One of the most important topics in airport ramp safety is aircraft refueling safety procedures and precautions. It is the ground handling operation with the highest risk factor as compared to other operations.
While we have a separate article on explaining the refueling equipment and refueling infrastructure at airports, today’s article focuses only on the safety aspects associated with aircraft refueling based on its criticality as a topic in itself.
On 05th September 2001, British Airways flight no. 2019 arrived at Denver International Airport, United States from Gatwick International Airport, United Kingdom. Starting the refueling procedure, the operator used a lift platform to reach the aircraft fuel receptacle (or coupling) and connected the fuel hose.
During refueling, the maintenance engineer standing on ground noticed that the fuel hose coupling separated from the fuel access panel in an angled direction gushing fuel all around. The operator was not facing towards the fuel access panel at that instant, therefore the maintenance engineer yelled at the refuel operator that the hose is loose.
The fuel spurted everywhere such that the maintenance engineer was immediately soaked in fuel and even swallowed some. Suddenly fire emerged and engulfed the refuel operator who was still in the lift platform. The matter was noticed by other ramp agents and fire vehicles immediately reached the spot and extinguished the fire.
However, aircraft and the fuel truck sustained fire damages. Unfortunately, the 24 year old refuel operator remained hospitalized but died from his injuries a few days after the accident.
We’ll discuss the root cause of the above accident shortly in this article, however, the incident and the unfortunate loss of a life teaches us why refueling an aircraft is dangerous. It is dangerous because aircraft refueling carries risk of causing a fire that not only causes financial loss but poses threat of loss of life as well.
Therefore, knowledge of the potential risks and hazards associated with aircraft refueling and how to mitigate them is important for any person involved in aircraft ground handling. This is what today’s article is all about.
Preflight Inspection of Aircraft Refueling Equipment
Before the aircraft arrives and aircraft refueling crew starts the refueling operation, there are some important safety checks to be made.
First is the proper preflight inspection of refueling equipment. Whether it’s a refuel truck or a fuel hydrant dispenser, a routine check is necessary to ensure that the equipment is in normal condition. The inspection is a walkaround of the equipment with a visual inspection of fuel hose, gauges, tires and the overall body of the truck. This inspection needs to be conducted at least 10-15 minutes prior to Estimated Time of Arrival (ETA) of the aircraft.
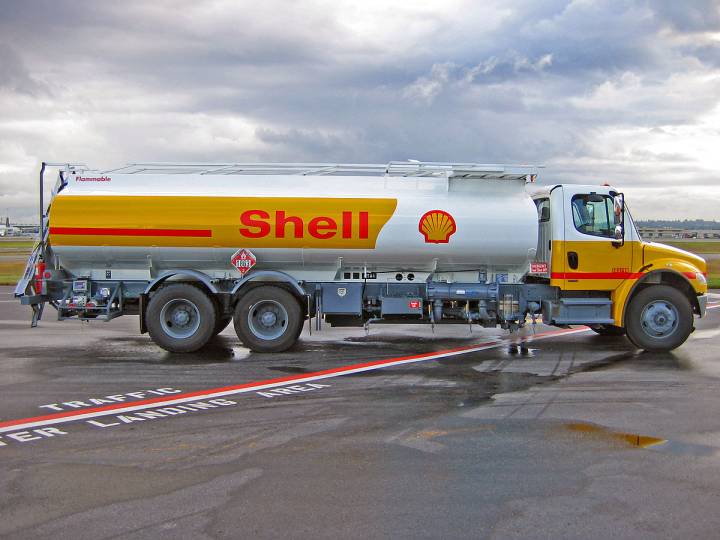
