In this article, we are going to explain utility pit systems including 400 Hz Ground Power Pit Systems and Preconditioned Air (PCA) Pit Systems. These pit systems are used at aprons and hangers on an airport.
A utility pit system is simply an assembly of underground components that act as an intermediate setup to connect source of a utility, such as 400 Hz ground power or Preconditioned Air, to the aircraft.
When the above referred utilities are not required, the pit system will store the components underground. When the utilities are needed, the pit system gives access to extractable cables, hoses or pipes from beneath floor level for making connections with the aircraft.
Conventional GSE Operation (Without Pit System)
In order to understand the concept of a utility pit system and what solution it offers to airport operations, it is necessary that you review the different ground support facilities provided to the aircraft when it is on ground.
These facilities include 400 Hz Ground Power, Preconditioned Air, Potable Water, High Pressure Air for Air Start and Lavatory Drainage. The conventional methods of providing these facilities to on-ground aircrafts hold the problem statement in response to which pit systems have been developed by different aviation equipment manufacturers around the world.
For each of the above-mentioned facilities, there is a separate ground support equipment generally in the form of a machine assembled over a cart or truck chassis (or a fixed under the jet bridge configuration).
These machines and vehicles are positioned close to the aircraft while cables, pipes or hoses stretch from each machine to the respective ground support connection under aircraft fuselage.
400 Hz Ground Power, for example, will be provided either by a mobile AGPU or bridge mounted AGPU. Nonetheless, Ground cable will have to be extended from the AGPU itself to the aircraft electrical power receptacle.
Similarly, a Preconditioned Air (PCA) unit will also provide preconditioned air through a hose that will extend from the preconditioned air unit itself to the aircraft.
When these facilities are engaged, the hoses, pipes and cables create a bit of clutter on the aircraft stand. Moreover, it takes time for correct positioning of machines and vehicles around the aircraft and extraction and laying of the hoses, pipes or cables safely on ground before making the final connection.
In the case of Preconditioned Air, for example, the operator has to first spread the PCA hose on ground for its complete length and then make the connection with the aircraft. It is because unlike a 400 Hz ground cable where you can only pull that length of the cable which is sufficient to reach aircraft’s electrical power receptacle, a PCA hose has to be unrolled its complete length and laid on ground even if the aircraft’s PCA receptacle is quite near to the PCA unit. Since the hose carries air pressure, a rolled hose will not remain rolled when PCA unit creates the air flow that forcefully inflates the hose.
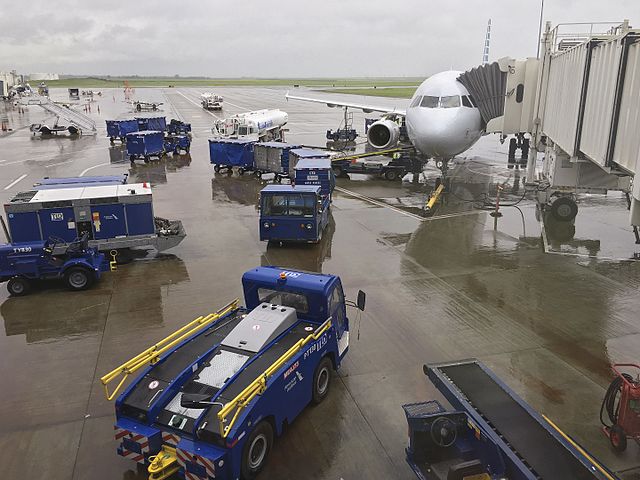
How Utility Pit Systems Solve the Problem
Now that we understand the problem, we can look at the solution offered by Pit Systems. Utility pit systems allow the Preconditioned Air, 400 Hz Ground Power or any similar facility to be installed on any desired location on the aircraft stand away from the aircraft.
The output of these facilities, that in the case of a PCA unit is Preconditioned air carried by a hose, and in the case of an AGPU is electrical power carried by a cable, is transferred to the aircraft parking location by making an underground channel carrying the cable or hose and terminating in a mechanical setup that opens up on ground and gives access to operators to extract the hoses and cables by simply pulling the desired length and easily making connection with the aircraft.
The main advantages offered by pit systems are given as under,
1. With pit systems, it becomes possible to reduce clutter of hoses and connectors on an aircraft stand and keep the working area neat.
