Aircraft Ground Power Unit (AGPU) is a type of aircraft ground support equipment that supplies electrical power to the aircraft from ground when its jet engines are turned off. AGPU is generally used when the aircraft is parked at an aircraft stand.
The electrical power requirement of an aircraft is not the same as domestic power supply. It does not require the standard 110/220 Volt and 50/60 Hz power supply used worldwide. Airliners require power at 115 volt and 400 Hz electrical frequency while smaller aircrafts like business and private jets generally require 28 Volt DC power supply.
Why Aircraft Ground Power Unit (AGPU) is Needed?
When an aircraft is in air, all of its electrical power requirements are fulfilled by jet engines i.e. the jet engines on an aircraft not only generate thrust to make the aircraft fly but also act as electrical power plants to supply power to all critical and auxiliary systems during flight.
These systems include all control systems, flight instruments, navigational aid and communication equipment and devices, electrical motor driven mechanisms; cockpit and cabin lighting system; appliances in onboard kitchen like ovens and refrigerators, passenger address (PA) or announcement system and entertainment systems such as display screens and mobile or laptop chargers.
When an aircraft lands, pilots generally keep at last one jet engine on for providing the aircraft enough thrust to taxi to the allotted aircraft stand as well as keep all of the electrical systems energized. The pilot may turn on the Auxiliary Power Unit (APU) if needed to fulfill aircraft’s power requirements.
When the aircraft reaches and stops at the aircraft stand, requirements of thrust remain no more, however, requirement of electrical power remains. The aircraft still requires electrical power during passenger disembarkation, aircraft servicing and passenger embarkation for the next flight.
Aircraft lights are required to be kept on for allowing the airline staff to undertake cleaning of passenger cabin to make it ready for the next flight. Moreover, many electrical and electronic systems are required to be kept on for allowing pilots and aircraft technicians to conduct post flight technical checks.
At this stage, pilots cannot keep the jet engines on because it is a safety hazard for ground staff that gets busy with different tasks around the aircraft.
When an aircraft is parked at an aircraft stand, there is tremendous movement all around it. You can read more about all of the different ground handling activities performed on an aircraft at an aircraft stand here.
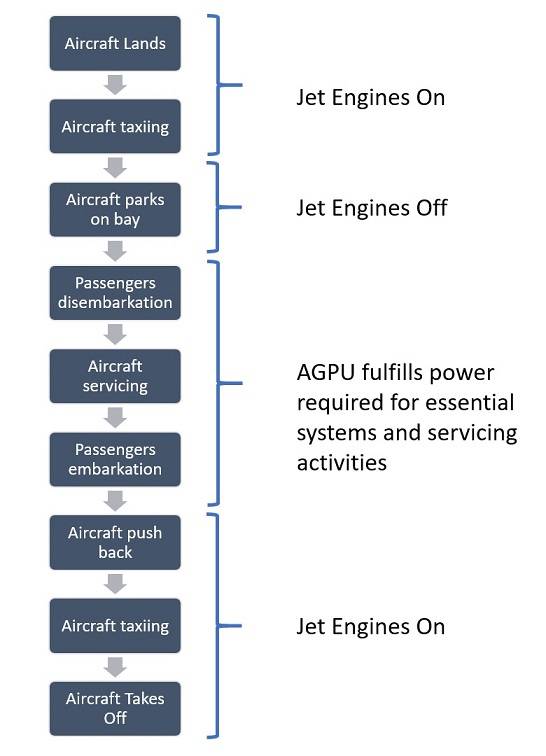
In short, if the jet engines are kept on, many of the ground support activities would not remain possible. Consequently, pilots have to choose between turning on the Auxiliary Power Unit (APU) or taking power from the Aircraft Ground Power Unit (AGPU).
Auxiliary Power Unit (APU) is a mini jet engine installed in the tail of the aircraft that can power all essential electrical and electronic systems without requiring any external aid. However, APU has two problems.
First, it generates quite a lot of noise that becomes a source of inconvenience for ground staff. Second, it is a jet engine that produces power by burning fuel that has an associated cost impact as well as produces carbon dioxide emissions.
Regulatory bodies in aviation have a very proactive approach on both occupational health and safety as well as environmental preservation. Noise produced by the APU goes against the former factor while carbon dioxide emissions go against the latter. Therefore, using an APU is discouraged and availability of 400 Hz Aircraft Ground Power Unit (APU) is encouraged and sometimes made mandatory in airport projects.

Why do aircrafts need 400 Hz power supply?
If you are reading this article, it is understood that you have a scientific and technical taste and it might have crossed your mind that why does an aircraft need 400 Hz electrical frequency? Why not the same 50/60 Hz used everywhere in the world?
The answer lies in the relation between electrical power transmission and electrical frequency and we would take some time to approach this problem from a fundamental physics aspect.
