Preconditioned Air Units, or simply PCA units, are giant air conditioners that provide comfortable environment inside an aircraft when the aircraft’s own air conditioning system is not switched on.
Preconditioned Air (PCA) Units supply fresh conditioned air having comfortable temperature and humidity to aircraft cabin when the aircraft is parked on the aircraft stand (or ramp).
A Preconditioned Air (PCA) unit is not so different from the air conditioner you have at home. It just has a much larger capacity to cope with the air conditioning requirement of commercial airliners.
However, unlike domestic air conditioners that recirculate a lot of air, PCA units generally don’t recirculate any air. They supply only fresh air to the aircraft after dropping its temperature, if it is summer season or, raising its temperature, if it is winter season.
A Look at Airconditioning Load of an Aircraft
In order to understand the utility of Preconditioned Air (PCA) units, we need to look at the air conditioning requirement of airliners.
A narrow body aircraft like an Airbus A320 has the capacity to carry more than 100 passengers onboard. A wide body aircraft like a Boeing 777 can carry more than 300 passengers. The Jumbo Jet (Boeing 747) or Airbus A380 can carry more than 500 passengers onboard.
Moreover, the seating arrangement in an aircraft is not very spacious. If an airliner’s economy class seating is replicated at home, you would easily fit 20-30 people in an average sized bedroom. Put that many people in a room without an air conditioner and we leave the rest to your imagination.
Apart from above, there are many electrical appliances running in an aircraft especially in galleys where onboard meals are stored and prepared. Moreover, adequate temperature is required to be maintained inside cockpit for ensuring smooth functioning of electronics.
All of the above factors make it necessary to have an arrangement of air conditioning inside the aircraft at all times irrespective of whether the aircraft engines are running or not.
When is Preconditioned Air needed?
The air conditioning system of an aircraft is dependent on its jet engines or auxiliary power unit (APU). As long as the aircraft is in flight, these power sources run the air conditioning system to keep the environment inside cabin comfortable.
When an aircraft lands and finally reaches the aircraft stand (or ramp), these power sources are turned off. However, requirement of air conditioning remains because passengers are still inside the cabin and it takes time for them to exit the airplane through jet bridge.
Moreover, if the aircraft is left without air conditioning until its departure time, passenger cabin will become too hot in summers and too cold in winters for the passengers of departure flight.
Apart from above, airline staff also works inside the aircraft for different cleaning and servicing tasks to make the aircraft ready for its turn round for the next flight.
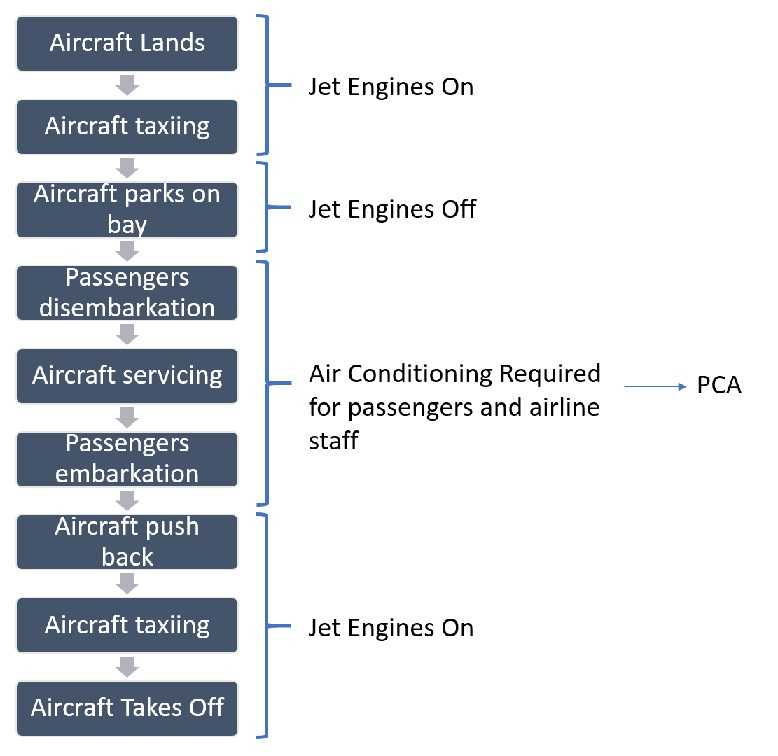
All of the above reasons make it necessary for an air conditioning system to keep running as long as the aircraft remains on ramp. Therefore, as aircraft approaches the ramp, Pilots have three options to keep air conditioning running after jet engines are turned off,
- Keep Auxiliary Power Unit (APU) on.
- Ask ground staff to connect Preconditioned Air.
- Ask ground staff to connect Air Start Unit (ASU).
The use of Auxiliary Power Unit (APU) is discouraged because it creates noise and emissions – both factors viewed negatively in heavily regulated aviation industry. An air start unit (ASU) is used primarily for engine startup therefore it is also not preferred for air conditioning.
This is where a Preconditioned Air (PCA) Unit comes in. The concept is to connect an external air conditioner into the air distribution network of the aircraft so that when the aircraft’s own air conditioning system is turned off, a comfortable environment inside passenger cabin is maintained.
