Aircraft Air Start Unit (ASU) is a ground support equipment used for starting jet engine of the aircraft when the aircraft is getting ready for departure. It is analogous to self-starter motor of an automobile that cranks the engine until the engine is able to sustain itself.
Air start unit (ASU) is an important piece of machinery maintained by all airlines and ground handling agencies at an airport in their Ground Support Equipment (GSE) inventory. The unit is made available at the aircraft stand when the boarding is about to complete and Pilots are getting ready for pushback and subsequent departure.
Basic Operation of Air Start Unit (ASU)
Before explaining the working principle, requirement and specifications of an air start unit, let us first imagine air start unit as a box out of which a hose comes and connects with the aircraft. What happens inside the box will be discussed in detail shortly.
If we look at the sequence of activities that take place between an aircraft landing and take-off, we observe that Jet engines are turned off when the aircraft reaches the aircraft stand and are started at aircraft pushback when the aircraft is ready for departure.
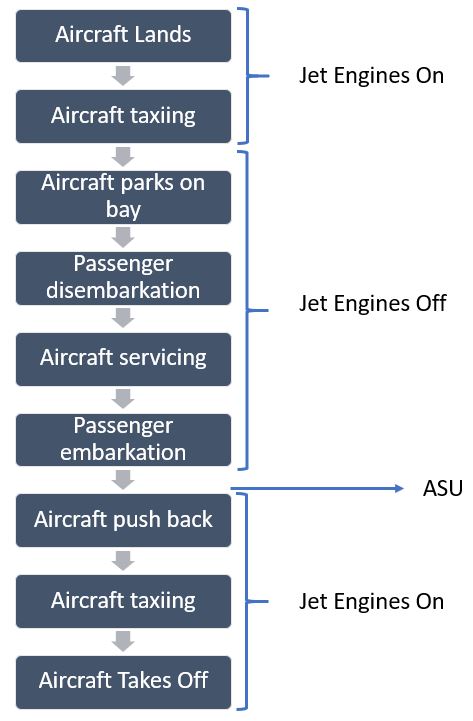
A towing tractor brings air start unit at the aircraft stand well before scheduled departure time. After obtaining go-ahead from the Pilot, air start unit discharge hose is connected with the aircraft high pressure receptacle and the unit is turned on.
The operation of an ASU is very noisy and is noticeable as soon as it starts. In fact, it is the loudest piece of equipment at an aircraft stand after the jet engine. Therefore, staff must not forget to wear hearing protection during air start operation.
As soon as the air start unit is turned on, the jet engine fan, compressor and turbine blades start rotating with the help of power received from air start unit. This rotating speed keeps increasing until Pilot turns the fuel injection system on that produces fire in the combustion chamber. This is the point from where the jet engine can sustain itself and air start unit is disconnected.
Once one jet engine is started (generally engine no. 2 i.e. engine on the right and side of Pilot), the other engine or engines, depending on the type of aircraft, can be started by either using the same air start unit or by using ‘cross bleed’ i.e. compressed air from a running engine flowing to the other engine.
Pilots often start just one of the jet engines with the help of air start unit before pushback operation begins. The other engine is started during taxiing to the runway.
Main Components & Working of Air Start Unit (ASU)
An air start unit is simply an engine driven air compressor. All it does is to suck in air from the atmosphere, pass it through filters to prevent dust and other particles from entering the compressor, and compress the air to raise its pressure. This high-pressure air is then supplied to the jet engine to power up its air starter motor – we’ll explain it shortly.
The engine is generally a diesel engine coupled with an air compressor with the help of a gearbox to drive the compressor at its most efficient speed. The unit has multiple air regulation and control valves for relieving pressure as well as controlling it.
A control panel houses all gauges and meters displaying discharge air pressure and temperature; engine speed; engine coolant temperature; high compressor oil temperature; low compressor oil pressure and buttons for emergency stop; turning the unit on, off or selecting operating modes.