For those who don’t remember electrical frequency, just think of electrical power as energy pulses in a cyclic manner – what is called a sine wave if it rings any bell.
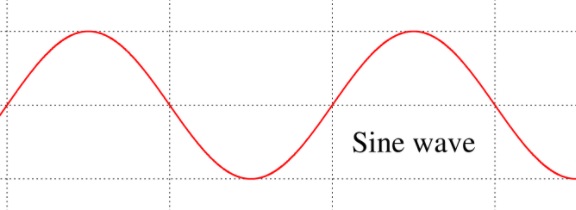
If you lower the electrical frequency, transmission losses decrease i.e. less power is lost when it is carried from point of generation to point of use. However, lower it too much and you would see your bulb flickering with the energy pulses.
On the other hand, if you increase electrical frequency, you increase transmission losses. However, with increased frequency, you can reduce the size of electric motors and some other electrical components to get the same amount of power from them. Increased frequency therefore allows more compact devices at point of use.
the Electrical frequency around the world is standardized at 50/60 Hz (that is 50/60 cycles per second) because power plants are located far from cities where bulk of electricity is used. Therefore, a decisive factor in choice of electrical frequency in domestic power generation is the transmission losses from power plant to cities.
In the past, some countries used 25-30 Hz as standard frequency, but it was later standardized at 50/60 Hz to bring the worldwide manufacturing of machines, appliances and devices at the same page – a globalization scenario.
However, the case of aircrafts is different. Weight is of paramount importance in an aircraft and engineers optimize it to be as light as possible. Aviation industry uses 400 Hz power supply in the aircraft to reduce the size and weight of electrical components especially electrical motors used in the aircraft.
The transmission losses don’t carry a considerable effect in aircrafts case because the distance between power generation i.e. jet engines and point of use is not so great. Since every aircraft has to carry its own weight before carrying weight of passengers and cargo, each kilogram you reduce on its own components adds to the kilograms you can add for passengers and cargo to generate greater revenue. By using a higher electrical frequency, aircrafts are made lighter and more efficient.
History of 400 Hz Standardization & Aircraft Ground Power Units (AGPU)
Historically, an aircraft was an all-mechanical machine with no requirement for onboard electrical power supply. The earliest requirement of electrical power in aircrafts arose for starting the main engines.
Consequently, in the first world war (1914-1918), wind-driven generators became a standard in military aircrafts to power the ignition system of the engine as well as wireless telegraphy.
As aircraft technology improved, aerodynamics of the aircraft did not allow the use of wind-driven generators because they relied on receiving air from the landing gear and the landing gear had to be made retractable. Therefore, onboard power generation shifted towards engine driven generators.
The earliest engine driven generators worked on 6 Volt DC and 12 Volt DC power systems. However, as more and more technologies integrated into the aircraft such as lighting and heating systems, more power was required from the generators that shifted them to 28 Volt DC system.
In 1940s and 1950s, 28 Volt DC engine driven generators were being widely used for onboard power generation. However, electrical power demands kept raising due to ever increasing features and services on the aircraft.
Greater power requirement translated into shifting towards AC power generation because high voltage DC power generation onboard was not a viable option in view of safety considerations.
AC generators found more and more use in aircrafts in 1960s as they could generate greater power onboard at high voltages resulting in lower cabling weight.
However, it also brought complexities associated with AC power including the question of choosing the right frequency. Choice of frequency depended primarily upon the maximum speed generators could run at as well as the impact on associated devices.
While different manufacturers around the world used different electrical frequencies ranging from 60Hz to 800 Hz, the first step towards standardization of 400 Hz electrical frequency was taken by US Air Force when it made 115/200 Volt AC power supply at 400 Hz mandatory in 1959 in military standard no. MIL-STD-704.
The reason behind the selection of 400 Hz was the same as discussed earlier i.e. compact design of devices using electrical power to carry out different functions in the aircraft and the maintainable generator speeds required to produce 400 Hz power.
Aircraft Ground Power Units (AGPU) were in use even when the aircrafts used 28 Volt DC power systems before the whole 400 Hz transition.
For example, Axel Ackerman – a Danish entrepreneur and inventor developed 28 Volt DC rectifier unit for smaller aircrafts in 1953 by his company AXA Power. These units were exported to Scandinavia and Netherlands the following years.
The same company developed 400 Hz aircraft ground power unit (AGPU) for larger aircrafts in 1985. Similarly, the famous Hobart brand had been producing aircraft ground power units since 1946. By 1990s, aircraft ground power units were being mass produced for meeting commercial aircraft power demands.
Both of the above mentioned companies i.e. AXA Power and Hobart GSE are now owned by ITW GSE.