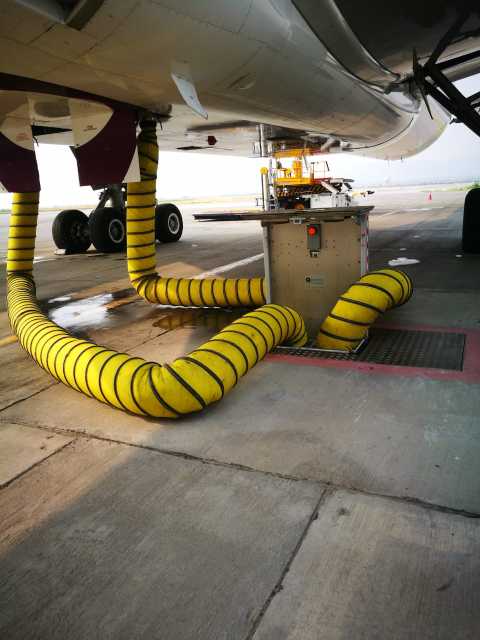
What’s with the name “Preconditioned Air”?
An interesting question to discuss here is why is it called “Preconditioned Air Unit”? Why not simply air conditioner? After all, it is nothing but a large capacity air conditioner supplying air directly into the conditioned air distribution system of the aircraft.
We will have to enter the HVAC terminologies to understand the reason behind the name “Preconditioned Air”.
In HVAC (Heating Ventilation & Air Conditioning) engineering, the space which is required to be cooled or heated is called “conditioned space” to differentiate it from the outside atmosphere.
An air conditioner is a machine that takes air from the outside, filters it for any impurities and changes its temperature and humidity required for achieving and maintaining desired atmosphere inside the conditioned space.
The properties of the outside air change when it passes through the air conditioner i.e. its impurities are removed and its temperature and humidity are dropped. This air that is now ready to enter the conditioned space is called “conditioned air”.
In an aircraft’s case, aircraft’s interior is the conditioned space and the internal air conditioning system supplies the conditioned air that flows in the air distribution network of the aircraft.
Preconditioned Air is given that name because from an aircraft’s perspective, the air being supplied by Preconditioned Air (PCA) Unit does not need treatment from aircraft’s internal air conditioning system i.e. the air being received is already conditioned. Hence the name “preconditioned” air.
Preconditioned air has already gone through all stages of air conditioning and is ready to be distributed inside the aircraft for maintaining comfortable environment in passenger cabin.
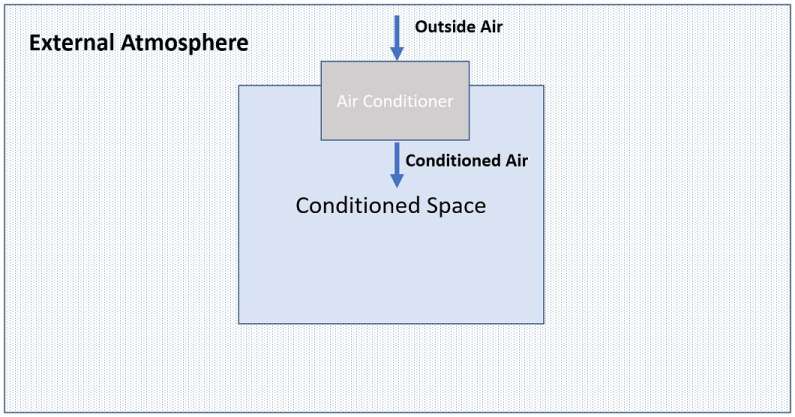

Why PCA Unit is needed when AGPU is already there?
Another important question is that when aircraft ground power unit (AGPU) is already connected to an aircraft, why doesn’t the aircraft use AGPU’s power to run onboard air conditioning system. Why is there a separate machine i.e. Preconditioned Air (PCA) Unit for air conditioning?
The answer lies in studying how aircraft’s own air conditioning system works. We have also discussed the aircraft’s internal air conditioning system in our post on Air Start Unit (ASU) and we would recommend giving it a read to understand the matter in more detail.
In short, Aircraft’s internal air conditioning system does not run on electricity like the air conditioning systems used for residential applications.
The onboard air conditioning of an aircraft is controlled by air conditioning ‘pack’. Airliners generally have two of these ‘packs’ for fulfilling air conditioning requirements and redundancy.
A ’pack’ is a package of parts and components that makeup an air conditioning unit of the aircraft. This unit comprises heat exchangers, an air compressor and an expansion turbine collectively called “Air Cycle Machine”.
Air Cycle Machine does not operate on electricity. Therefore, it cannot be powered up by the electrical power supply received from AGPU.
Please recall the concept of conditioned air discussed a few paragraphs earlier. Air cycle machine is responsible for converting air received from a source into conditioned air that is finally supplied inside passenger cabin.
It is interesting to learn that this source air that the air cycle machine turns into conditioned air is actually not the external air received from the altitude at which an aircraft is flying. The source of this air is an aircraft’s jet engine and it is called bleed air i.e. air that has been bled off from a jet engine and supplied to air cycle machine.
At first it appears counter intuitive that air that needs to be supplied to passengers is actually coming from the jet engine because a jet engine is all about high temperatures, combustion and thrust. However, that is actually the case.
An air conditioning pack (or air cycle machine) receives bleed air from any one of the jet engines of the aircraft or its auxiliary power unit (APU). This air has high temperature and pressure and cannot be used for air conditioning in it raw form.
Air cycle machine passes this air through different stages of heat exchange and expansion to drop its temperature and make it suitable for air conditioning.