2. It also reduces airside traffic by eliminating the need of GSE carts and vehicles such as towing tractors bringing mobile AGPUs or a mobile PCA units to an aircraft stand where the units are kept parked until the time of departure.
3. By reducing traffic, risk of accidents is also reduced. Apart from that, other accidents such as another vehicle or machine running over a ground power cable can also be avoided by removing cables, hoses and connectors from the path of ground crew.
4. Last but not the least, pit systems reduce the time required for engaging and disengaging a facility by providing hoses, cables and pipes close to their ground service connection points of the aircraft. It reduces the connection distance where an operator simply pulls as much cable as needed to reach aircraft’s AGPU receptacle or extracting only that much length of potable water hose as is needed to reach potable water port.
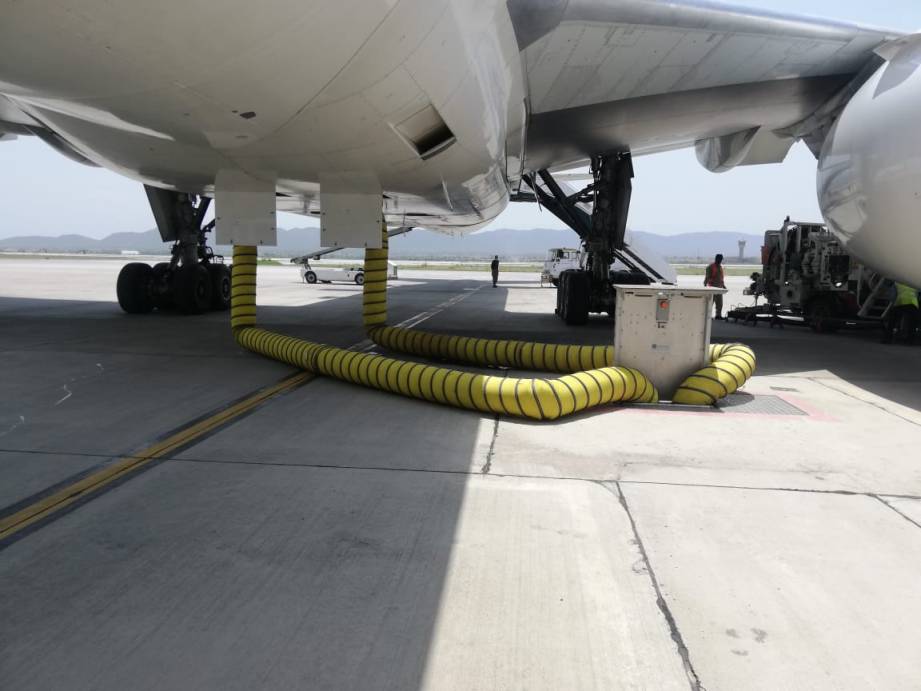
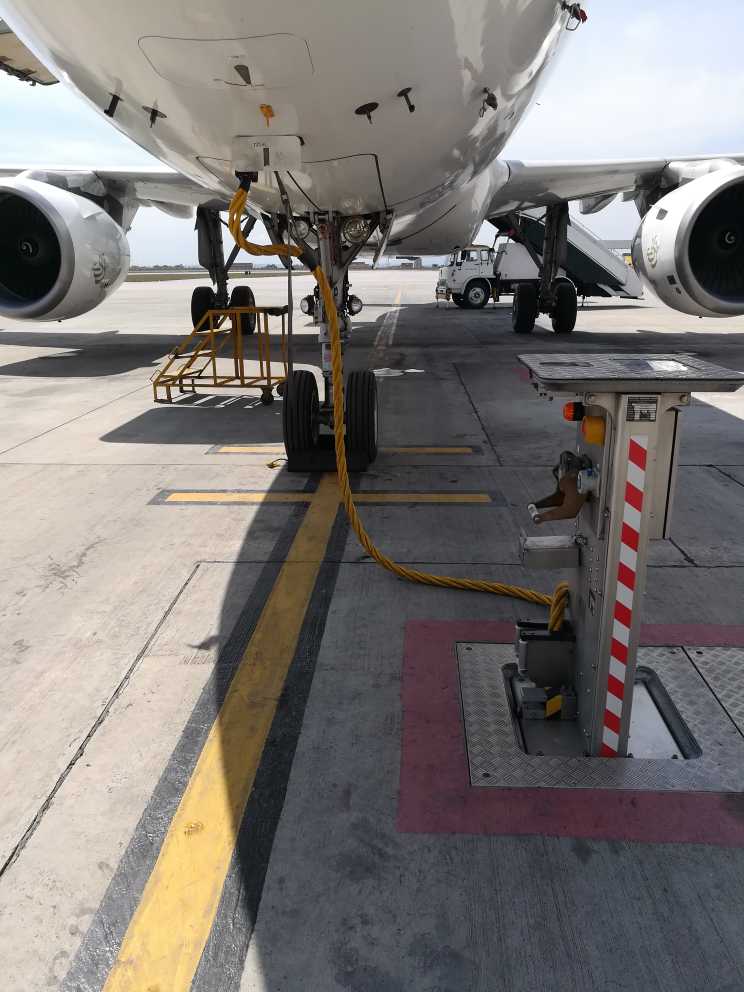
Types of Pit Systems
There are two main types of pit systems,
- Hatch pit system
- Pop-up pit system.