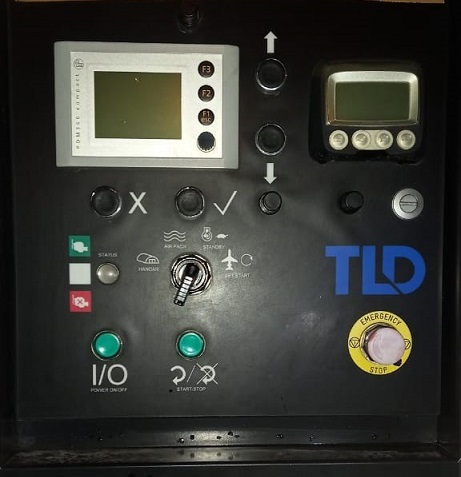
The engine and compressors are all enclosed in a protective covering for rain and weather protection. The complete unit is installed over a cart or over a truck chassis for making it mobile.
The main specifications of an air start unit are its air pressure capacity and its air flow rate. The air pressure in the range of 42 PSI is generally common and services most aircrafts whereas the air flow rate varies from aircraft to aircraft depending on the size of the engine.
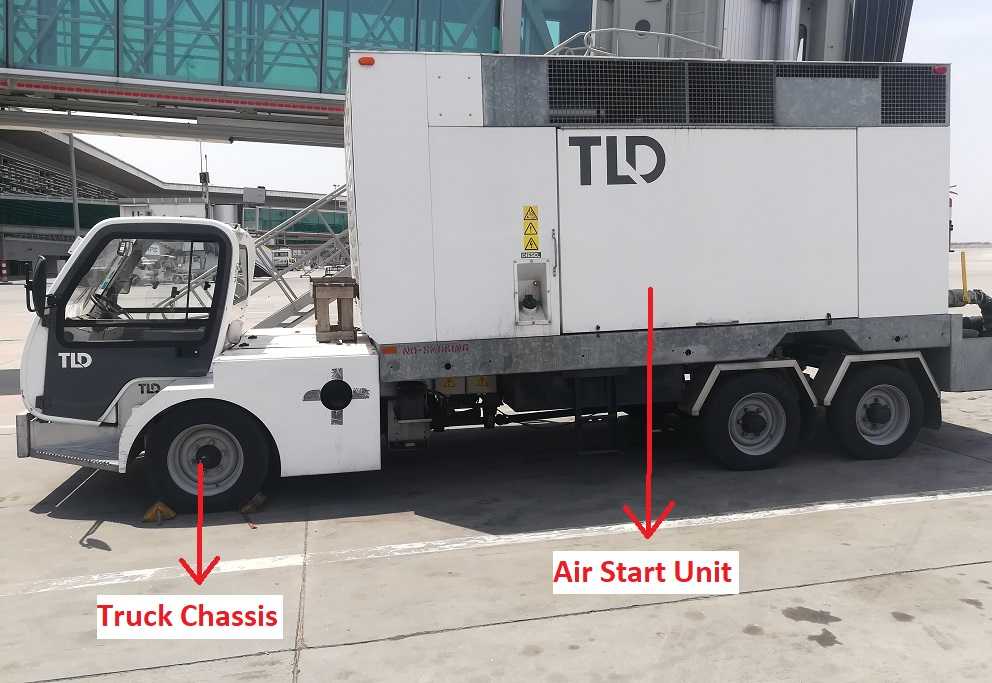
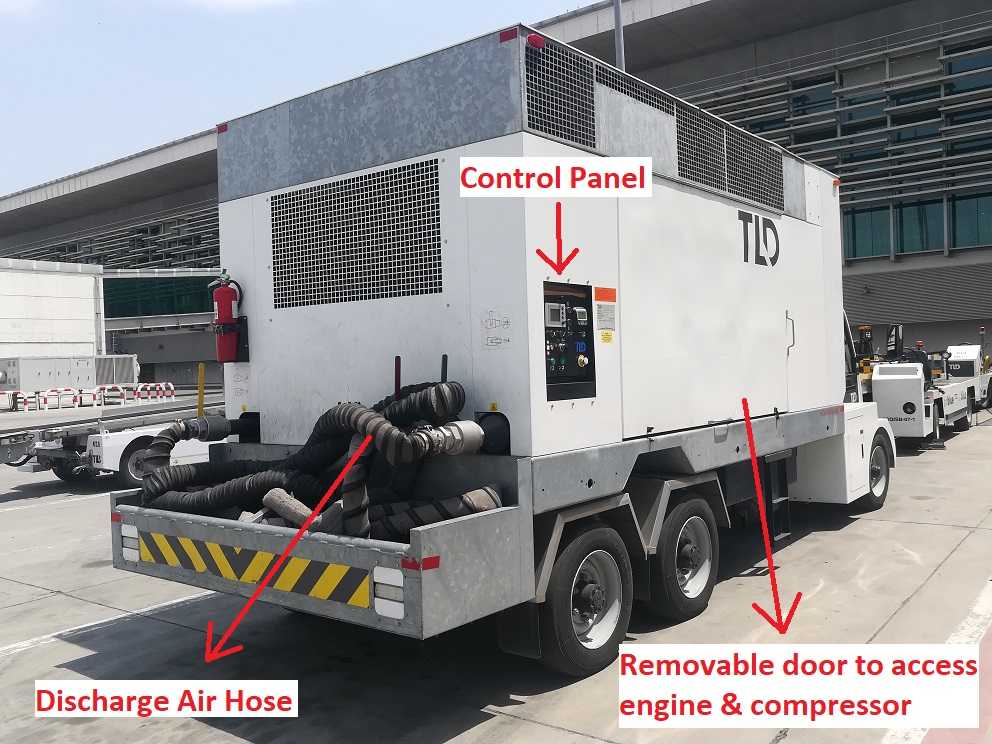
Why an Air Compressor Starts the Jet Engine?
As we have already discussed earlier that aircraft engines starting mechanism is analogous to an automobile engine starting mechanism. Just like an automobile engine is fitted with a self starter motor to start the engine after which you can control its speed with the help of throttle, you can think of ASU as serving the exact same purpose.
However, the most obvious question that arises in any technical mind is how come an air compressor is starting up a jet engine? The self starter motor on an automobile is an electric motor powered by a battery and it makes sense. Isn’t there a motor to start the jet engine just like in our cars? There must be a big motor that could do that.
The simple answer to that intuitive question is, Yes, there is a motor. However, it is not an electric motor powered by a battery. It is a pneumatic motor powered by high pressure air supplied by the air start unit. This air start motor needs compressed air and not electricity to run itself and that is why air start unit is an air compressor.
How Air Start Mechanism Works?
To explain the air start mechanism, let us begin with an explanation of the basic working principle of a jet engine.
A jet engine has a fan, rotary compressor blades and turbine blades all mounted on a common shaft referred to as a spool. When air that has been heated in the combustion chamber passes through the turbine blades, they extract energy and make the spool rotate that makes the fan and compressor blades rotate because they are all mounted on the same shaft.