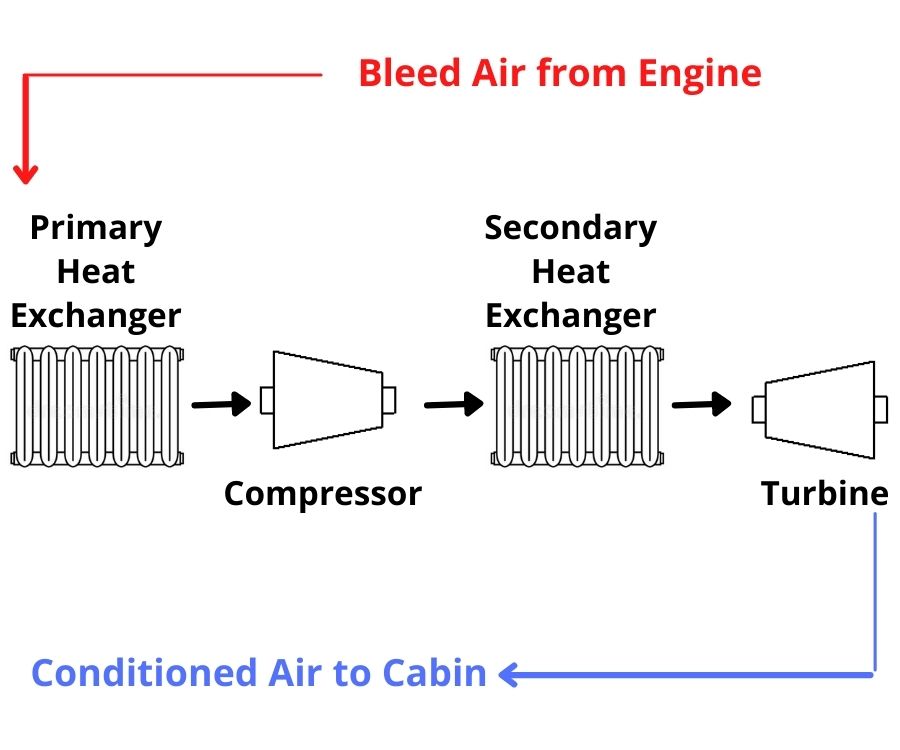
Types of Preconditioned Air (PCA) Units Based on Power Source
Now that we have developed concept of what preconditioned air is and why a preconditioned air (PCA) unit is needed, let’s look at different types of Preconditioned Air (PCA) units available in the market.
On the basis of power source, Preconditioned Air (PCA) units are categorized into two types,
- Engine driven Preconditioned Air (PCA) Unit
- Electric Preconditioned Air (PCA) Unit
Let’s briefly look at both types.
Engine driven Preconditioned Air (PCA) Unit
Engine driven Preconditioned Air (PCA) Units are powered by an internal combustion engine, generally a diesel engine. The engine drives a generator to generate electricity that is used to power up the HAVC refrigeration compressors of PCA unit.
These units are the conventional units that have been used at airports since long. A comparatively advanced technology in engine driven PCA units is direct drive technology in which the engine directly drives the refrigeration compressor and removes the electrical generator from in between.
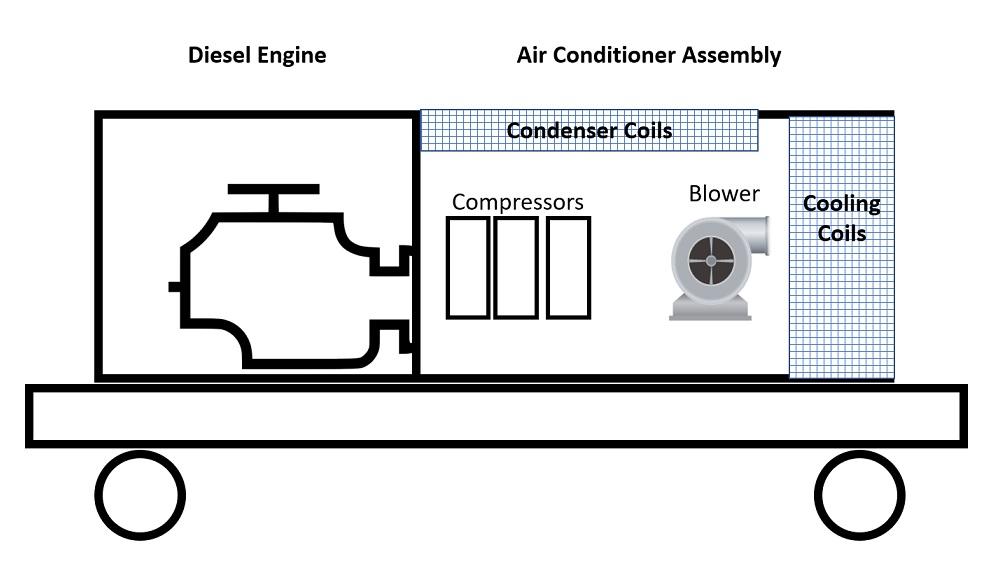
Electric Preconditioned Air (PCA) Unit
An electric preconditioned air (PCA) unit runs on utility power supply. It receives electrical power as input from airport building power supply. All of its compressors and internal circuitry is powered by this power supply.
Electric preconditioned air (PCA) units have no emissions on ramp and are generally more efficient in energy consumption that engine driven preconditioned air (PCA) unit. Moreover, they also have less operating noise due to which they are preferred over engine driven preconditioned air (PCA) units.