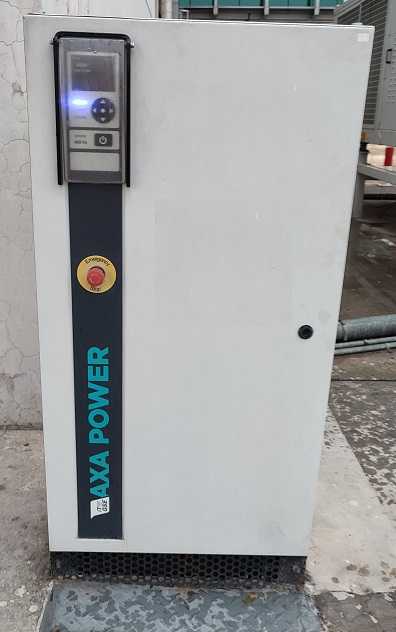
Basic Operation of Aircraft Ground Power Unit (AGPU)
In layman terms, Aircraft Ground Power Unit is a box with a cable to plug into the aircraft. What happens inside the box will be explained in detail shortly. For now, just consider that this box produces power supply at 400 Hz electrical frequency and 115 Volt (3-Phase).
After an aircraft reaches and stops at the aircraft stand, pilots generally keep at least one jet engine on to power all of its electrical systems. AGPU is connected to the aircraft before the pilot turns off the engine so that no break in electrical power is experienced in the aircraft.
The sequence is such that the AGPU operator conducts a pre-flight inspection of AGPU before arrival of flight to make sure it is in serviceable condition with no errors or faults that could create problem at the actual arrival.
After parking and engaging chokes on the aircraft wheels, ground engineer gives a go ahead to the AGPU operator to approach the aircraft. The operator extracts and lays the AGPU cable on ground in a way to avoid the cable from getting overrun by any vehicle on the aircraft stand.
The AGPU receptacle is always located near the nose of the aircraft. For narrow body aircrafts like the Airbus A320 and Boeing 737, the height of the AGPU receptacle is approachable without the need for any aid. For example, height of AGPU receptacle of Airbus A320 is 2.0m (6.56 ft.) above ground. Similarly, on Boeing 737 is 1.9m (6.23 ft.).
For above aircrafts, the operator simply opens up the AGPU receptacle cover and hooks up a strain relief strap whose function is to prevent the AGPU plug from disconnecting and falling to the ground due to its own weight.
The operator then plugs in the AGPU adapter and checks for a yellow LED on adaptor to turn on that gives indication to the operator that the adapter is properly inserted and the aircraft is ready to receive power. It is called the interlocking LED.
Once the Yellow/interlocking LED is lit, the operator presses the ON button on the adapter to turn the power on. The AGPU plug adapter has an LED than turns green when a successful electrical connection is established. AGPU operation is complete at this moment.