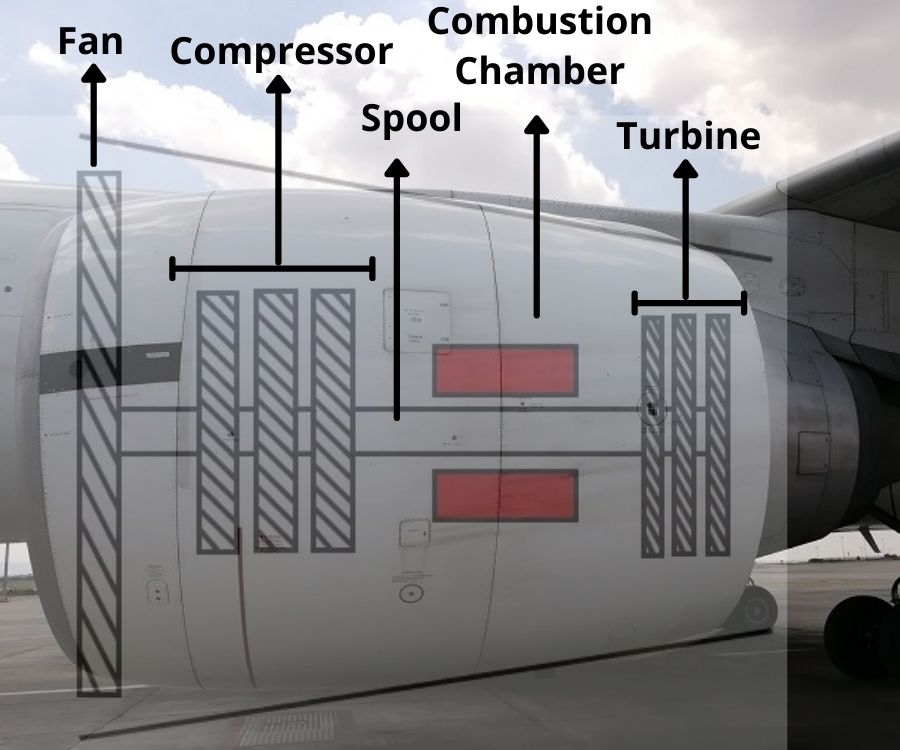
The speed of the spool is controlled with the help of throttle adjusted by pilots in the cockpit. As more and more fuel enters the combustion chamber, turbine speeds up causing the turbofan and compressors mounted on the common spool to speed up drawing more and more air into the combustion chamber and turbines.
The problem is that this whole cycle cannot start itself. To start the cycle you need to get the shaft rotating for some time to generate enough airflow for the combustion chamber to take control and sustain the rotational speed of the jet engine.
This initial rotation is provided by air starter motor that drives the spool with the help of a gearing mechanism. As the motor runs, it runs the spool that runs the turbine, fan and compressor blades.
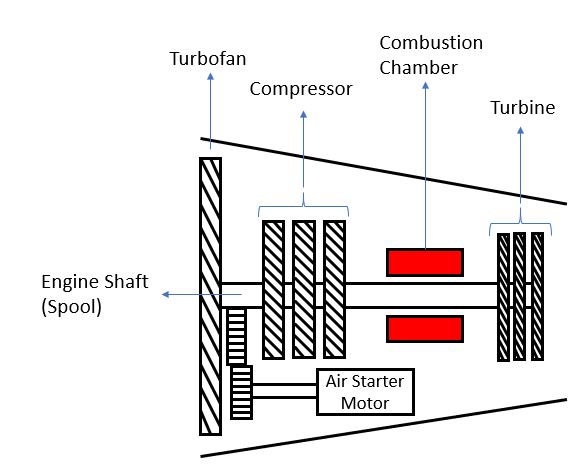
When air start unit is turned on by ground staff, compressed air is supplied to air starter motor. The energy inside this compressed air is converted into rotation by the motor as long as the desired air pressure and air flow are sustained with he help of air start unit.
As soon as the jet engine reaches desired speed, fuel is introduced into the combustion chamber by Pilots that takes over the control of speed from air start unit and ground staff is cleared to shut down and remove the air start unit. Let us discuss the basic engineering design of an air starter motor to develop a deeper understanding of the matter.
Basic Design & Working of Air Starter Motor
The basic design of an air starter motor comprises a turbine, gear mechanism and clutch that engages or releases the motor from the jet engine drive shaft (spool).