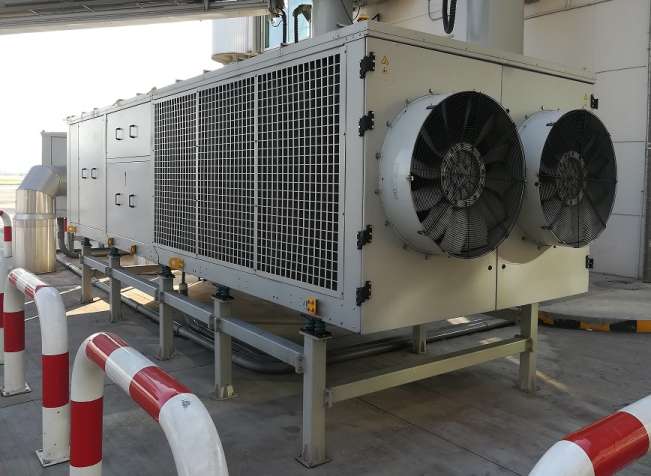
Types of Preconditioned Air (PCA) Units Based on Installation
Apart from the power source, there are three types of Preconditioned Air (PCA) units based on the type of their installation,
- Bridge mounted
- Fixed on ground (also known as apron mounted)
- Mobile PCA Units
Bridge Mounted Preconditioned Air (PCA) Units
As the name suggests, bridge mounted PCA units are installed on the jet bridge. They hang under one of the telescopic tunnels of the bridge with the help of special mounting frame or supports. Some configurations can also have PCA unit mounted over the bridge instead of under it.
Generally, bridge mounted PCA units are electric PCA units. Engine driven PCA units are not installed under the bridge because they have tendency to produce more vibrations that is not desirable for the integrity of the jet bridge.
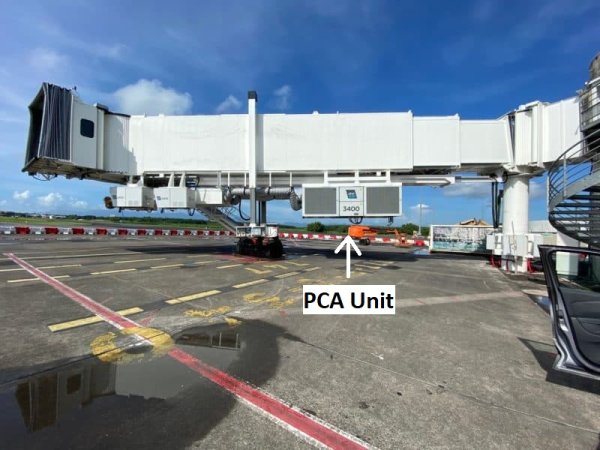
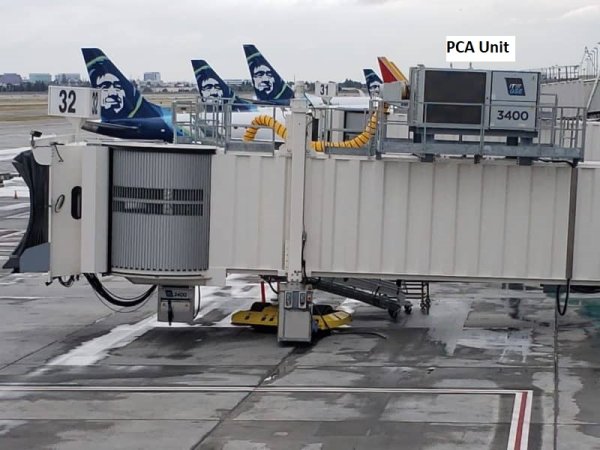
Fixed On-ground Preconditioned Air (PCA) Units
If PCA unit is not installed under the bridge, it will be fixed on ground. Such PCA units are installed on the aircraft stand (ramp) and are generally electrically powered.
The supply air reaches the aircraft from the PCA unit in any one of the following ways,
- Underground pipe opening into a utility pit system carrying conditioned air from PCA unit to the aircraft with the help of a pipe installed in a trench on the apron.
- A duct or pipe installed under the jet bridge that receives conditioned air from the PCA unit, runs it through the entire length of the jet bridge tunnels and terminates with a flexible hose that is connected with the aircraft.
Mobile Preconditioned Air (PCA) Units
Mobile PCA units is a PCA unit mounted on a cart that can be towed to any desired location or installed over a truck chassis that goes wherever the truck goes. These units have all of their components assembled over a platform mounted on cart or truck chassis with a tray for holding the PCA hose.
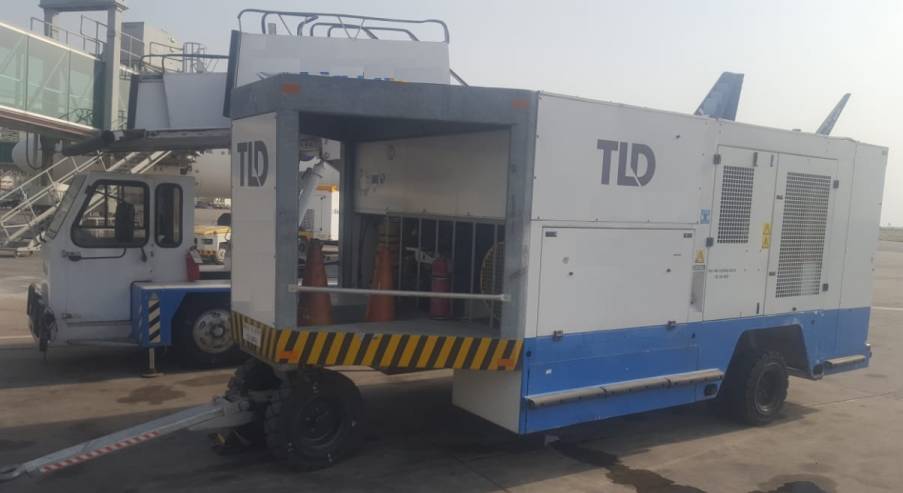
How Type of Preconditioned Air (PCA) Unit is Selected?