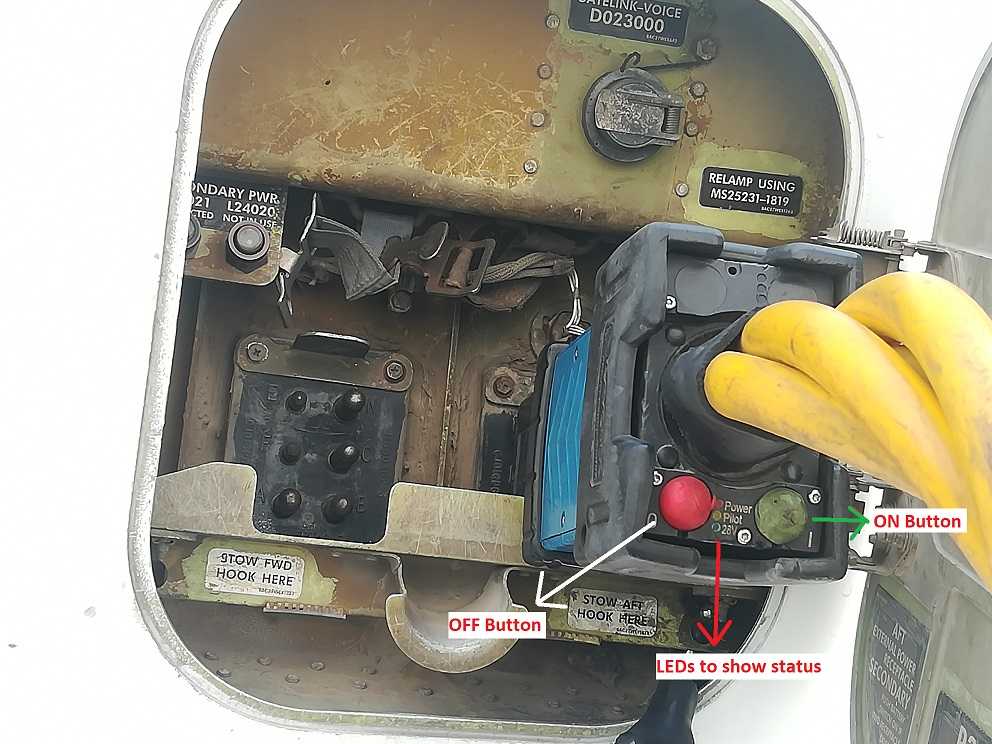
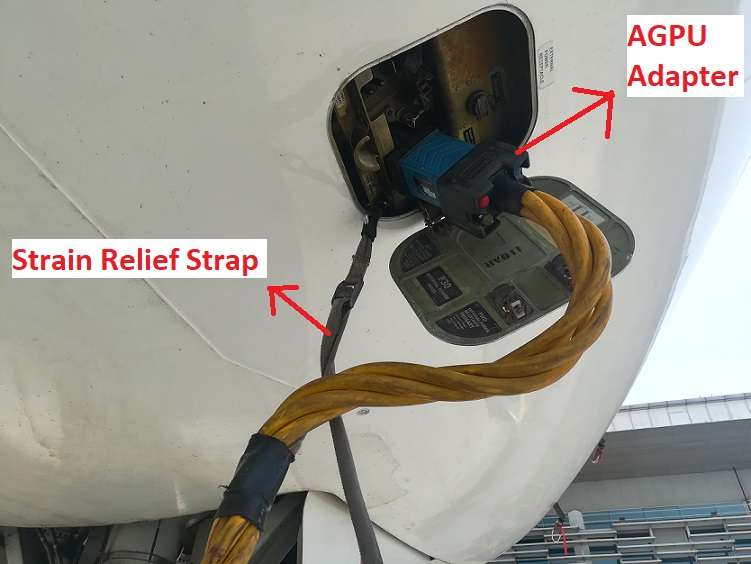
On wide body aircrafts such as Boeing 777 and Airbus A350, height of the AGPU receptacle is not reachable without an external aid. For example, AGPU receptacle on Boeing 777-300 are located 2.8m (9 ft.) above ground. Similarly, the AGPU receptacle on Airbus A350-900 is located 2.58m (8.46 ft.) above ground.
Moreover, wide body aircrafts have two AGPU receptacles to plug in two adapters since they need more power. We will discuss this point in more detail shortly.
For above aircrafts, a team of two AGPU operators is generally deployed. They also bring a 2-3 ft. ladder on the aircraft stand to reach the AGPU receptacle of these larger aircrafts and plug in the adapter. All of the other steps are same as already discussed above for narrow body aircrafts.
At the time of departure, the same sequence is reversed where AGPU operators turn the OFF button on the adapter, unhook the strain relief strap and remove the AGPU cable to clear the path for aircraft pushback.
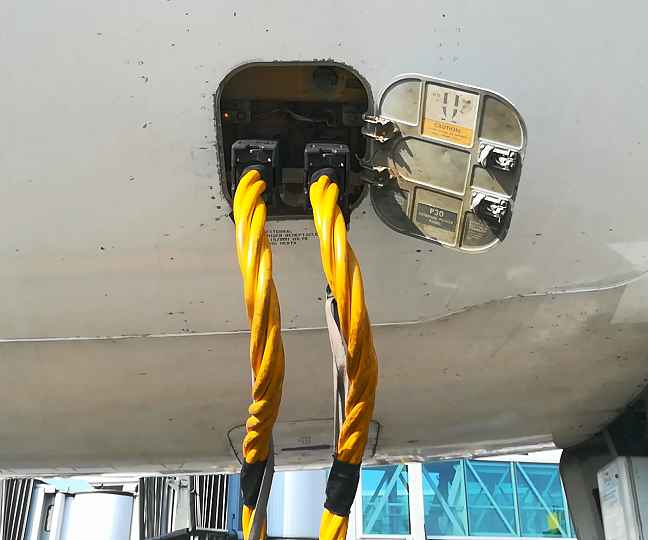
Types of AGPU Based on Mobility
Remember we assumed AGPU to be a box?
There are three types of aircraft ground power units with respect to place of installation of the unit and how much mobile are they. These types are,
- Fixed to ground
- Bridge Mounted
- Mobile
Fixed Type Aircraft Ground Power Unit
The Fixed Type Aircraft Ground Power Units are installed on aircraft stand and they cannot change their position. They can only serve the aircrafts that arrive at the stand where they are installed and are not mobile at all.
The output cable from such type of AGPUs is taken near the aircraft receptacle with the help of either a utility pop-up pit system or a cable retriever system.
The type and quantity of these AGPUs to be installed at each aircraft stand is decided at the time of airport planning. The decision is based on maximum size of aircraft for which the aircraft stand is designed for.
For example, an aircraft stand designed for narrow body aircrafts like Airbus A320 and Boeing 737 will have a single AGPU installed at the stand and will generally have a capacity of 90kVA.