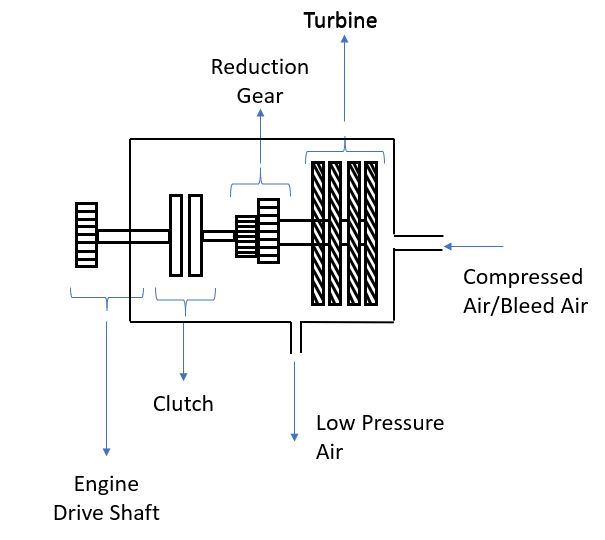
It works when compressed air (at high pressure) is received as its input. This air passes through the turbine and leaves as low pressure air out of the motor. Turbine extracts energy from this pressurized air and makes the motor shaft rotate. Since the motor shaft is coupled with the jet engine’s shaft (or spool), it is rotated as well.
As soon as the fuel is introduced inside the combustion chamber and control of speed is needed to be shifted from the air starter motor to the jet engine itself, the air starter motor clutch is released allowing it to be disconnected from the jet engine’s spool. The air start unit hose is then disconnected.
What if there is no Air Start Unit (ASU)?
While air start unit is an important piece of ground support equipment, it is not that the jet engines cannot start without air start unit. Air start motor needs compressed air to work and an air start unit is not the only source of compressed air.
Another source of compressed air is the Auxiliary Power Unit (APU). It is a mini jet engine located in the tail of an aircraft that is used to power up different systems when the main jet engines are off. It also serves as a source of compressed air that is technically called ‘bleed air’.
Since it is a mini jet engine itself, the APU also has a set of compressor blades. Bleed air is given that name because it is extracted from compressor of the APU i.e. air is bled off hence the name ‘bleed air’. It is compressed air that can be supplied to the air starter motor to start the jet engine.
In this way, an auxiliary power unit (APU) makes an aircraft self sufficient in engine startup mechanism.
It is important to mention here that an aircraft can have a faulty APU but still fly because as per international regulations, aircrafts are not grounded solely on the basis of unserviceable APUs.
Under such a case, airline ground staff or ground handling agency is communicated about APU unserviceability well before time to make sure that air start unit is arranged at the time of departure i.e. air start unit becomes necessary when an aircraft is flying with an unserviceable APU.
Use of Air Start Unit for Air Conditioning
Air Start Units can also be used as substitutes of Pre-Conditioned Air (PCA) units to provide onboard air conditioning. ASUs have an operating mode for air conditioning on their control panel that changes the pressure and air flow settings at the output of the ASU and makes it suitable for aircraft’s air conditioning.
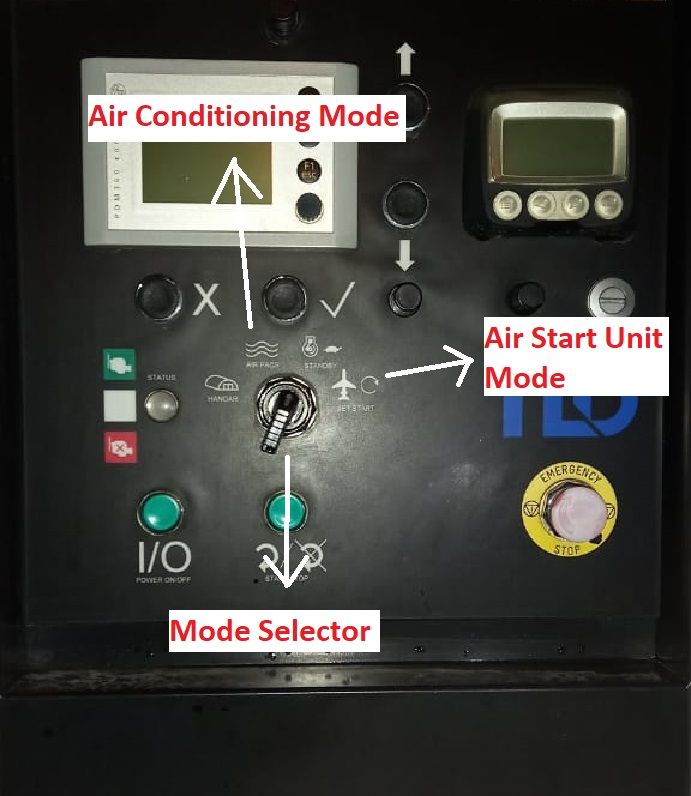
It is once again an interesting question that how can an air compressor be used to provide air conditioning to the aircraft?