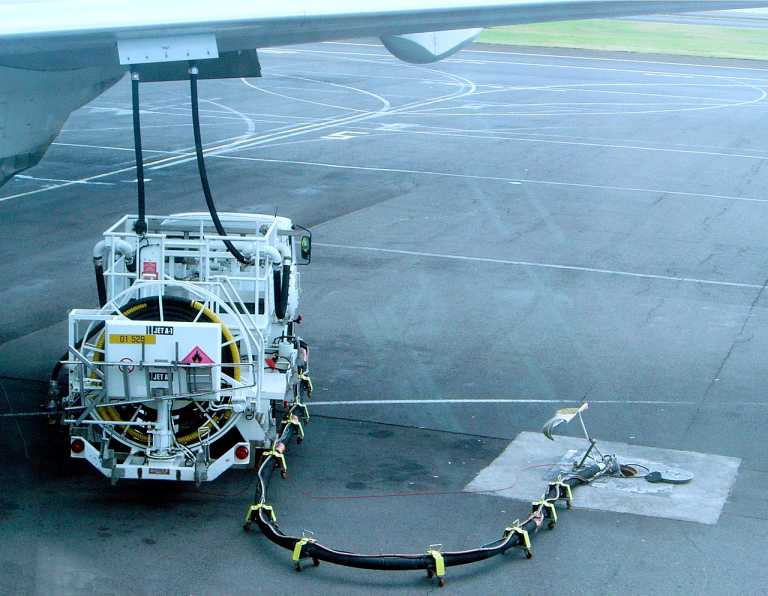
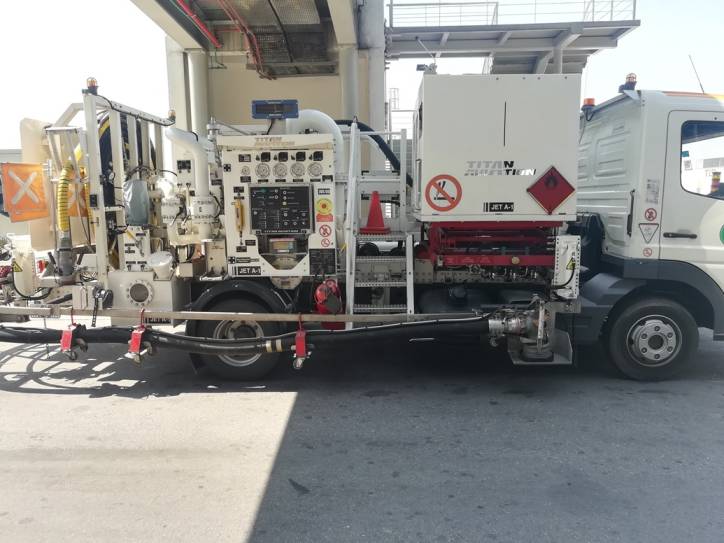
Aircraft Refueling Under Adverse Weather Conditions
Bad weather conditions are needed to be checked. Refueling operation must not be initiated if there are electrical storms close by the airport. Moreover, if airport is experiencing lightening, refueling must be stopped.
It is important because during aircraft refueling operation, fuel vapors are present around the aircraft especially near the aircraft fuel tank vents located in the wings of the aircraft. These vapors can ignite due to a lightning strike thereby posing a great safety risk.
How Type of Jet Fuel Affects Aircraft Refueling Safety
The type of jet fuel being used for fueling the aircraft also affects safety. There are two main types of jet fuels in this context:
- Wide Cut Gasoline (Such as JET-B or JP-4 or equivalent)
- Kerosene (such as Jet-A, Jet-A1, JP-8 or equivalent)
The type of jet fuel being worked with decides the safety precautions to be taken while handling it.
The first type i.e., the wide cut gasoline is made up of 70% gasoline and 30% kerosene. It requires greater safety precaution in handling because it is comparatively more flammable than kerosene. If wide cut gasoline is being worked with, passengers must neither be present in the aircraft nor should they be allowed to board or exit the aircraft.
With Kerosene based fuels such as the Jet-A or Jet-A1, passengers can board or exit the aircraft with certain safety precautions, the most important of which is readiness for emergency evacuation.
Readiness for Emergency Evacuation in Aircraft Refueling
The first most important aspect in the readiness for emergency evacuation is that aircraft refueling takes place while other ground handling operations are also under progress such as cleaning and catering. It poses risk of congestion and blockage of evacuation route for passengers at the time of emergency. Therefore, it is of critical importance during aircraft refueling to keep the aircraft aisles clear from obstruction and keep aircraft 1L and 2L doors clear for passengers for a possible emergency exit.
Another measure with respect to the readiness for emergency evacuation is that passengers may be informed through an announcement (or by the flight attendants) not to fasten their seat belts while the aircraft refueling is in progress. The supervisor of aircraft refueling crew must remain in coordination with flight crew to inform them when the refueling begins and when it is completed. Flight crew may give directions to passengers regarding seat belts accordingly.
It is also important for the flight crew to keep a notice of anything unusual inside the aircraft during refueling such as smell of fuel inside passenger cabin. Flight crew is used to how ‘normal turnround operation’ feels. Therefore, anything felt out of the usual must be given a check just for safety.