On the other hand, if the aircraft stand is designed for supporting wide body aircrafts such as Boeing 777 and Airbus A350, there will be two AGPUs installed on the aircraft stand, each of 90kVA capacity. Why 90kVA is a standard capacity will be discussed later in this article.
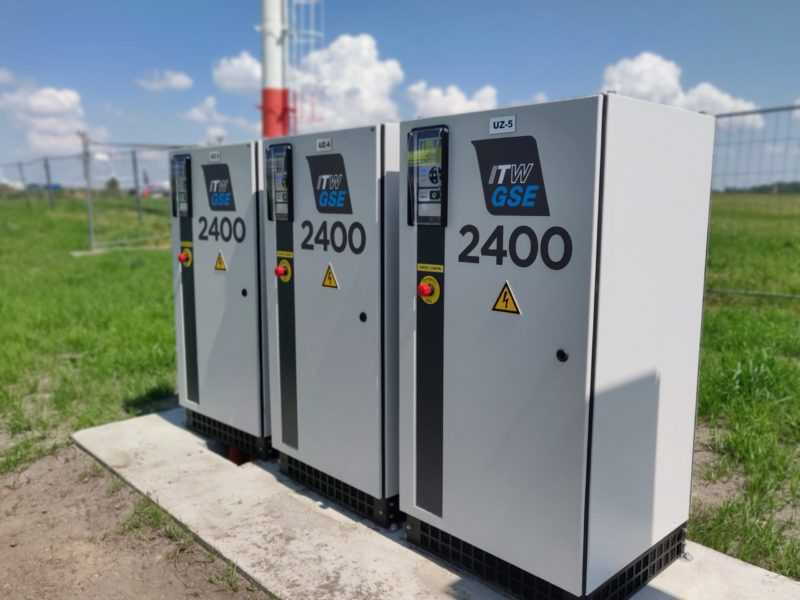
Bridge Mounted AGPU
The second type are Bridge Mounted Aircraft Ground Power Units. They are given that name because they are installed under a passenger boarding bridge (also known an jet bridge).
The mobility of bridge mounted AGPU is also restricted as it cannot be moved to another aircraft stand. It is installed under a jet bridge and as the jet bridge moves closer to the aircraft, it moves with the bridge.
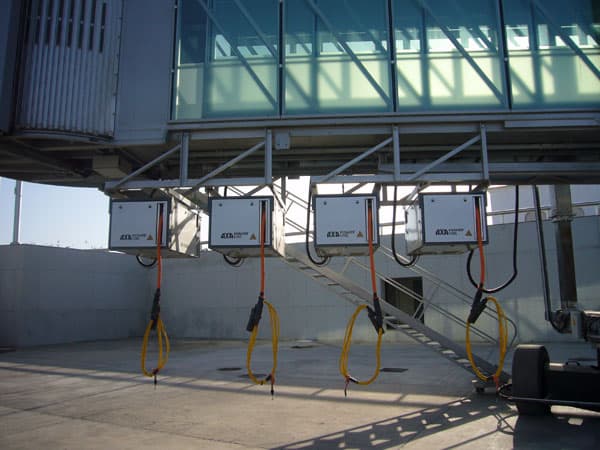
Mobile AGPU
The third type is Mobile Aircraft Ground Power Unit. It is simply AGPU on wheels. They are built upon a cart that is towed with the help of a towing tractor and taken to the aircraft sand where they are required.
As the name suggests, their mobility allows greater flexibility for the airport operations team to tow the unit wherever required and serve different aircrafts parking on different aircraft stands throughout the day.
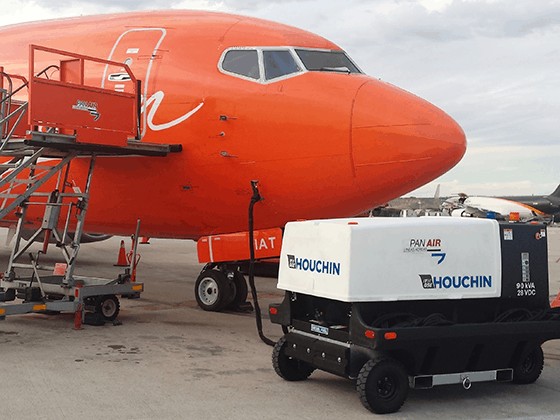
Comparison of AGPU Types – How to choose?
Now that we understand the different types of AGPUs, let us explain why these types exist at all as well as how a particular type of AGPU is selected at an airport.
Mobile AGPU is the conventional type of AGPU that has been used traditionally at airports around the world. These AGPUs allow the greatest flexibility in airport ground support operations because they can be towed to any aircraft stand.
Moreover, they don’t need a lengthy cable because they can be parked close to an aircraft’s GPU receptacle.