Now that we understand the different types of Preconditioned Air (PCA) units, let us compare them and learn what factors are involved in making a decision on the type of PCA units to be chosen for an airport.
The type of PCA units chosen for an airport is given consideration at the design and planning stage of airport development. Engineers and consultants need to design aircraft stands by looking at factors such as energy efficiency, emissions and environment, space utilization and operations efficiency.
Energy & Environmental Considerations
Energy efficiency and environmental considerations play a pivotal role in deciding whether PCA units used at an airport are diesel engine driven or electric. Electric PCA units are becoming more and more common in response to stringent aviation regulations on environmental preservation.
Moreover, electric PCA units are also more efficient from an energy efficiency point of view. Production of energy in bulk is always cheaper than producing localized energy onsite for a specific piece of equipment. Consequently, electric PCA units utilize power coming from the building instead of generating power onsite like diesel engine driven PCA units.
Redundancy & Flexibility in GSE Operations
Every airport has a certain number of contact stands i.e. aircraft stands where jet bridges are installed to connect the ramp and the aircraft parked on it directly with the airport building.
A certain number of remote stands are also available at all major airports that don’t have a jet bridge facility and direct connection with the airport building, however, remote stands are necessary for incorporating redundancy at the airport for accommodation of flights during peak hours. Remote stands may also be used by airlines not willing to use jet bridges.
Fixed on-ground or bridge mounted electric PCA units are the go to choice for contact aircraft stands because these stands remain busy throughout the day accommodating different flights assigned to the aircraft stand.
Fixed on-ground remote stands are not generally fitted with PCA units. For accommodating flights on remote stands, engine driven mobile PCA units are used because they offer far greater flexibility in terms of airport management.
Mobile PCA units don’t require any electric power source therefore they can be towed anywhere on any aircraft stand without the concern of availability of power. This mobility allows airport management to deal with equipment issues with greater flexibility.
For example, if the contact stand’s own PCA unit has become faulty, airport management would still be able to provide PCA facility to the incoming aircraft by quickly moving a mobile PCA unit to that stand as contingency.
Similarly, a group of a few mobile PCA units can be used for accommodating various remote stands by moving them from flight to flight. This flexibility is not available with fixed or bridge mounted PCA units. If aircraft stand is not being utilized, fixed or bridge mounted PCA units will remain unused without the ability to be moved to another stand where there is requirement for PCA unit.
Due to the above reasons, airports neither go for all fixed/bridge mounted PCA units in their inventory nor for all mobile units. A mix of both types is kept to cater to different scenarios and flight schedules.
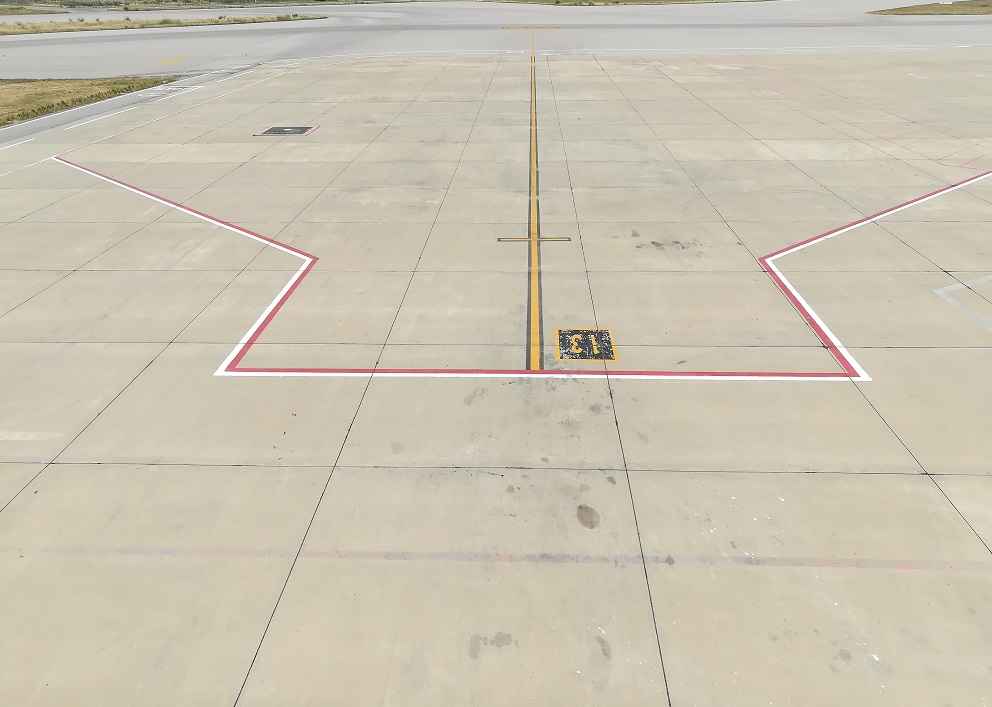
Ease of Maintenance
Routine maintenance, breakdown maintenance and troubleshooting is a major consideration for airport management. In order to ensure maximum uptime of all facilities, airport facilities have to be designed maintenance friendly.
In this regard, Mobile PCA units are again the most advantageous because their maintenance is not hindered by flight operations or location constraints. They can be moved to any location, such as a workshop, for maintenance activities while the other mobile units cater to flight operations.