The answer lies in understanding the air conditioning system of the aircraft.
Aircrafts do not have the traditional air conditioning system used in offices, homes or your automobile. The onboard air conditioning is controlled by what is referred to as an air conditioning ‘pack’. Airliners generally have two of these ‘packs’ for fulfilling air conditioning requirements and redundancy.
A ’pack’ is a package of components that makeup an air conditioning unit. This unit comprises heat exchangers, an air compressor and an expansion turbine.
An air conditioning pack receives bleed air from any one of the jet engines or the APU. The ultimate purpose of the pack is to reduce temperature of this bleed air to make it suitable for introduction into the cabin.
For this purpose, it is passed through a heat exchanger, an air compressor and an expansion turbine, collectively called an “Air Cycle Machine”.
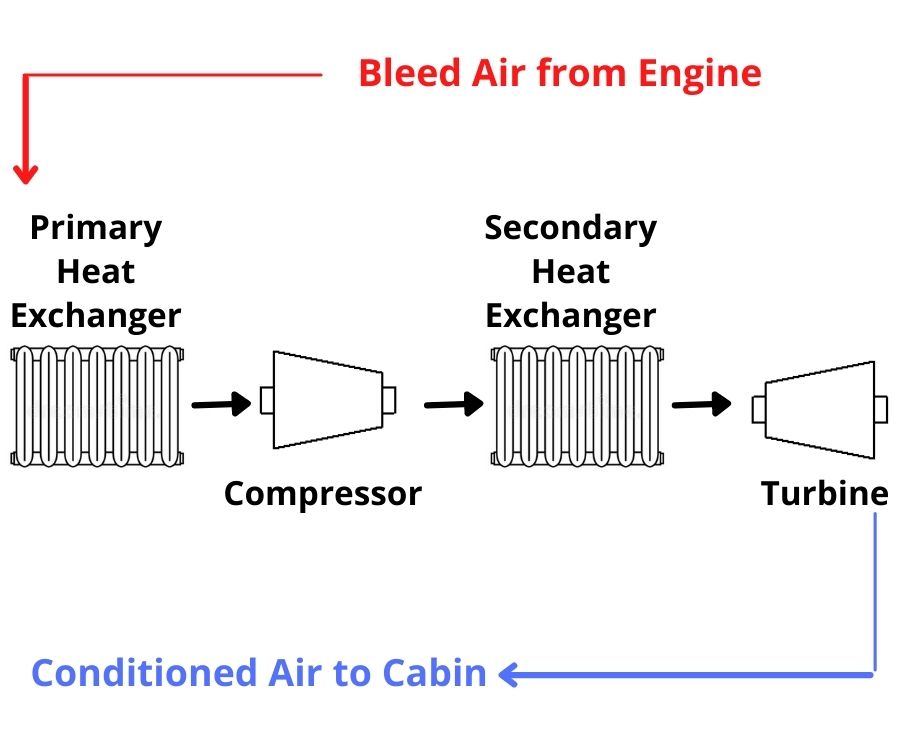
The heat exchanger uses ambient air to drop the bleed air temperature before supplying it to compressor (otherwise it will be harder for the compressor to compress the already hot air). Compressor compresses this bleed air that raises its pressure to make it ready for the expansion turbine.