However, movement of these units creates traffic on airside that increases risk of accidents on apron. Another drawback is cost of fuel consumption for towing these units from one place to another with he help of towing tractors.
Every airport weighs the advantages and disadvantages of mobile AGPUs to decide if they need to keep such AGPUs in their inventory. If yes, how many are needed?
Generally, airports do keep a certain number of mobile AGPUs in their inventory and use them for,
- Supplying power to aircrafts parked at remote stands (an aircraft stand where there is no jet bridge).
- Using them as contingency for those aircraft stands where fixed type AGPU has become faulty.
- Use on airports or aircraft stands where aircraft traffic is not enough to justify installation of a dedicated fixed type AGPU. For example, if an airport does not receive much traffic of cargo aircrafts, it is not cost effective to install fixed type AGPUs on cargo stands of the airport as they would remain under-utilized. A set of mobile AGPUs will offer a cost effective solution.
Fixed type aircraft ground power unit is the right solution for aircraft stands and airports that receive a lot of traffic throughout the day. They eliminate the need for towing a mobile AGPU and offer a ready solution to all aircrafts that arrive at the bay.
They simplify ground support operations by removing the hassle of planning movement of mobile AGPUs from one aircraft stand to another by a ramp supervisor. Moreover, by eliminating movement, they provide a twofold advantage. They reduce risk of accidents on the ramp as well as reduce cost of operation by saving fuel consumed by towing tractors.
Bridge mounted Aircraft Ground Power Units combine two advantages of fixed type and mobile AGPUs. Like fixed AGPUs, they offer a ready solution at the aircraft stand and like mobile AGPUs, they get near the aircraft to reduce the cable length that runs from the AGPU to the aircraft AGPU receptacle.
Apart from above, a characteristic advantage of these AGPUs is that they don’t occupy any space on the aircraft stand. Mounted under the jet bridge, they have zero foot print on ground.
However, the main problem of these units is with their maintenance friendliness. Since they are mounted at a certain height, it is not as easy to inspect and service these units like it is for a fixed AGPU or a mobile AGPU.
Moreover, bridge mounted AGPUs cannot be serviced or checked for technical faults when the jet bridge is engaged to an aircraft unless you unmount these units – a cumbersome task in itself.
Fixed AGPUs and Mobile AGPUs offer a lot of convenience to maintenance teams in this regard because you can undertake maintenance tasks on these units irrespective of flight operation. They are located away from the aircraft and you can open these units up without disturbing ramp activities.
In short, when airport management is considering procurement of aircraft ground power units for the airport, they have to look at multiple factors related to operation of the airport as well as maintainability of the machines before reaching a final decision.
Types of AGPU Based on Power Source
So far, we have discussed the types of aircraft ground power units based on mobility and their place of installation. We repeatedly asked you to consider AGPU just as a box.
Let us now peek inside the box and discuss the types of aircraft ground power units with respect to the type of power source they work with.
There are three main types of aircraft ground power units based on power sources,
- Fuel or Engine Powered AGPU
- Solid State AGPU
- Battery Powered AGPU
They are fairly simple to understand just with their names.
A Fuel Powered Aircraft Ground Power Unit is like a diesel generator that produces power at 400 Hz and 115 Volt (3-Phase) with the help of a generator run by a diesel engine. It is very similar to a mobile generator in its design with the difference of output power specifications.
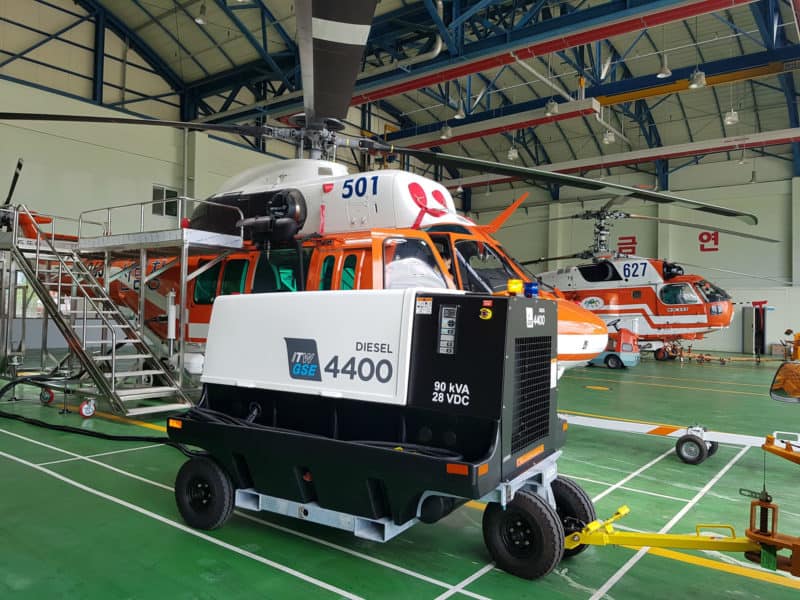
A Solid State Aircraft Ground Power Unit is basically a solid state converter that does not generate electricity of its own. It takes the airport’s utility power supply as an input and converts the 50/60 Hz frequency to 400 Hz as well as the utility volts to 115 Volts needed by the aircraft.