The main difference is that a pop-up pit system allows the operator to pull the connectors from the popup unit from a comfortable height, whereas, in a hatch pit system, connectors have to be pulled from ground level.
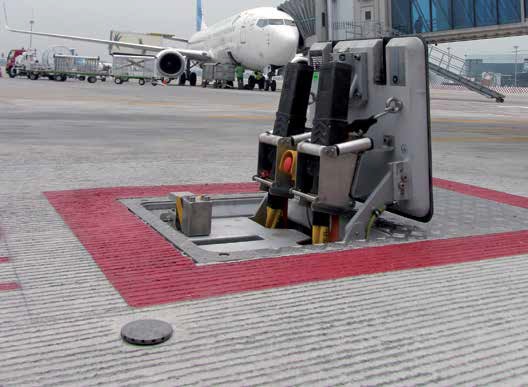
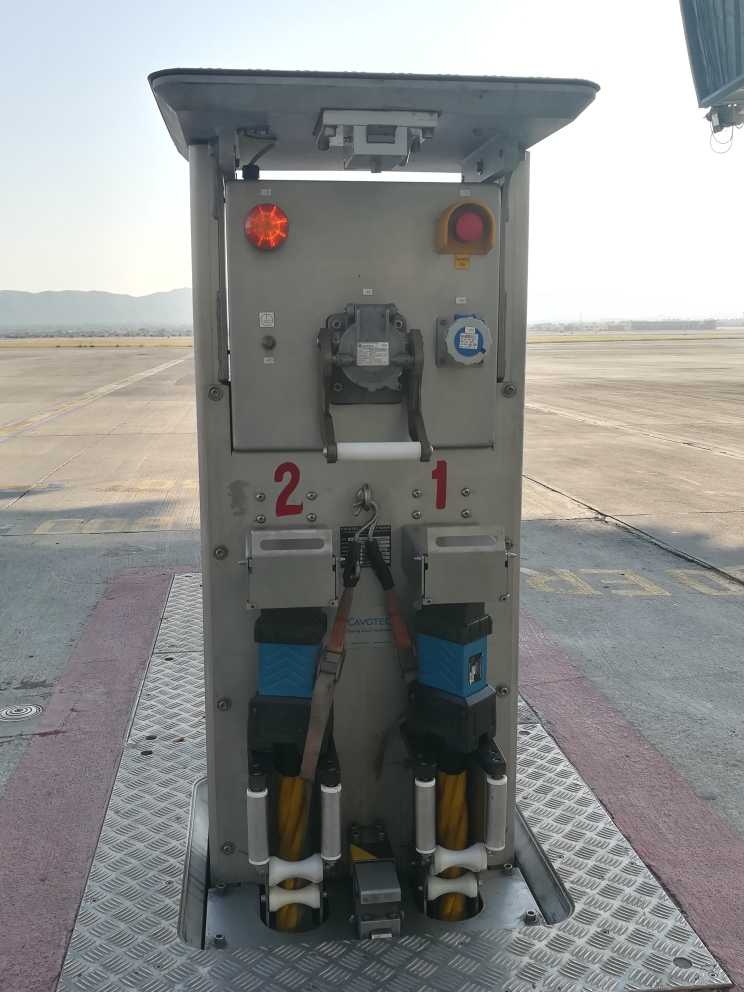
Basic Design of Utility Pit Systems
The basic setup of a Utility Pit System comprises the parent system (for example Preconditioned Air Unit or 400 Hz Ground Power Unit) installed on a fixed location at aircraft stand with an underground channel leading from the parent equipment to an underground pit in the form of a room.