Aircraft Refueling Accident Case Study – Importance of Maintenance
Maintenance of refueling equipment is as important for ensuring aircraft refueling safety as any other measure taken during operation. Refuel equipment comes with many built in safety interlocks that are needed to be maintained by the maintenance team to make sure they function as expected in the hour of need. Healthy equipment is less likely to cause any accident than an unhealthy one.
Joint Inspection Group – an organization dealing with developing aviation fuel standards shared an accident report where two aircraft refueling trucks collided with each other.
Both of the aircraft refueling trucks had been travelling to an aircraft stand one behind the other, when the brake safety interlock mechanism of the truck in front got activated due to a malfunction and suddenly stopped the truck. The truck directly behind it ran into the truck in front causing a dangerous accident.
The cause of accident was attributed to the malfunctioning safety interlock and the inability of the driver to maintain a safe distance from the vehicle in front of him. Therefore, proper maintenance is important to make sure chances of such malfunctions are reduced.
Testing Jet Fuel Quality Before Refueling
A very important part of aircraft refueling before the operation is executed is carrying out testing of jet fuel before pumping it in the aircraft. The primary concern is the presence of water in fuel. For that, specific gravity test of fuel is carried out on the ramp each time before refueling is conducted.
The test makes sure that fuel is not contaminated with water. There have been many flight accidents in history caused by contamination of fuel by water resulting in abnormal operation of jet engines. Apart from water there are other contaminants also.
However, jet fuel quality control is in itself a topic for another article another day. At this stage, what’s important to remember is that quality of jet fuel is so significant that an onsite quality check is performed on the ramp on every flight in which the aircraft is refueled.
Correct Way of Parking Aircraft Refueling Truck for Safety
Safety in aircraft refueling starts with correct parking of the refuel truck on the ramp. Whether it is a fuel hydrant dispenser or a refuel truck, it must be parked in a way such that it is always ready for an emergency exit.
For this purpose, the aircraft refuel vehicle must never be positioned with its front towards the aircraft. Its front must always be in the direction of a possible escape route away from the aircraft. This escape route must not be blocked by any other object or vehicle such as another Ground Support Equipment (GSE).
The escape route must always be clear as if an emergency exit of refuel truck can take place at any time. It is important because in case of any fire or fuel spill, it becomes extremely important to remove the refuel truck from the site immediately so that the truck neither becomes a source of fire itself nor create obstruction in the path of firefighting.
Aircraft refuel trucks are more dangerous than aircraft fuel hydrant dispensers in this regard because they are carrying all the fuel in their tank and they themselves are a great fire safety hazard on the ramp.
Fuel Hydrant Dispensers don’t carry aviation fuel like refuel trucks, but they do carry fuel for the vehicle itself. Moreover, the fuel that remains in its hoses, filters and piping remains a safety hazard in case of fire. Needless to mention that it is coupled with an underground fuel source with virtually unlimited fuel supply.
The more sources of fuel are there in an event of fire, the more chances of spreading the fire. Therefore, the way a fuel truck is parked may seem trivial, however, it has the potential to both escalate or contain the situation in case of an emergency.
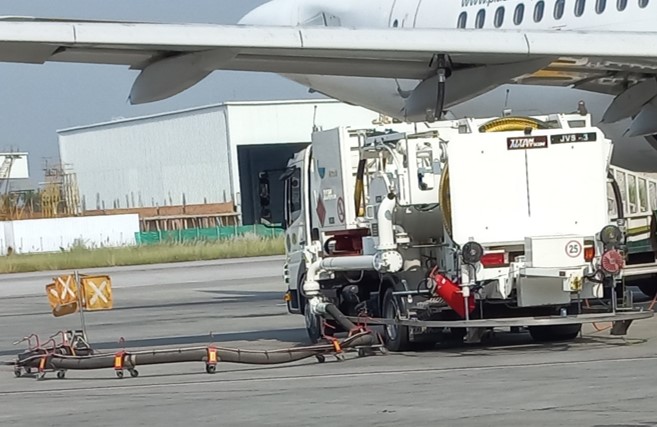
Apart from above, the fuel truck has to be parked with consideration of how fuel hoses will be connected with aircraft fuel coupling so as not to put unnecessary strain and stresses on the fuel coupling. The truck must be positioned such that its bucket (or lift) that houses the fuel hoses fall under the fuel access panel located under the aircraft wing.