However, temperature inevitably gets raised during the compression process for which a secondary heat exchanger is installed that uses ambient air to cool down the bleed air to a temperature a little above the ambient temperature. At this point, the bleed air has low temperature and high pressure. It is ready to enter expansion turbine.
The turbine expands the air that cools the air down as it passes through the turbine such that at the exit, it can reach subzero temperature. This cold air is used for air conditioning in passenger compartment, cockpit and cooling of temperature sensitive electronic systems on the aircraft.
If you are wondering where the air start unit comes in all this, the bleed air from where the whole process started is compressed air as already discussed earlier in this topic. Sources of bleed/compressed air include the main jet engines, the APU or the air start unit.
This is where air start unit plays its role. It has air conditioning mode that adjusts the output pressure of the ASU to make it suitable for entry into air cycle machine through a dedicated receptacle in the aircraft for ground connection of ASU hose.
In this way, an air start unit not only starts the main jet engine of an aircraft but can also be used for air conditioning.
Safety Precautions in Aircraft Air Start Unit Operation
The very first thing you’d notice if you have never experienced an air start procedure before, is that how loud the operation is. The loudness of air start unit is next only to the jet engines themselves. That is why the very first safety aspect is that air start crew must always wear hearing protection.
Since the air start unit kickstarts the engine, the ground crew itself must make sure that there is no object or person in the jet engine’s ingestion danger zone nor in its jet blast zone.
Pilots cannot see the jet engine hazard zones clearly and their go ahead for the engine startup procedure is based on their readiness inside the cockpit. That’s why their go ahead must not be taken as go ahead for turning on the air start unit immediately. It is imperative that ground crew make sure there is no one in the danger zones.
Secondly, although apparent, air start unit must always be positioned on the opposite side of the jet engine it is starting. That is because of the obvious reason that the air start crew themselves and the air start unit are well away from the engine that is about to come to life.
Crew must also observe care when disconnecting the air hose from the air start access panel generally located under the aircraft. Safe distance from the rotating jet engine is critical in air start procedure.
Since air start is one of the last procedures before pushback, pushback crew must resist the temptation to begin the pushback while air start unit has not been carried away from the ramp. Pushback must begin only after air start unit has vacated the ramp.
Last but not the least, maintenance teams have a great responsibility in ensuring ramp safety when it comes to air start procedure. Air start units are high pressure air compressors and a poorly maintained air compressor operating at the pressures at which air start units operate is dangerous for everyone around it. Maintenance teams must always ensure that the pressure relief valve and the air fittings are well maintained.
Innovative Engine Start Mechanism on a Boeing 787
The Boeing 787 series of aircrafts are different from conventional aircrafts in the area of engine startup as well as overall electrical design. The 787 series features more electrical controls in a ‘no-bleed architecture’ that refers to design of aircraft sub-systems to minimize the use of bleed air.
In this system, the engine startup mechanism is also made possible with the help of electrical power. Boeing 787 series of aircrafts can start their engine using electrical power from the APU or even the 400 Hz Aircraft Ground Power Units.
Jet engine on Boeing 787 can be started by using electrical power supplied by a minimum if two ground power units of 90kVA capacity each, however, Boeing recommends connecting three 90kVA units during engine startup to prevent interruption in cabin lighting, entertainment systems and ventilation.
With this we conclude our topic. If you liked our article, please do share it with likeminded people as it helps our efforts to reach people who can benefit from this information.
If you are interested in obtaining a base level knowledge about all the different types of aircraft ground support equipment and operations, Check out this 3 Hour video based course on Udemy that explains each of nearly 20 different aircraft ground support activities and equipment.
Or, if you are interested in obtaining a base level knowledge about ramp safety, check out this 7-hour video based course on Udemy that you can easily finish in a week (or binge watch in a day or two). It explains ramp safety in detail with interesting case studies of ramp accidents for in-depth understanding of the subject. It also explains ramp safety aspects associated with 13 main ground handling operations carried out on the ramp.