The underground channel carries the 400 Hz cable or PCA hose from the parent equipment to the Utility Pit. The pit system comprises the following,
- Mechanical Assembly
- Electronic Sensors
- Dewatering Pump
- Electrical Enclosure
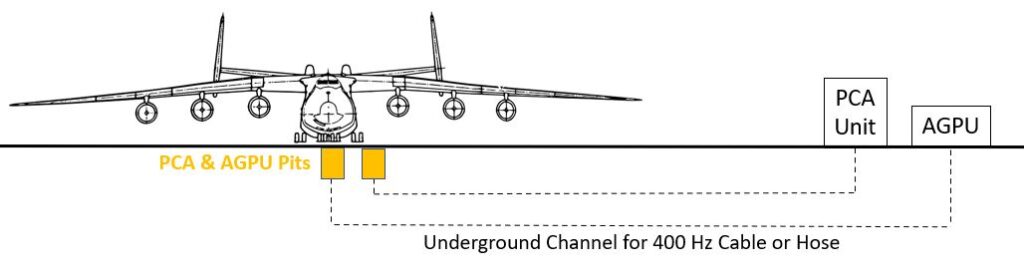
The Mechanical Assembly comprises the necessary support structure needed to house the hose or cable. For example, in Preconditioned Air Pop-up Type pit systems, there is a sheet metal assembly to ensure smooth retrieval of PCA hose stored in collapsed form inside the same assembly.
Similarly, the 400 Hz Ground Power Cable rests on a support structure from where only that length is extracted by operators as needed to make connection with the aircraft.
For potable water, a hose reel is installed inside the pit system that unrolls only that length of the hose as is necessary to connect with the aircraft’s potable water port.
Electronic Sensors mainly consist of such sensors and switches that communicate the status of pit especially if it is properly closed or not. These sensors are necessary for establishing electronic communication with other equipment installed on aircraft stand (especially the parent equipment of the pit system) for safety interlocks.
For example, a limit switch will give feedback signal to 400 Hz AGPU about whether or not the pit system is closed. If the pit system is not open, 400 Hz power will not activate even if the operator gives ON command from the main unit.
A Dewatering Pump is necessary for preventing flooding of the pit in case of rain. Since pit systems are underground, it is imperative that they get filled with rainwater that poses a serious safety and longevity threat to the pit system because water can not only cause short circuiting but also cause corrosion of pit’s mechanical components adversely affecting its service life.
The Electrical Enclosure consists of all the electrical connections inside pit system. These include the connections of the electronic sensors and switches installed inside the pit systems that communicate with the parent equipment for safety interlocks as well as the connections for powering up lights installed to illuminate the pit and dewatering pump.