The aircraft refueling accident we discussed at the start of this article is referred again. The accident was investigated by National Transportation Safety Board concluded that the probable cause of the accident was incorrect positioning of the fuel hydrant dispenser that applied an angled force on the fuel hose coupling connected under the wing of the aircraft.
The same force was responsible for fracturing the fuel adapter ring that led to leak in the pressurized fuel flow. However, the source of fuel ignition could not be found. The accident highlights the importance of a seemingly small safety procedure in aircraft refueling.
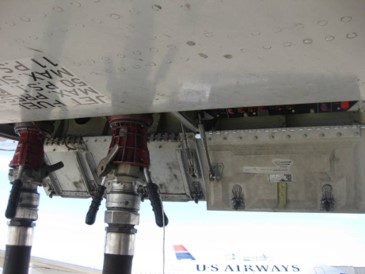
Aircraft Refueling Grounding (Bonding)
Once the aircraft refuel truck is correctly parked, a critical safety precaution is grounding (or bonding) of the refuel vehicle with the aircraft. Physically, there is a cable reel on the refuel truck that the refuel agent pulls out and connects with a bonding point on the aircraft, generally located in the rear landing gear.
Grounding (or bonding) is simple but is of paramount importance in refueling safety due to electrostatics. An airplane and the refueling truck, both are made of metallic parts. These metallic parts have the tendency to carry a static electrical charge. It is the same type of charge you sometimes get on your shirts that start attracting your body hair.
Another familiar example is you touching a doorknob and getting a sensation of electric shock. That is because a static charge often gets developed on the doorknob that discharges itself when you touch it.
In the same way, static charge often gets developed over aircraft body and just like you feel shock from the door knob, aircraft body also has the potential to release its static charge when it comes into contact with another object such as a refuel truck’s hose coupling that the operator engages at the time of refueling.
While the discharge of static charge from a doorknob does not produce a spark, the discharge of static charge from an aircraft can cause a spark. It is a serious safety hazard in aircraft refueling because that spark can cause ignition of fuel to cause fire. Therefore, grounding (or bonding) in aircraft refueling is critical to safety.
A bonding cable (or reel) is a simple cable that connects the metallic body of the aircraft with the metallic body of the refuel vehicle. Whatever static charge difference is there between the aircraft and the refuel vehicle is discharged through the bonding cable. It causes both of the bodies i.e., the aircraft and the refuel vehicle to get on the same level of electrical potential.
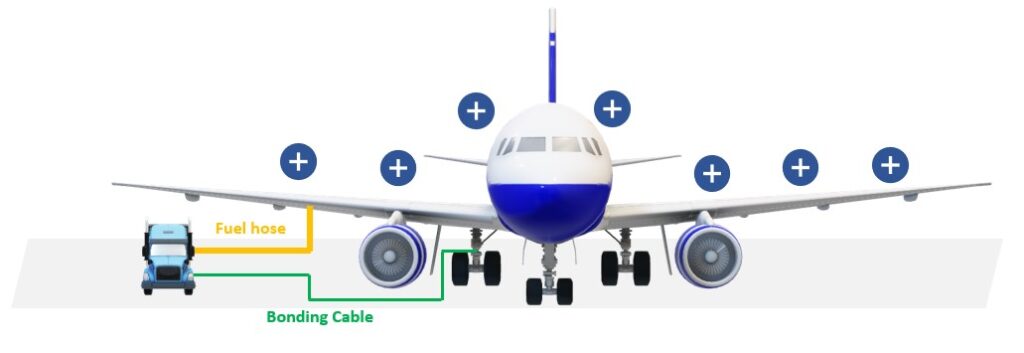
After bonding, the risk of sparking when the operator connects the fuel hose coupling with the aircraft fuel access panel is mitigated. It is because that discharge has already been killed by the bonding cable. It is interesting to note that a seemingly trivial action like hooking up a cable with aircraft body can prevent a serious ramp accident.
An important safety aspect in bonding is that the bonding connection on majority of the aircraft is located on their landing gear. While trying to make the connection on some aircrafts, the operator must take care of the hot brakes on the landing gear that can easily scorch the body as well as the bonding wire.