Fixed on-ground PCA units comes second because they can be serviced without interrupting flight schedule. They are generally installed on one corner of the aircraft stand where maintenance personnel and technicians can undertake disassembly and servicing tasks while a mobile PCA unit serves flights.
However, there is one constraint. Maintenance teams will have to bring tools to the site where maintenance activity is to be performed – a limitation not present with mobile units that can be moved in a workshop for maintenance. This constraint becomes most noticeable when major overhauling needs to be done.
It is easier to assemble and disassemble heavy duty compressors and motors of PCA units inside a workshop than to arrange forklift trucks and cranes on an aircraft stand – that sometimes hinders flight operations as well.
If fixed on-ground PCA units are used with utility pit systems, it becomes difficult for maintenance team to find and fix air leaks in the system since a large part of the duct in underground.
Moreover, during flight operations,, maintenance teams can face distraction and disturbance in their work on PCA units due to the busy nature of ramp at the time when ground support operations are in their full bloom.
Bridge mounted PCA units are least preferred from maintenance aspects.
First, they are mounted under a bridge and maintenance teams cannot access different parts of the PCA units for servicing and maintenance without a ladder or elevated platform.
Secondly, no maintenance activity can be performed on bridge mounted PCA units when there is an aircraft parked on the bay and ground support operations are underway. You will have to wait for the ground support operations to complete and the jet bridge to become vacant to be able to work on the PCA unit hanging under the bridge.
Apart from above, both bridge mounted and fixed on-ground PCA units have another constraint. Maintenance teams cannot perform maintenance on these units during bad weather conditions for example when it is raining or during a windstorm.
You cannot just open up electrical cabinets of PCA units and disassemble different parts while it is raining, snowing or there are heavy gusts of wind. It becomes a safety hazard.
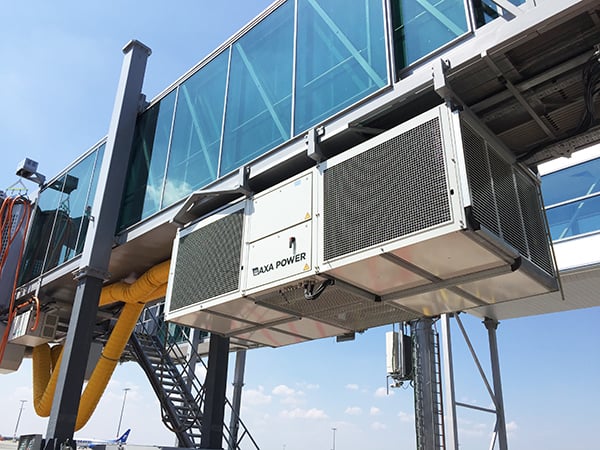
Space Preservation & Ramp Safety
Since ramp becomes a busy place during aircraft operations where various ground support operations are performed, space preservation is also an important aspect when selecting the type of PCA unit to be installed on the aircraft stand.
Bridge mounted PCA units are preferred in this regard because they don’t have any footprint on ground. The space unoccupied by PCA unit becomes available for movement of other ground support equipment by freeing up space on ramp.
This freeing up of space is not only important from an operational efficiency point of view but also from safety point of view. The more men and machine are present on the ramp, the greater the chances of any accident. By making ramp more clutter free, ramp operations become safer as well.
Fixed on-ground PCA units can be equally beneficial in this area if utility pit systems are used with them. Utility pit system allows PCA hose to popup from underground just near the aircraft instead of laying on the ramp for vehicles to accidently run them over.
Mobile PCA units are least effective in this area because they have to be towed to the ramp by a towing tractor and towed off the ramp at flight departure thereby creating most movement. Moreover, they remain positioned close to the aircraft and add to the crowd of people and vehicles at the ramp.
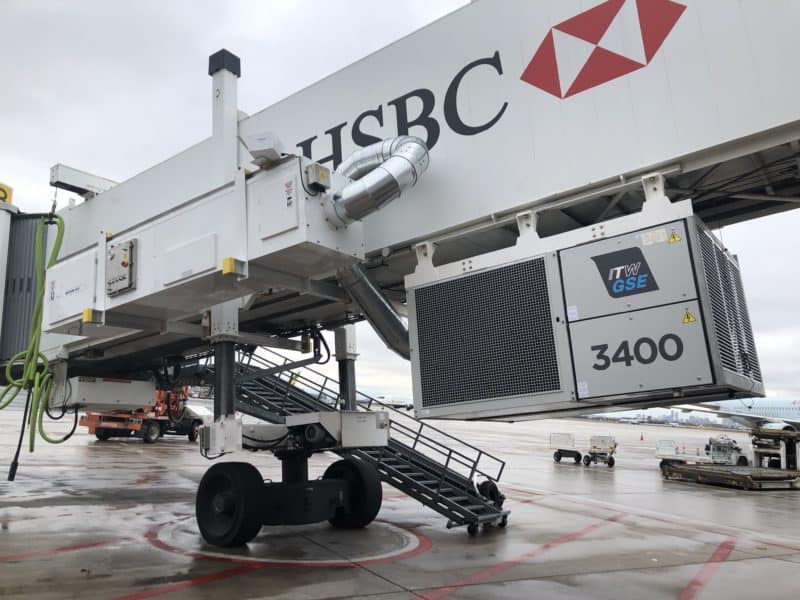
Cost of Installation
Mobile PCA units don’t bear any cost of installation, however, fixed on-ground type PCA units and bridge mounted PCA units do have installation costs.