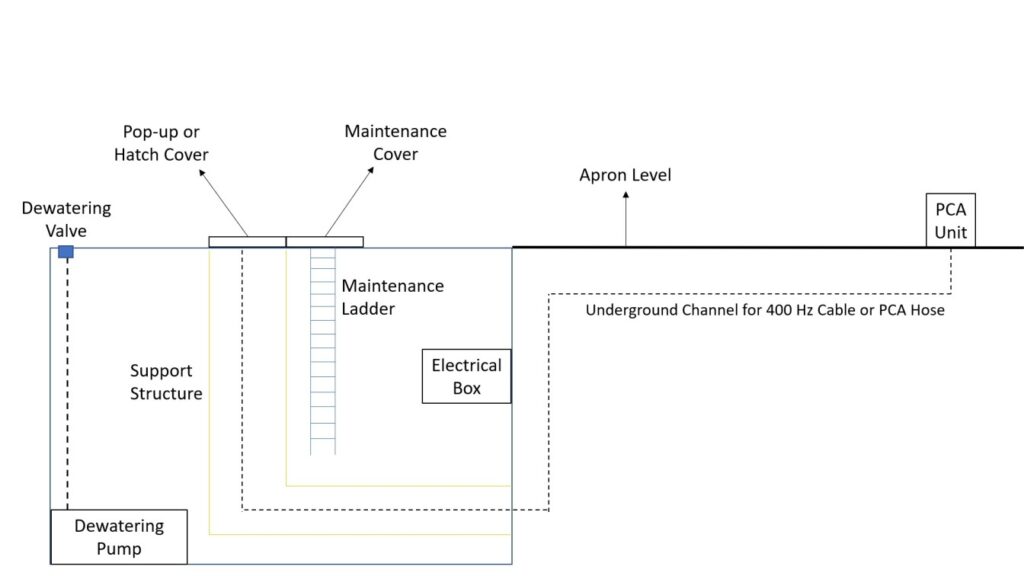
Utilities for which Pit Systems are used at Airports
Preconditioned Air and 400 Hz Ground Power are the most common utilities for which pit systems are used. However, pit systems are also available for many other utilities such as potable water that eliminates need for a potable water truck; compressed air that eliminates the need of an Air Start Unit and sewage that eliminates the need of lavatory service equipment.
Safety, Longevity & Ergonomic Requirements of Pit Systems
There are some important considerations that go into the design of pit systems including,
1. Pit systems are required to have water ingress protection. Since the pit system houses all of its components underground, it is very easy for rainwater to fill the pit drowning its components which can be a critical safety issue especially in case of 400 Hz ground power pit systems where there is risk of short circuiting. For that purpose, pit systems ground covers are designed to offer maximum protection by using rubber seals for waterproofing. Additionally, an underground de-watering pump is installed inside the pit that automatically turns on if it senses (with the help of a float sensor) that the pit is getting filled with water.
2. Pit systems are required to have good corrosion protection to allow it to keep its structural integrity over its life. If the mechanical components of pit system catch rust, they can create hindrance in opening and closing of pit covers.
3. Pit systems are required to have good dust protection by designing its ground level covers with minimum tolerances.
4. Pit systems installed in extremely cold areas have icing protection to prevent the covers from getting stuck due to ice.
5. Pit systems are required to be ergonomically designed so that they don’t create abnormal stress in lower back causing health problems in operators. For that, pit cover needs to be very easy to open. It requires an efficient mechanical setup that is well designed as well as well maintained to keep the opening and closing of pits smooth.
6. Pit Systems are required to be designed strong enough to withstand heavy duty vehicles (such as towing tractor or even the aircraft itself) to run over them without causing structural damage to the pit system.
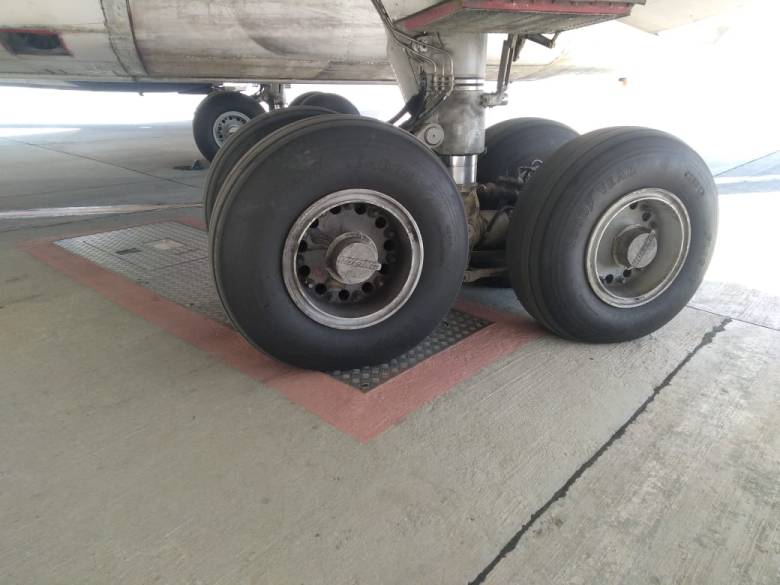
7. Pit Systems have electronic interlocks in place with the parent equipment. For example, a Preconditioned Air unit will not turn on if the pit system is closed. Similarly, 400 Hz Ground Power Unit will not turn on if pit system is closed. Such electronic safeties are setup by installing sensors and switches inside pits that give feedback to the parent equipment i.e. Preconditioned Air unit or 400 Hz Ground Power unit to prevent accidental startups of these equipment inside closed pits.