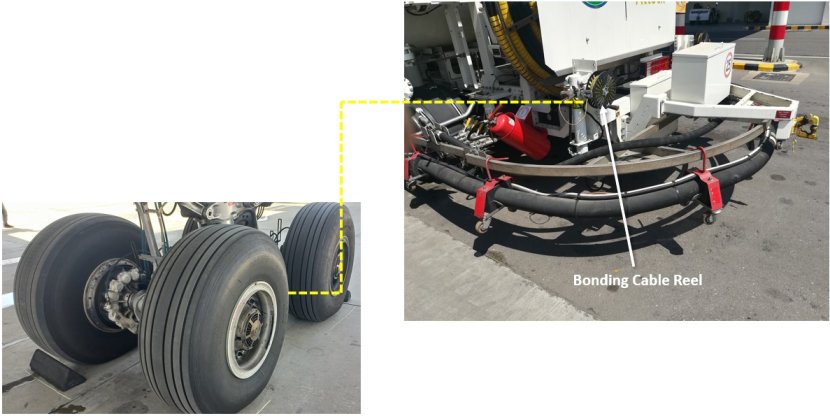
Creating Separation Between Aircraft Wheels & Chocks Before Refueling
The next safety precaution before refueling is commenced is to check that neither the aircraft nor the refuel vehicle can move from their place. For this purpose, aircraft nose wheels as well as main landing gear wheels must be chocked properly.
The general principal of applying chocks on the aircraft (or even with any other vehicle) is to place the chocks snugly against the tires. This is the position in which the chocks are applied on aircraft wheels before refueling begins.
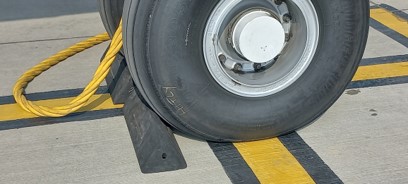
However, before beginning the aircraft refueling operation, the refueling team must create separation between the chocks and aircraft tires before commencing refueling. It is a small yet very important safety precaution.
The reason is that thousands of liters of fuel weigh several tons. For example, even a narrow body aircraft like the Airbus A320 has the capacity to carry over 27,000 liters of fuel. This amount of fuel weighs at least 20 metric tonnes. On the other hand, a wide body aircraft like Boeing 777 has capacity of carrying over 100,000 liters of fuel that weighs over 80 metric tonnes.
All this weight of the fuel settles the aircraft down in the same way a car settles down when a lot of weight is put in it. What’s most important to note is that the footprint of the aircraft tires expands when it settles down. If the wheel chocks are placed snugly against the tires during the refueling procedure, expansion of aircraft tires will cause the chocks to get pinched by the tires.
The above reason is why the refuel team must create a small separation between the chocks and wheels of the aircraft so that when the aircraft settles, there is room for the tires to expand. After refueling is completed, the chocks may be placed snugly against the tires again.
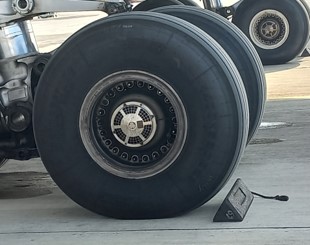
Restricting Motion of Refueling Truck – Accident Case Study
It is not only the aircraft whose wheels need to be chocked for restricting its motion. The movement of the aircraft refueling truck must also be restricted by ensuring engagement of the parking brake and application of chocks for additional safety.
Joint Inspection Group published a report of an accident in which an aircraft refuel truck driver brought the truck to the ramp and waited for the flight crew’s permission to approach the aircraft and start the refuel procedure. After waiting for a while, he got off from the vehicle to meet the pilot.
Shortly after getting off the vehicle, he noticed that the refuel truck started moving due to slope of the apron. He had forgotten to set the parking brake and had also left the vehicle’s engine running. He ran and tried to get in the moving vehicle but couldn’t do so. The refuel truck ended up colliding with a light pole.
The reason for the accident was that the driver forgot to apply proper exit procedure before leaving the refuel vehicle unattended. Engine was kept running and the parking brake was not set. A mistake in ensuring that the refuel truck’s motion is restricted resulted in a major ramp accident.
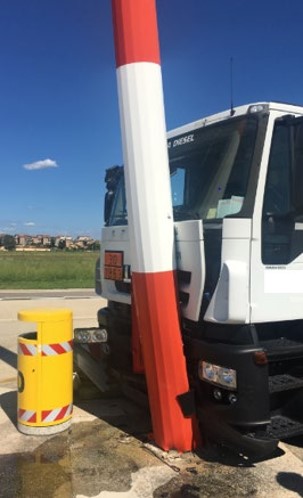
The Dead Man’s Switch in Aircraft Refueling
Once the refuel vehicle is properly parked; fuel hoses are connected in the refuel access panel of the aircraft and all other precautions of refuel setup are complete; the refueling can be started.