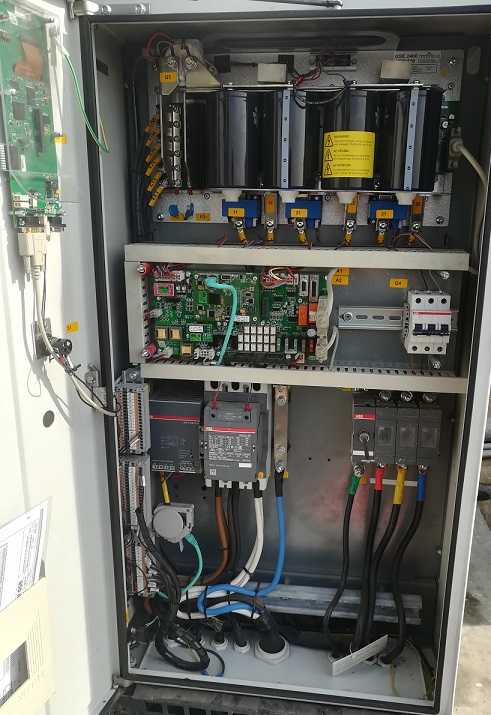
Battery Powered Aircraft Ground Power Units are the equivalents of electric cars in AGPU industry. They are charged by the airport’s utility power supply and store the charge in their batteries. They produce and supply the 115 V and 400 Hz electric power to aircrafts until their batteries are drained and a recharge is required.
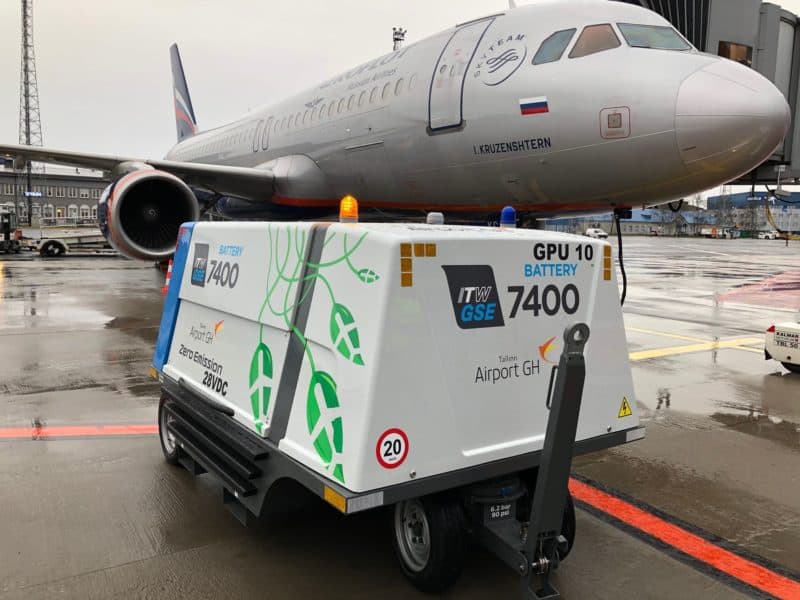
How to Choose AGPU Power Source?
Fuel powered AGPUs generally come in Mobile AGPU configuration because it fits well with their flexibility as you can use them anywhere as long as you have fuel in the tank. However, due to environmental concerns and the emphasis on green energy, manufacturers are now developing mobile AGPUs that run on utility power supply as well as models that run on batteries.
The drawback of fuel powered AGPUs includes their noise level, maintenance and emissions. They are powered by internal combustion engine – generally diesel engine that needs maintenance just like any engine does.
They generate more noise at the ramp thereby adding to an already noisy environment creating more discomfort for the staff working at the ramp. Moreover, like any car, they also generate carbon dioxide emissions that are not environmentally friendly.
Utility powered AGPUs come in both fixed and mobile configurations. These AGPUs simply covert the 50 Hz 110/220 volts of utility power supply into 400 Hz 115V aircraft power supply. Due to no moving parts, these AGPUs have negligible noise as well as less maintenance.
Utility powered mobile AGPUs require ground power sockets having utility power supply at aircraft stands. One cable is plugged inside the utility power supply and the other cable is plugged into the aircraft.
Utility powered fixed AGPUs are installed on the aircraft stands where utility power is hardwired at their inputs and as described earlier, their output is taken near the aircraft AGPU receptacle by means of a utility pop-up pit system or cable retriever system.