Bridge mounted PCA unit needs to be installed under the bridge with the help of supports and a support for PCA hose also needs to be provided. Moreover, a PCA hose trolley is fitted in front of jet bridge bogie that stores the PCA hose. When jet bridge is engaged, PCA hose is extracted from the trolley and engaged with the aircraft after which PCA unit is turned on.
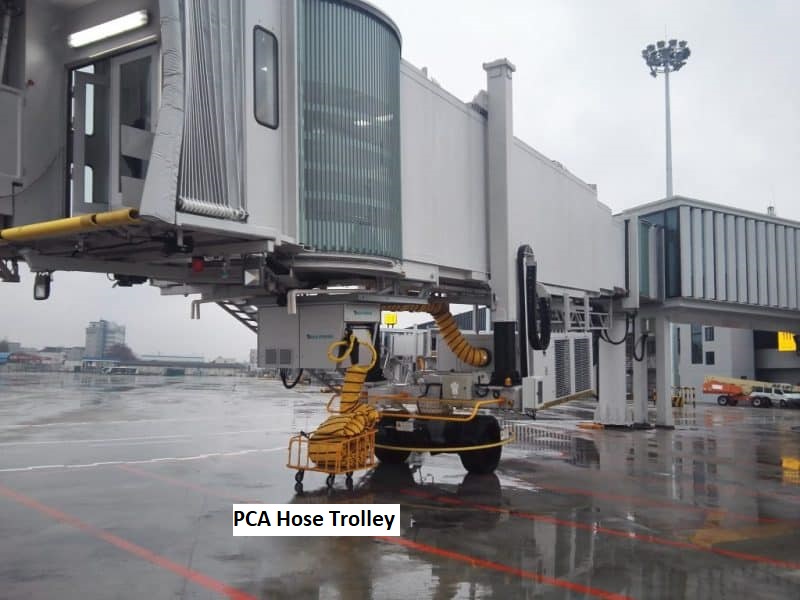
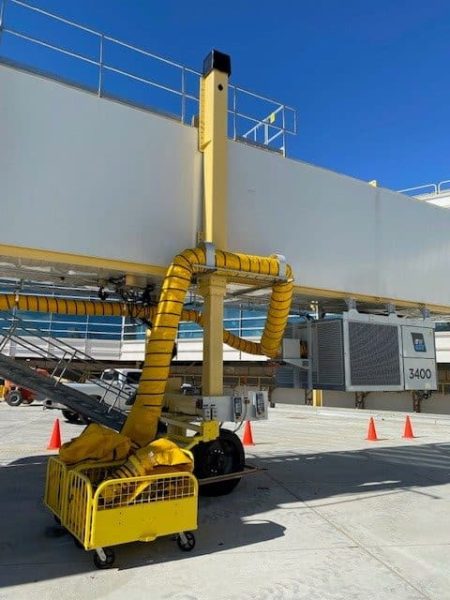
Fixed on-ground type PCA unit has a foundation built on the apron that comprises vibration dampening elements. The main challenge is to carry the hose to the aircraft. There can be two ways in which it can be done.
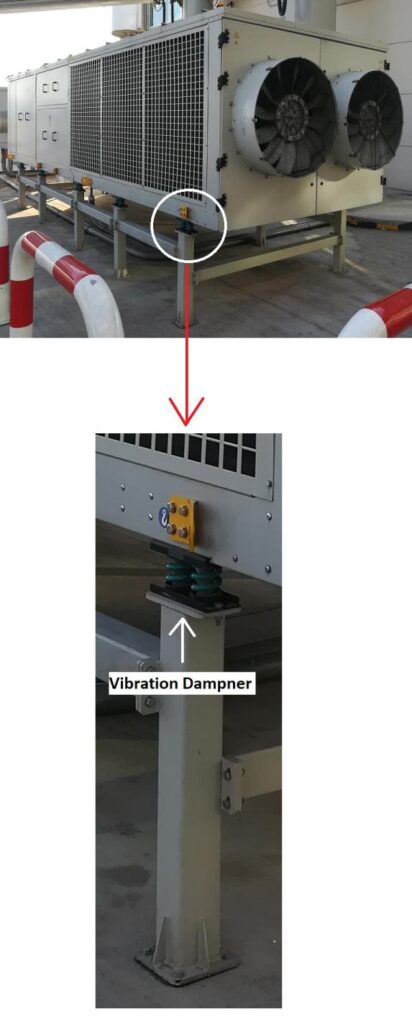
The first way is the less expensive way in which the PCA hose runs through a pipe installed under the jet bridge and exits under the jet bridge cabin with trollies installed in front of jet bridge bogie carrying extra length of the hose.
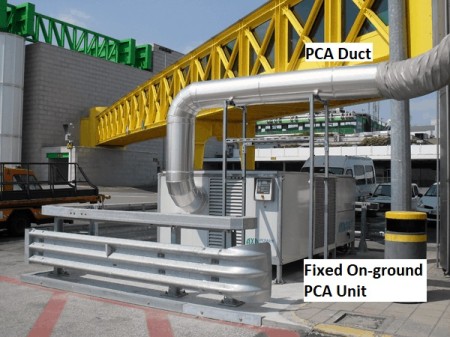
The second way is connecting the PCA unit with a utility pit system. This is most expensive as lots of civil work is involved in making an underground room for installation of utility pit and laying an HDPE pipe in a trench from PCA unit to the utility pit.