There is a very simple yet effective piece of technology used at this point known as the Dead Man’s Switch. It is a remote control device having a switch that is needed to be kept depressed for allowing the fuel to flow from the aircraft refuel truck to the aircraft wing.
The term commonly used in industry for pumping fuel is Uplifting because fuel is loaded in upwards direction into the wings of the aircraft. The fuel uplifting will stop if the operator releases the switch. This technology makes human supervision of refueling process mandatory by design. The remote control is wired with the refuel truck and the refuel operator is bound to remain in the vicinity of the refuel truck and keep the switch activated for refueling to work.
By ensuring human presence and supervision of fuel uplifting, safety is ensured as the refuel operator will be able to respond to any abnormal thing immediately.
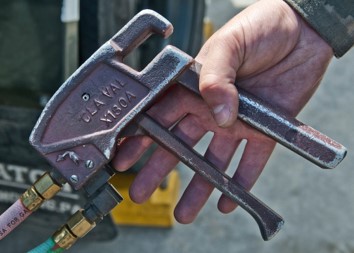
Aircraft Fueling Safety Zone
Once aircraft refueling has started on the ramp, all ramp personnel must keep their distance and observe precautionary measures from:
- The aircraft refuel truck
- The fuel hydrant pit
- The fuel hoses
- The aircraft fuel vents
This precautionary distances establishes what is technically known as the Fuel Safety Zone. The exact figure of this distance can vary based on local regulations of the country or the standards of the airline or ground handling agency. However, commonly a distance of 3 meter may be specified.
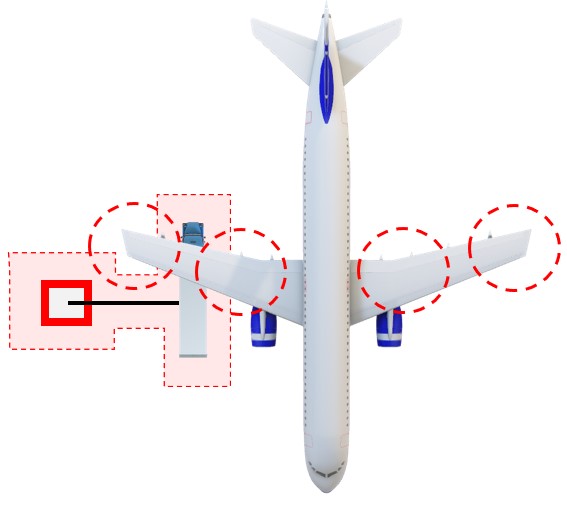
The primary safety measure for the refuel safety zone is not to enter it unless you have some business inside of it. Secondly, smoking is strictly prohibited inside this zone because fuel vapors can be present in the fuel safety zone and anything that can initiate a fire is strictly prohibited.
With the same concept, no motorized vehicle should enter the fuel safety zone and if any vehicle is already present inside the fuel safety zone, its engine must be turned off because engines also pose risk of igniting fuel vapors.
Ramp personnel must also be cautioned not to use their mobile phones or operate other electronic devices inside the fuel safety zone because electronics also pose risk of igniting vapors.
The Aircraft Ground Power Unit must also be located farthest away from the fuel safety zone because it is a high voltage and high current piece of equipment with a great risk of igniting fuel vapors.
Aircraft Functions Not to be Operated During Refueling
Flight crew must observe safety precautions inside the aircraft when refueling is in progress including:
- Aircraft weather radar must not be operated
- Aircraft High Frequency radio transmissions must not be made during fuel uplifting because the radio waves can also cause fuel ignition. The phenomenon is referred to as Radio Frequency Ignition Hazard.
- At nighttime, aircraft strobe lights must not be switched on because strobe light surfaces heat up to a high temperature that can also become a source of ignition of fuel vapors.
Preventing Jet Fuel Spill
Jet fuel spill is one of the most serious risks associated with aircraft refueling operation. In case there is a fuel pit being used for aircraft refueling, the connection between the fuel hose and the fuel hydrant pit must be properly secured.