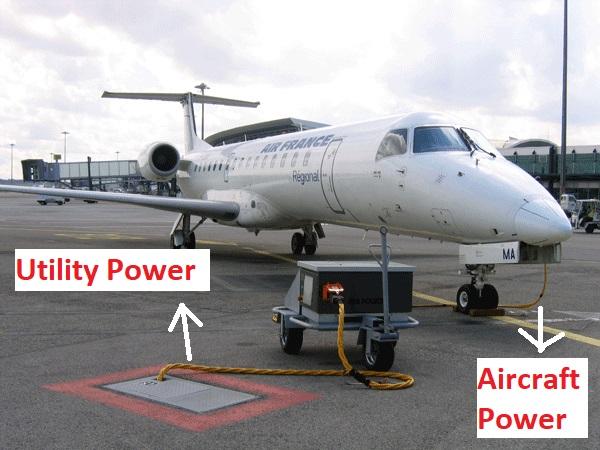
Battery powered AGPUs are predominantly offered in the form of mobile AGPUs because installing a battery on a fixed AGPU doesn’t have much advantage. Batteries have been introduced to AGPUs for providing a mobile emission free solution to ramp operation.
These AGPUs combine the mobility of conventional fuel powered mobile AGPUs with ergonomics and environmental friendliness of utility powered AGPUs.
They don’t need any ground power socket due to which they remain as flexible as fuel powered units as their mobility is not restricted by location of ground power socket. Moreover, they don’t generate the noise and emissions generated by fuel powered AGPUs which makes them environmentally friendly as well as reducing overall noise level at the busy noisy ramp. These units generally charge from the standard 50/60 Hz sockets.
On the downside, battery powered AGPUs have a limited time in which they can offer their services. Their usage duration is dependent upon the capacity of their battery bank. Units like Model 7400 eGPU from ITW GSE come with battery banks that can serve 10-12 flights of narrow body aircrafts (manufacturer’s claim) in a single charge.
However, this limitation has been overcome by manufacturers by introducing the ability of supplying power and charging at the same time. It allows the AGPU to be charged if its battery is low while plugged into the aircraft if a power socket is available at the aircraft stand.
The same problem is also dealt with adding an internal combustion engine in the unit as a contingency to kick in if battery level is low at the time when AGPU is needed.
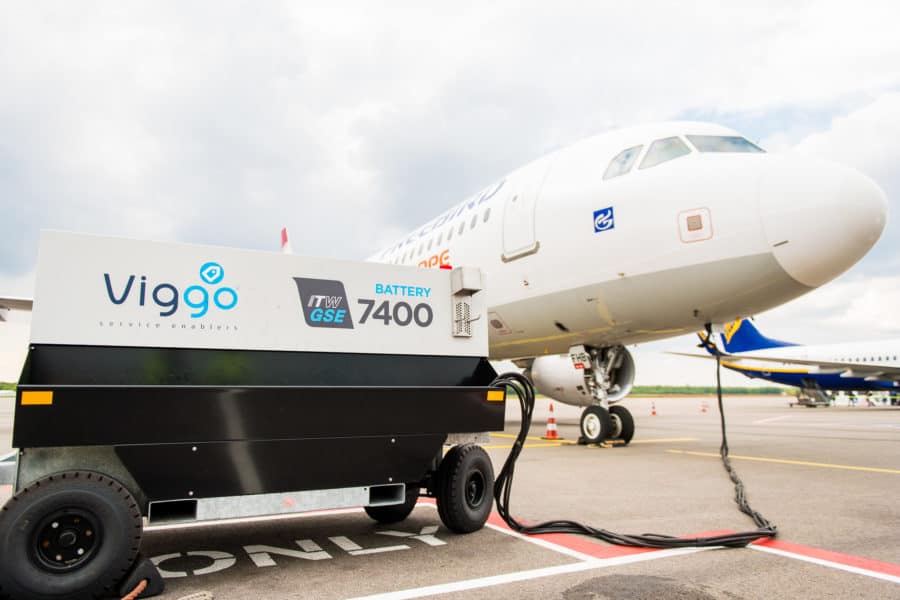
At all modern airports, utility powered AGPUs are generally the preferred choice due to less noise, reduced maintenance and environmental preservation factor. Being relatively new, battery powered AGPUs have not become common and might take some time before being established as a competent solution.
Mobile AGPUs on the other hand are generally fuel powered as it has remained the predominant AGPU configuration throughout history. However, more and more airports around the world are converting to utility powered AGPUs due to environmental regulations and concerns.
So this was it from our side. We hope we have explained all you needed to know about aircraft ground power units. Nonetheless, if you think we have missed something, do let us know. If you liked our article, don’t forget to share it with people sharing the same interest as us and you.
If you are interested in obtaining a base level knowledge about all the different types of aircraft ground support equipment and operations, Check out this 3 Hour video based course on Udemy that explains each of nearly 20 different aircraft ground support activities and equipment.