Utility Pit Systems Considerations in Airport Development
At the time of planning and development of airports, the decision regarding whether to incorporate utility pit systems in airport design requires considering the cost effectiveness factor as well as operational constraints as explained below.
Cost Effectiveness of Utility Pit Systems
Since Pit Systems require considerable civil work, the cost of developing utility pits is much greater than not using them and going on with the conventional means of GSE operation (including carts and vehicle mounted GSE).
Therefore, airport consultants have to deliberate on the cost effectiveness factor and weight the benefits achieved by pit systems against the capital investment that goes into their development. Pit systems are effective only for very busy airports where considerable efficiency gains and risk mitigation is achieved by cutting ramp traffic and constant movement of GSE carts and vehicles on airside. If the problem doesn’t exist, it is not worth investing in a sophisticated solution.
Moreover, Utility Pits bring a lifetime maintenance cost with them as they are made up of several electrical and mechanical components that are required to be maintained over the service life of pits. These costs include the cost of spare parts, consumables and manpower needed to carry out preventive and corrective maintenance of pit systems.
Operational Constraints of Utility Pit Systems
Apart from above cost related factors, Utility Pits also have some operational constraints. Maintenance on pit systems cannot be carried out without interrupting flight operation on the aircraft stand. That is so because pit systems are located close to the aircraft centerline and aircraft docking procedures cannot be carried out while pit system is opened for maintenance.
Owing to reasons given above, maintenance team are left with little flexibility to carry out maintenance on pit systems as they have to fit maintenance activities in the empty time slots of an aircraft stand i.e. when no flights are planned on it. Such constraints are not available with cart mounted or vehicle mounted equipment as they can be taken to a workshop for maintenance whenever needed with a substitute given in operations.
Similarly, there can be occasions where a mechanical fault in Pit System prevents it from properly opening and closing that has the potential of delaying flight departure (if for example the pit system is unable to be closed at the time of pushback of the aircraft). Such incidents can be prevented by proper inspection before flight arrival and by ensuring proper preventive maintenance.
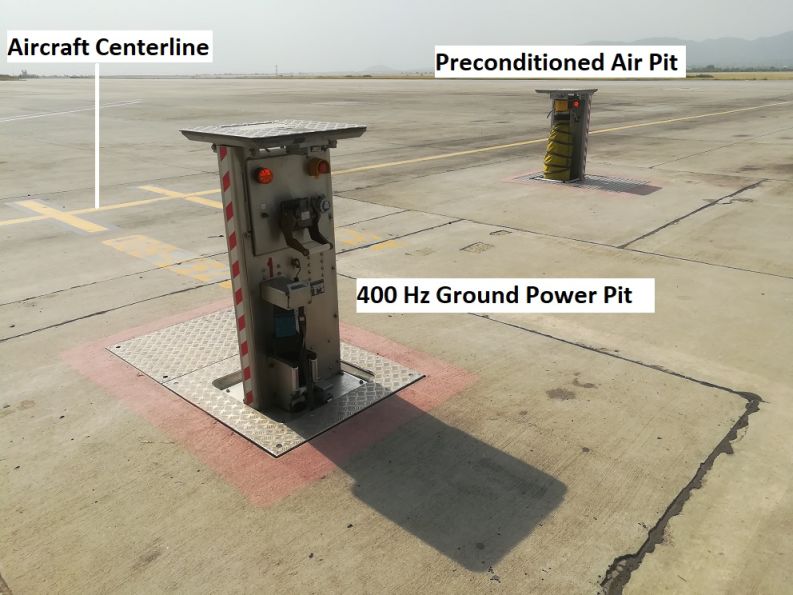
So this is it from our side. If you liked the information we have presented, please do share it with likeminded people so our efforts could reach where most benefit can be derived from them.
If you are interested in obtaining a base level knowledge about all the different types of aircraft ground support equipment and operations, Check out this 3 Hour video based course on Udemy that explains each of nearly 20 different aircraft ground support activities and equipment.