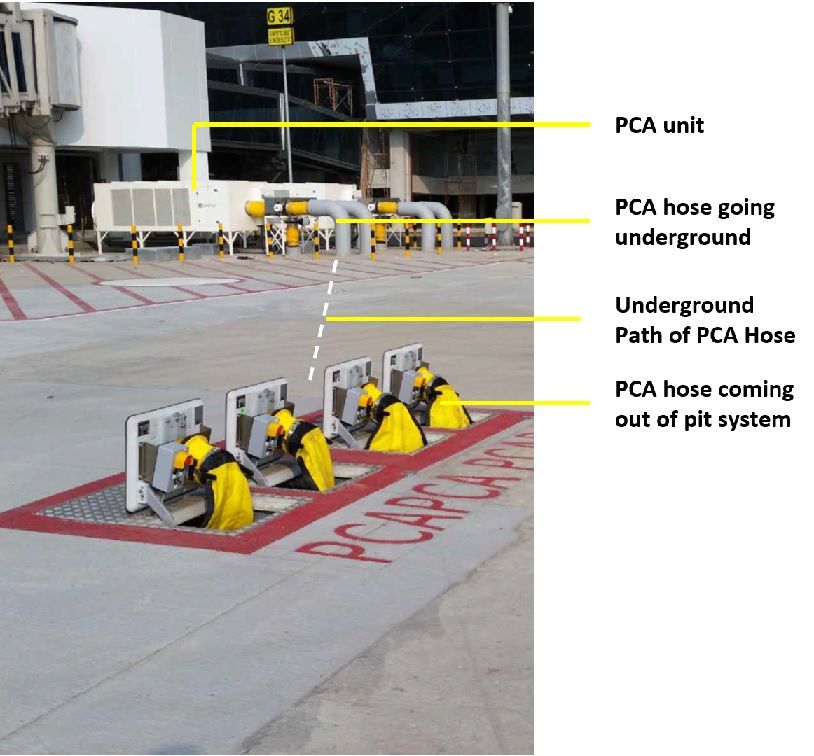
PCA units installed under or over passenger boarding bridges have the convenience of getting near to the aircraft as the bridge moves forward. Once the bridge has been engaged, supply air hose is connected with the aircraft and PCA is turned on.
How Capacity of PCA Unit is Decided?
The choice of PCA unit to be installed on an aircraft stand is dependent upon the largest aircraft that the stand is designed to support. Narrow body aircrafts can easily be serviced by a single PCA unit installed on the bay. Accordingly, narrow body aircrafts only have a single PCA receptacle for ground connection.
The capacity for narrow body aircrafts can be around the range of 40 TR (Ton of Refrigeration) to 60 TR depending upon the climate of the airport where PCA units are installed.
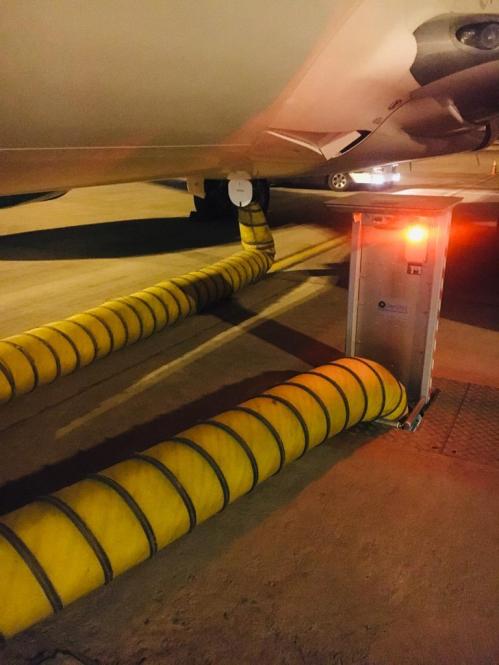
Wide body aircraft have a higher air conditioning load. For servicing these aircrafts, multiple PCA units or a single large PCA unit may be required to be installed at the bay. Accordingly, wide body aircrafts have two PCA receptacles for ground connection. However, Airbus A380 has four PCA receptacles for meeting its air conditioning load.
A single 90 TR capacity PCA unit or multiple 60 TR capacity PCA units may be installed on such aircraft stands.
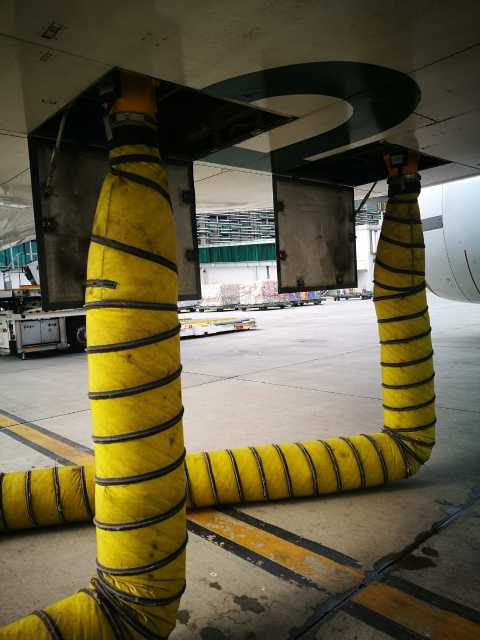
Again, the capacity of PCA units is greatly dependent upon the climate of the country in which PCA units are installed. Places where summer temperatures are extremely hot require more capacity from the PCA units than a coastal area where temperatures remain comfortable throughout the year.
With this we conclude our topic. If you liked our article, please do share it with likeminded people as it helps our efforts to reach people who can benefit from it.
If you are interested in obtaining a base level knowledge about all the different types of aircraft ground support equipment and operations, Check out this 3 Hour video based course on Udemy that explains each of nearly 20 different aircraft ground support activities and equipment.