a base level knowledge about all the different types of aircraft ground support equipment and operations, Check out this 3 Hour video based course on Udemy that explains each of nearly 20 different aircraft ground support activities and equipment.