Fuel hose from the fuel hydrant dispenser to the fuel hydrant pit lays on ground and has a risk of getting runover by some vehicle or equipment. Therefore, it is standard practice among refuel truck manufacturers to have sections of highly visible color in the fuel hose.
The fuel hydrant pit once opened up and connected with the hose is also a safety hazard with respect to any vehicle or equipment colliding with the hydrant pit coupling that could cause a serious fuel spill. As an associated safety precaution refuel crew must never forget to place the caution flag over it indicating the hazard in approaching the pit.
Such visual cues (like high visibility sections in the hose and caution flag over fuel hydrant pit) play an important role in ensuring ramp safety because they catch everyone’s eye and alerts people from running into an accident just because they didn’t notice the stretched out fuel hose and the occupied hydrant pit.
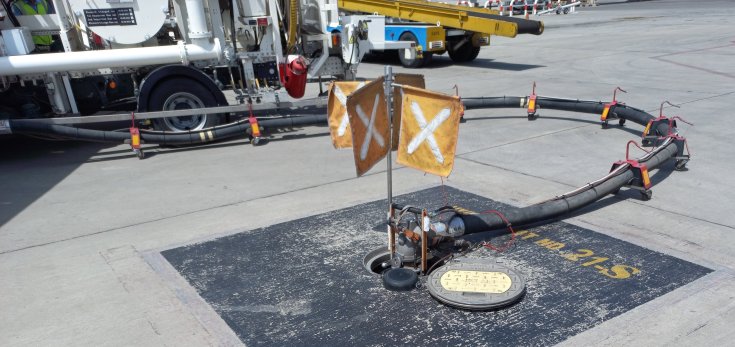
Apart from above, aircraft refuel setup also mandates availability of fire extinguishers on the ramp. These extinguishers are installed on the refuel truck as well as available separately on the ramp.
Handling Jet Fuel Spill
While the safety precautions observed in aircraft refueling reduce risk of a fuel spill, refueling crew as well as other ramp personnel must be adequately trained for handling the situation if a fuel spill has taken place on the ramp as a worst case scenario.
The most important thing to undertake in case of a fuel spill is to stop the refueling process immediately. For this purpose, a dedicated emergency stop button for fuel hydrant pit system is available on the aircraft stand that cuts off the fuel supply from the pit in case of any emergency.
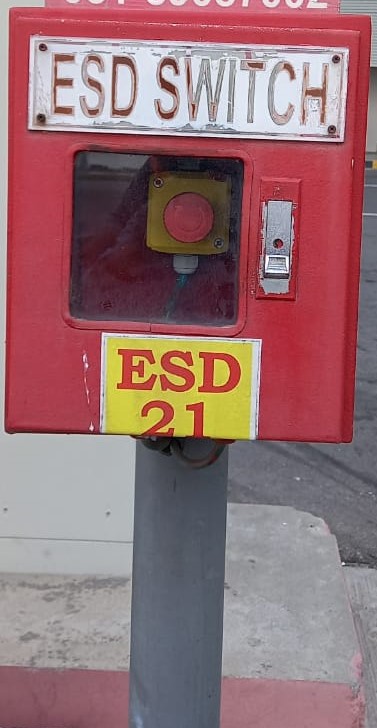
The fire department must be immediately informed and fire extinguishers on the refuel vehicle and the ramp must be used. All ramp personnel must halt their activities and create their distance from the spill. Only those personnel who are trained in handling emergencies (especially the refuel crew itself) must approach the spill.
All electrical equipment on the ramp must be switched off immediately especially the aircraft ground power unit (GPU). Engines of all the vehicles on the ramp must be turned off if possible without compromising safety as staff has to abandon their vehicles to move away from the spill.
In order to contain a fuel spill, apart from the obvious cutting-off of fuel source, using sawdust around the boundaries of the spill prevents from spreading it. The same sawdust is also used to clean up the remains of fuel spill that cannot be removed manually or through a machine.
The above activities must resume only when the emergency response team or the fire safety team has given clearance that fuel spill has been cleaned and operations may be resumed.
If you liked this article, share it with at least one person of common interest. It allows our work to be of service to people who can benefit from it the most.
If you are interested in obtaining a base level knowledge about ramp safety, check out this 7-hour video based course on Udemy that you can easily finish in a week (or binge watch in a day or two). It explains ramp safety in detail with interesting case studies of ramp accidents for in-depth understanding of the subject. It also explains ramp safety aspects associated with 13 main ground handling operations carried out on the ramp.